Carrier 19DG User Manual
Page 7
Attention! The text in this document has been recognized automatically. To view the original document, you can use the "Original mode".
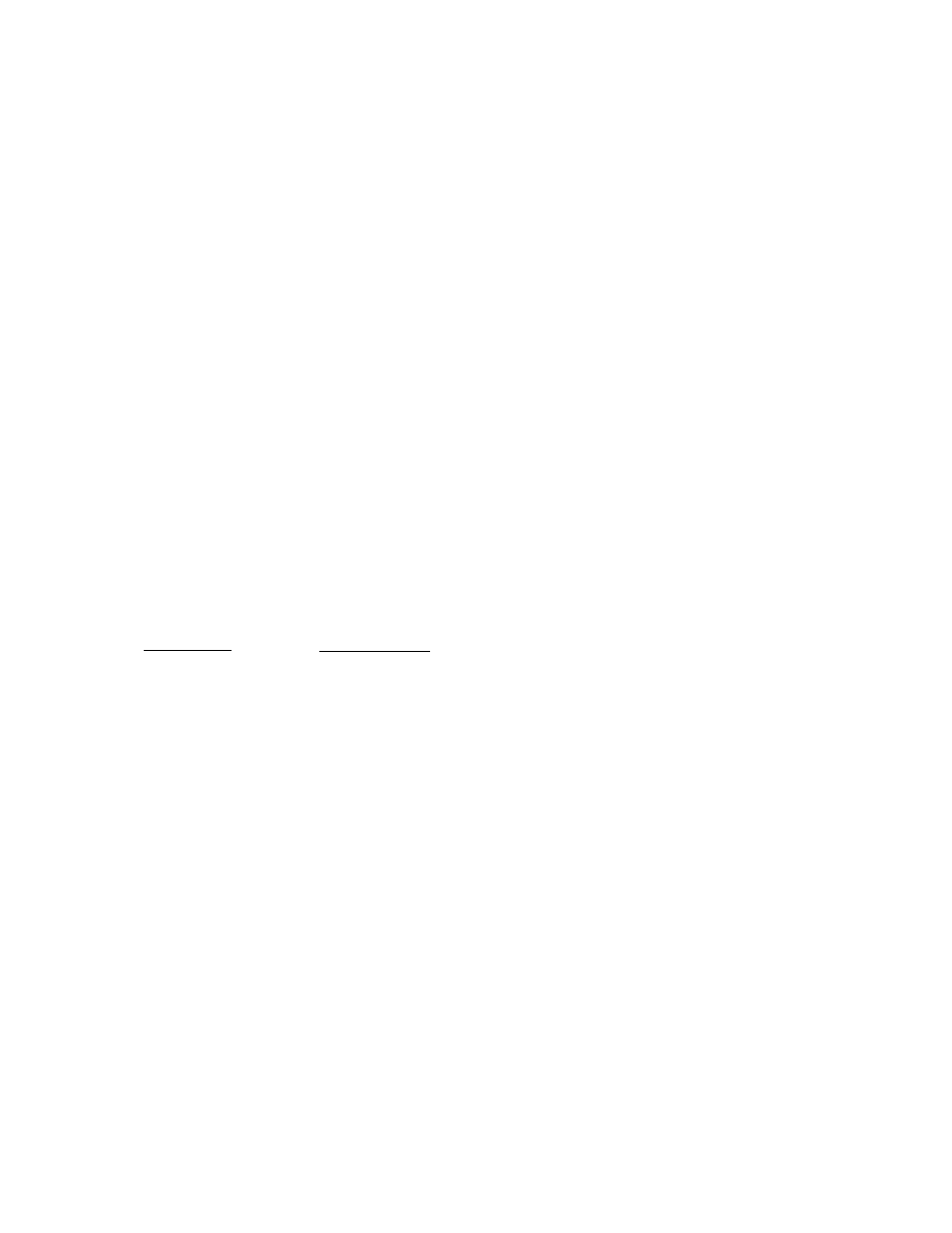
AGITATOR VALVE CHECK - The refrigerant
agitator solenoid valve is open when the compres
sor guide vanes are closed. When opening.the guide
vanes manually in the following procedure, listen
for the sound of the agitator solenoid valve closing
as the vanes reach 20—28 deg of opening.
MOTOR CURRENT CALIBRATION
1. Establish a steady motor current value for this
calibration. Open guide vanes manually (capac
ity control to “Inc”) until full load current is
reached. Motor current calibration (Eig. 3) may
have to be turned counterclockwise to permit
vanes to open further. Do not exceed 105% of
nameplate full load amperes.
If system load is sufficient to maintain full-load
current for a period of time, calibrate at this
condition. With small loads, pull down to and
maintain (capacity control to “Hold”) design
leaving chilled water temperature and calibrate
at this condition.
2. Measure motor current at selected condition
and determine its percentage of full load motor
current.
3. Use this percentage figure to set the electrical
demand adjustment (Eig. 3) per the following
table:
Setting Operating Controls
Percent of Full
Load Motor Current
105
85 or above
65 to 84
45 to 64
below 45
Electrical
Demand
Adjustment
Setting
100
percent
80 percent
60 percent
40 percent
Control cannot be
calibrated
4. Turn the motor current calibration adjustment
fully clockwise. This will cause the guide vanes
to close part way.
5. Turn thermostat (Eig. 3) to “Cooler” (fully
counterclockwise).
6. Set capacity control to “Inc” position.
7.
Slowly turn the motor current calibration
counterclockwise. Allow the guide vanes to
open until motor current reaches 5% above the
electrical demand setting.
NOTE: There is a time lag of several seconds
due to feedback capacitance in the motor
current circuit. When the motor current
calibration setting is adjusted, allow for this
time lag.
8. Check the foregoing motor current calibrations
with
machine
under
“Auto.”
control
as
follows:
a. Close vanes manually (capacity control to
“Dec”).
b.
Turn capacity control to “Auto.” Vanes
should stop opening at electrical demand
setting.
9. If control was calibrated at less than 100% load,
turn electrical demand adjustment setting to
100%. Control is now automatically calibrated
for 100% full load motor current.
This is a two-step motor current limiting
circuit. At 100% full load motor current, the
vanes will stop opening further. If the motor
current should increase to 105% due to some
change in load conditions, the vanes will close
until the motor current is reduced to about
102%. If the motor current is reduced to 98%
or below, the control will respond to leaving
chilled water temperature. The electrical de
mand adjustment allows the operator to reduce
the maximum current drawn by the motor,
minimizing the electrical demand rate during
off-season operation.
If control cannot be calibrated with above
procedure, check voltage signal from signal
resistor in starter. At 100% full load current,
voltage between terminals 23 and 24 inside
control panel must be 0.5 ± 0.1 volts. If not in
this range, check sizing of resistor in starter.
CHILLED WATER CALIBRATION
1. Turn throttle range adjustment (Eig. 3) fully
clockwise.
2. Turn chilled water thermostat (Eig. 3) until
design chilled water temperature is maintained.
Mark thermostat at this position. If capacity
control vanes hunt, turn throttle range adjust
ment counterclockwise in small increments
until hunting ceases. Chilled water thermostat
may require resetting.
TRIMMING REERIGERANT CHARGE - After
the machine has been placed in operation, it may
be necessary to adjust the refrigerant charge for
optimum machine performance.
When machine full load is available, add refrig
erant slowly until the difference between the
leaving chilled water temperature and the cooler
temperature reaches design conditions or becomes
a minimum. Shut the machine down and allow the
refrigerant to drain to the cooler. Mark the level at
the bull’s-eye glasses on the float chamber and
maintain that shutdown refrigerant level.