11 servicing, Attention! 11. 6 combustion check – Glow-worm hxi and Gas Valve User Manual
Page 33
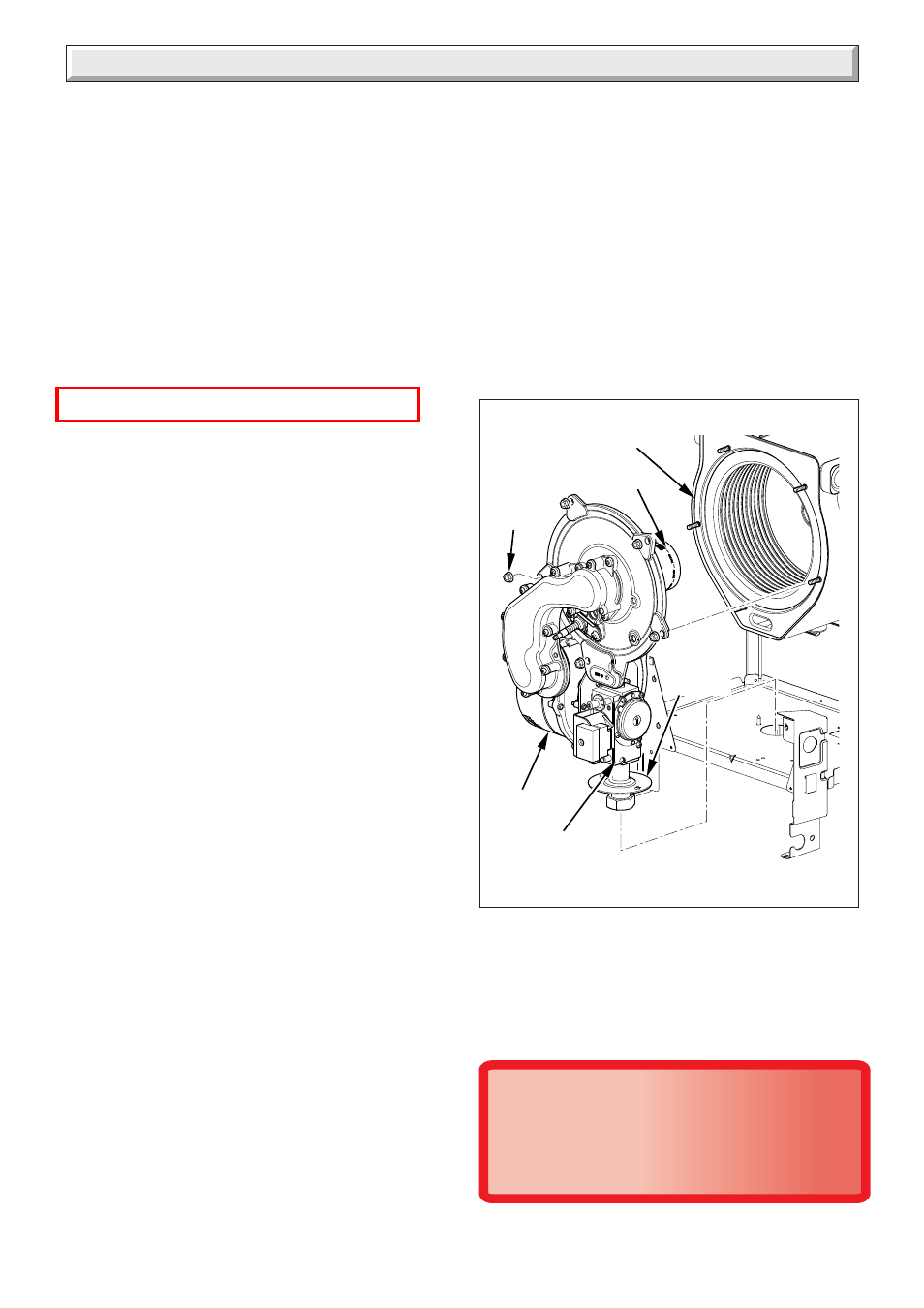
33
0020008153-05
11.4. Combustion Chamber and Heat
Exchanger.
Refer to diagram 13.3.
Remove loose debris from combustion chamber using a soft
brush and vacuum cleaner. Carefully flush by spraying water
any remaining debris through the condensate trap (Ensure the
water is kept away from electrical components).
11.5 Condensate Drain
The condense drain does not normally need removing during
servicing.
To flush the condense drain carefully pour water into the heat
exchanger and check that water flows freely to drain.
If the condense drain is blocked refer to section 13.16 for
removal.
Once the appliance has been reassembled (apart from the front
and inner casing panels) connect a CO
2
combustion analyser to
the test point on the flue
elbow, see diagram 11.6.
Turn on the gas service cock, see diagram 11.1.
With the power off and the appliance cold, unclip the controls
fascia and hinge it down to reveal the potentiometers on the rear
of the User interface, see diagram 11.7. Take care not to allow
the fascia to drop down and damage the wiring.
Turn on the electrical supply.
Ensure external controls are calling for heat. The boiler should
fire automatically.
Allow the boiler to fire for a minimum of 60 seconds and then,
using an electrical screwdriver, rotate the ‘service’ potentiometer
fully clockwise, see diagram 11.7. This will allow the digital
display to indicate the ‘flashing’ fan speed on the appliance
fascia.
In the fully clockwise position the display should be indicating
the maximum fan speed of the appliance, (27±1 for 12hxi, 32 ±1
for 15hxi, 41±1 for 18hxi, 47±1 for 24hxi and 57±1 for 30hxi and
38hxi). Check the CO
2
value, which should be 9.1% +0.2 -0.5.
Note that with the inner casing panel fitted the combustion
readings will increase slightly to 9.3% +0.3 -0.5.
If adjustment proves necessary then proceed as follows.
Any adjustment to the gas valve should only be carried out by
a competent person.
Refer to diagram 10.3.
Adjust the maximum rate CO
2
with the throttle to 9.1%. (Rotate
anti-clockwise to increase).
Rotate the ‘service’ potentiometer fully anti-clockwise. Hold it
in this position for about 5 seconds before rotating the service
potentiometer clockwise to the mid-point or 3 o’clock position.
The fan should reduce to 1200 ±100 rpm which will flash ‘12’ on
the digital display.
Check the CO
2
value which should be 9.1% + 0.2 - 0.5.
For Propane the CO
2
value should be 10.5% + 0.3 - 0.7.
Note that with the inner case front panel fitted the combustion
readings will increase slightly.
Natural gas should read 9.3% + 0.3 - 0.5
Propane gas should read 10.7% + 0.3 - 0.8
Diagram 11.5
BURNER
COMBUSTION
CHAMBER
FAN
GAS VALVE
11 Servicing
GAS PIPE
BRACKET
& SEAL
11475
SECURING
NUTS (5
OFF)
Refer to diagram 11.6
For adjustment of Propane appliance refer to section 10 (LPG
conversion).
If adjustment proves necessary then proceed as follows.
Adjustment of the CO
2
at minimum rate is very coarse so
carefully adjust the CO
2
with the offset adjustment to 9.1%, see
diagram 10.3.
Rotate the ‘service’ potentiometer fully clockwise, see diagram
11.7, and recheck the maximum rate combustion, which should
be 9.1% + 0.2 -0.5.
After checking combustion rotate the ‘service’ potentiometer
fully anti-clockwise so that the digital display indicates the water
temperature.
Replace the cap on the sampling point and refit the control cover
rear panel.