Fan adjustment check – Carrier UPFLOW 58BTA User Manual
Page 8
Attention! The text in this document has been recognized automatically. To view the original document, you can use the "Original mode".
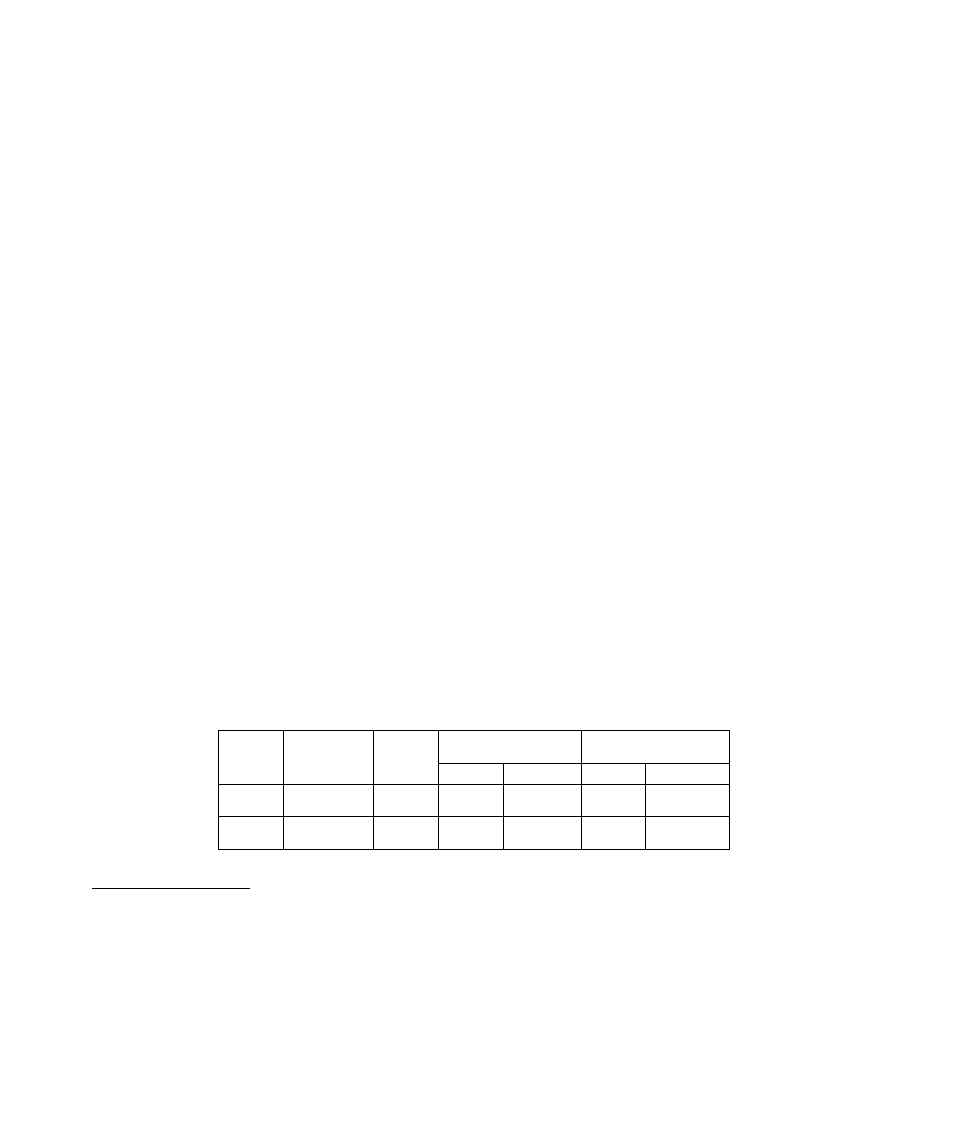
4. The over the fire draft, which is taken through
the hole that is provided in the observation
door, is a measurement that is necessary to
determine if there is a blockage between the oil
burner and the flue outlet.
There should be between a .005"wc to .020"wc
pressure drop through the furnace. This would
set the range of the over the fire draft between
-.01 "wc to -.03"wc. A reading above -.01 "wc,
for example +0.1 "wc, would indicate that the
furnace is in an extremely high pressure
condition in the primary section. This condition
may be caused by excessive combustion air
due to the air band being too wide open or a
lack of flue draft (chimney effect) or some other
blockage, such as soot, in the secondary
section of the heat exchanger.
5. The CO
2
and stack temperature instruments will
enable you to obtain the data that is required to
determine the thermal efficiency of the furnace.
Although this information is nice to have, it is
not essential in the basic set up of the furnace.
6. An oil filter should be installed as close to the
b u r n e r
a s
p o s s i b l e
w i t h
ail
o i l
burners and is essential on the lower firing rate
burners. We recommend the use of a low
pressure drop oil filter such as the General
Filter, Inc . model #1A-25A or equivalent. It is
critical that the oil capacity be equivalent or
greater than the fuel pump gear capacity. For a
two pipe system this is 25gph.
7. The oil pressure regulator is factory set to give
nozzle oil pressures of 100PS1G. The firing
rate noted on the nameplate may be obtained
with "standard" nozzles by adjusting the pump
pressure as noted on the chart below or noted
on the label on the furnace.
NOTE: This appliance is equipped with one of the
oil burners as listed on the chart below and rating
label on the furnace. Use the nozzle listed for that
specific oil burner.
On a new installation the air entrapped in the oil
line leading from the tank to the nozzle must be
thoroughly purged in order to prevent excessive
after drip. The oil pump is provided with a
special fitting that will enable you to purge any
air between the tank and oil pump. The proper
procedure for performing this operation is as
follows:
Place a piece of clear plastic 1/4" dia. tubing
over the purge fitting on the oii pump. Start the
oil burner, then open the purge fitting and allow
the burner to run until the purge tube is
completely free of air bubbles. At this point
tighten the purge fitting which will allow the oil
to run to the nozzle and fire the burner. (If the
purging takes longer than 15 seconds and no
flame has been established the burner will stop.
Push the reset button on top of Primary Control
to restart burner.) For detailed information on
operation of primary control refer to instructions
included with furnace.
8.
After all the set up procedures mentioned
above have been completed, the burner should
be allowed to operate and an inspection mirror
should be used to observe the flame pattern.
Any irregularities such as burning to one side or
pulsating flame patterns should be corrected by
changing the nozzle.
BURNER, NOZZLE AND PUMP PRESSURE CHART
HEATING
CAPACITY
BTU/HR.
FIRING
RATE
GAL/HR/(US)
PUMP
DUCANE
OIL BURNER
R.W.
OIL
BECKETT
BURNER
PSIG
MODEL
NOZZLE
MODEL
NOZZLE
150,000
1 . 3 5
1 0 0
DRC-
2 0 A
1.35 GPH
80* SOLID
AFG
1.35 GPH
70* SOLID
200,000
1 . 7 5
1 0 0
DRC-
2 0 A
1 . 7 5 GPH
80" SOLID
AFG
1 . 7 5 GPH
70’ SOLID
Fan Adjustment Check:
This furnace is equipped with a 3 speed direct drive
motor to deliver a temperature rise within the range
specified on the rating plate, between the return and
supply plenums, at the external duct static pressure
noted on the rating label.
Adjust the fan speed so that the temperature rise is
within the rise specified on the rating plate. Consult the
wiring diagram for speed changes on the direct drive
motor.
To adjust fan OFF time, set the DIP switches on the
control board as shown to obtain the desired timing
(See Figure 2 on next page).
ISSUE 9413
20142901 818