Kipp&Zonen Brewer MkIII User Manual
Page 22
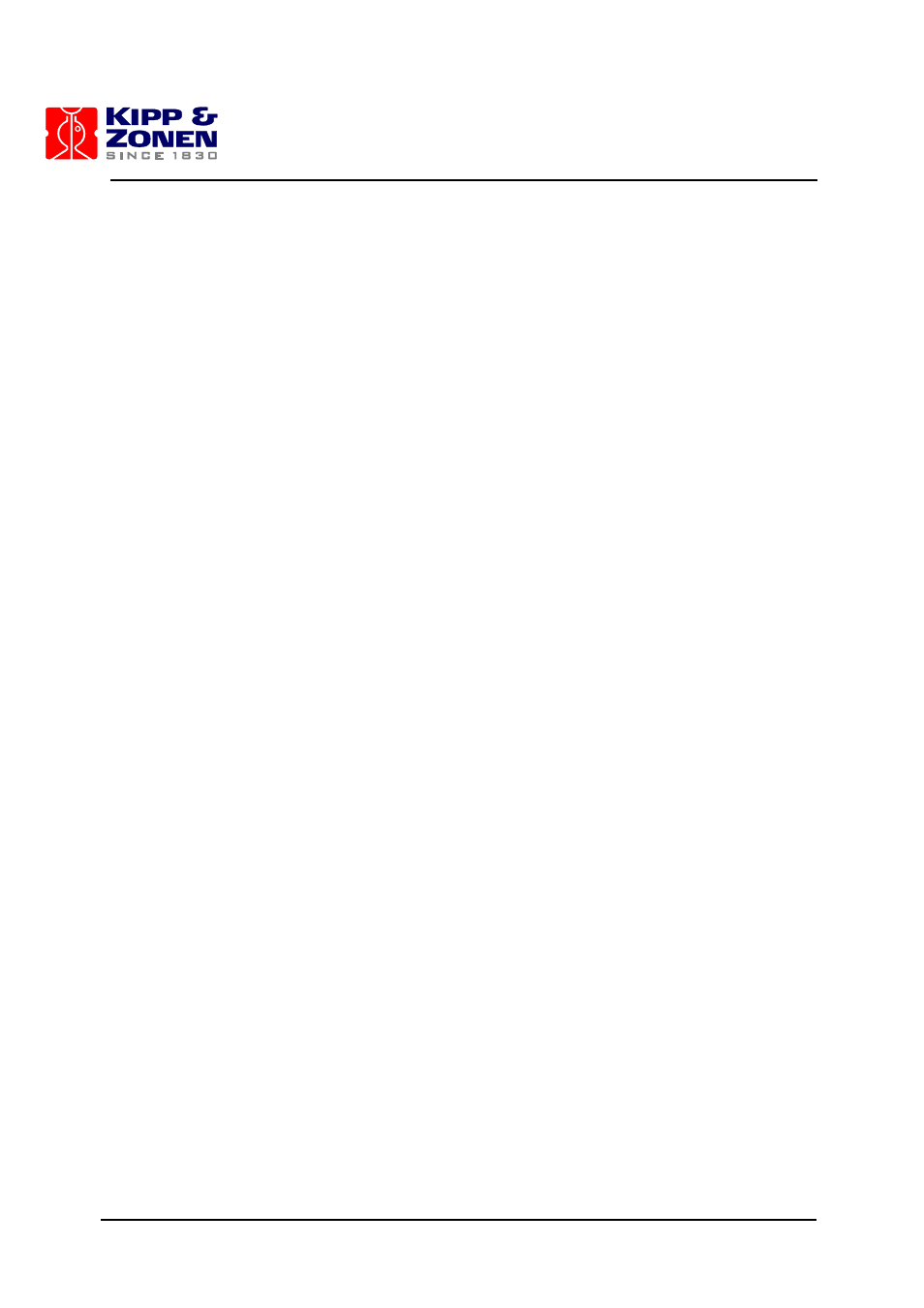
MKIII SERVICE MANUAL
17
If these signals are normal, consult KIPP & ZONEN before proceeding further. If any of the signals
are missing or are not clean square waves, replace this board.
11. Contact KIPP & ZONEN
If all of these tests fail, there is a probable fault in the PMT, and KIPP & ZONEN should be
contacted before proceeding.
4.8
STEPPING MOTOR CONTROL
The stepping motor control circuitry provides for the control of each stepping motor through
individual motor microprocessors and stepping motor driver integrated circuits. This type of motor
control allows the system to move the motors simultaneously, and to monitor the sensors very
efficiently. All of the motor microprocessors are controlled by the main processor through a serial
"I2C" bus. Each motor is optimized for speed and taylored to each function in the Brewer. The
configuration file is included with the control software to allow changes and updates to the system.
The configuration file is optimized for each instrument and normally does not require operator
modifications unless recommended by KIPP & ZONEN.
4.9
PHOTON COUNTER CIRCUITRY
A schematic diagram of the photon counter circuitry is given in figure 10.4-1. The photomultiplier
signal which has been amplified and divided by a line driver on the pulse amplifier board is
received by a line receiver on the Main Electronics board. This signal is fed to a pair of binary
counters. The outputs of the 2 counters are compared and if they differ by more then a set amount
the second counter is disabled and a “PMT counter failure” message is generated in the Firmware
Log. The counters are each connected to output ports which are connected to the data bus of the
system microprocessor.
The main gate is generated by an electronic circuit that provides a very precise gating signal to
enable counting for a specific length of time. The microprocessor decides when the pulse counting
circuitry is initiated and the circuitry then triggers the gate to allow counting of the photons.
4.10 HIGH SPEED AMP BOARD
The photomultiplier, and pulse amplifier board are enclosed inside the photomultiplier
subassembly. The sub assembly is designed to allow access to the pulse amplifying circuitry
without upsetting the alignment of the PMT or the optics.
The photomultiplier is an EMI 9125UVA type. It is enclosed in a magnetic shield at the high voltage
potential of the photo cathode. A small area on the shield is open to allow light to fall on the
cathode. A high voltage power supply provides stepped voltages to the photomultiplier through a
resistor divider circuit at the base of the tube. Since differential thermal expansion between the
photomultiplier glass and the PTFE base may cause tube breakage under extreme temperature
conditions, it is recommended that the photomultiplier housing never be subjected to temperatures
of less than -50C or greater than +60C.
The pulse amplifier board is located directly behind the base of the photomultiplier tube. This
circuitry accepts the photon pulse signals from the photomultiplier, amplifies them, discriminates
the signal level from current leakage, divides the amplified photon pulses by four, and finally
outputs the pulse on a line driver. Since the circuitry is extremely sensitive to feedback and RF
noise, it is located in close proximity to the photomultiplier.
4 OPERATING TEST FAILURES