4 installation – Glow-worm Inset 40BBU User Manual
Page 9
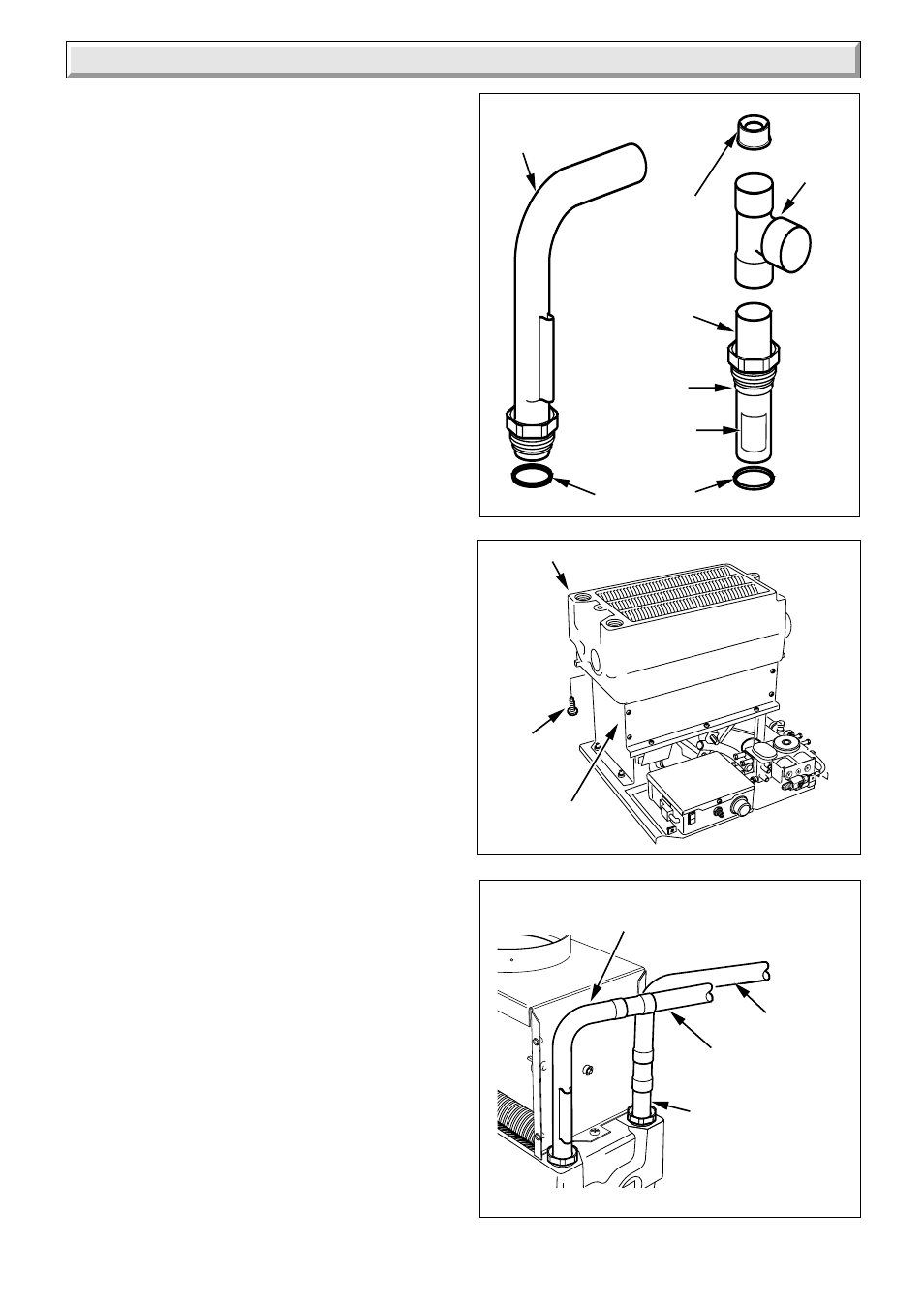
9
221722B
4 Installation
Diagram 4.2
If the heat exchanger connections are opposite hand to that
required, turn in the same manner as described in Section 4.3
paragraph 5.
4.5 Heat Shield Assembly
If the boiler electrical supply cable has to be routed down the left
hand side of the combustion chamber you must fit the heat
shield assembly supplied in the fittings pack. Refer to Section
5.1 and diagrams 5.2 and 5.3.
4.6 Circulating Pump
Isolating valves, integral if possible, must be fitted each side of
the circulating pump.
4.7 Gas Supply
The gas installation must be fitted in accordance with the
recommendations of the current issue of BS6891.
Do not use pipe of a smaller diameter than Rc
1
/
2
(
1
/
2
BSP) inlet
or 15mm, see diagram 1.1 for position of gas connection.
The gas meter must be capable of passing natural gas at the
following rates: 24.8ft
3
/h to 70.1ft
3
/h (0.7m
3
/h to 1.98m
3
/h).
This rate is in addition to all other natural gas appliances
supplied from the same meter.
It is recommended that the gas supply enters the builder’s
opening on the right hand side.
If the gas supply enters from the left hand side it will be
necessary to route the pipe behind the combustion chamber
before final fixing.
4.8 Positioning the Back Boiler
To position the back boiler lift by the heat exchanger casting and
place centrally in the builder’s opening. The installation centre
line is indicated on the base by a notch on the front of the plate
and the fire fixing wall face positioning line by the front corner
edges of the base, see diagram 4.5.
The back boiler must be positioned so that a line across the
opening of the fire fixing wall face coincides with the fire fixing
wall face positioning line, see diagram 4.5. Use a straight edge
across the fire fixing wall face to make sure that the back boiler
is square to it.
Check that the back boiler is level. If packing is required to
adjust the level of the back boiler, use metal shims and pack
under the full width of the base.
Mark through the three fixing holes on the floor protection plate,
see diagram 4.6. Remove the back boiler unit. Drill three holes
using a 5mm masonry drill bit to accept the plugs and fixings
provided.
4.9 Positioning the Back Boiler - continued
Fit the flueway baffles, ensuring that they are positioned centrally
in the flueways, see diagram 4.7.
NOTE: The front flueway does not have a baffle.
NOTE: If the heat exchanger has been turned the baffles must
still be fitted into the back and middle flue ways only.
Fit the draught diverter onto the heat exchanger with the two
securing screws supplied in the fittings pack, see diagram 4.8.
Push fit the sensing tube onto the flue blockage safety device
and draught diverter. Secure the sensing tube assembly with
the securing screw, see diagram 4.9.
Where a flexible flue liner is being used, fully fit the No8x
3
/
8
in self
tapping screw provided into the rear of the flue socket as in
diagram 4.10.
6175
HEAT EXCHANGER
SECURING
SCREWS
(4)
COMBUSTION
CHAMBER
22mm RETURN
PIPE ASSEMBLY
SUPPLIED WITH
APPLIANCE
(Do not cut)
Diagram 4.1
6254
UNEQUAL
TEE PIECE
SEALING WASHERS
INJECTOR
22mm COPPER PIPE
SUPPLIED WITH APPLIANCE
(Do not cut)
Diagram 4.3
8024
22mm
FLOW
22mm
RETURN
22mm COPPER PIPE SUPPLIED
WITH APPLIANCE
(Do not cut)
22mm COPPER
PIPE SUPPLIED
WITH APPLIANCE
(Do not cut)
Pumped Heating and Hot Water
BRAZED JOINT
LABEL