Start-up – Carrier 50DQ User Manual
Page 3
Attention! The text in this document has been recognized automatically. To view the original document, you can use the "Original mode".
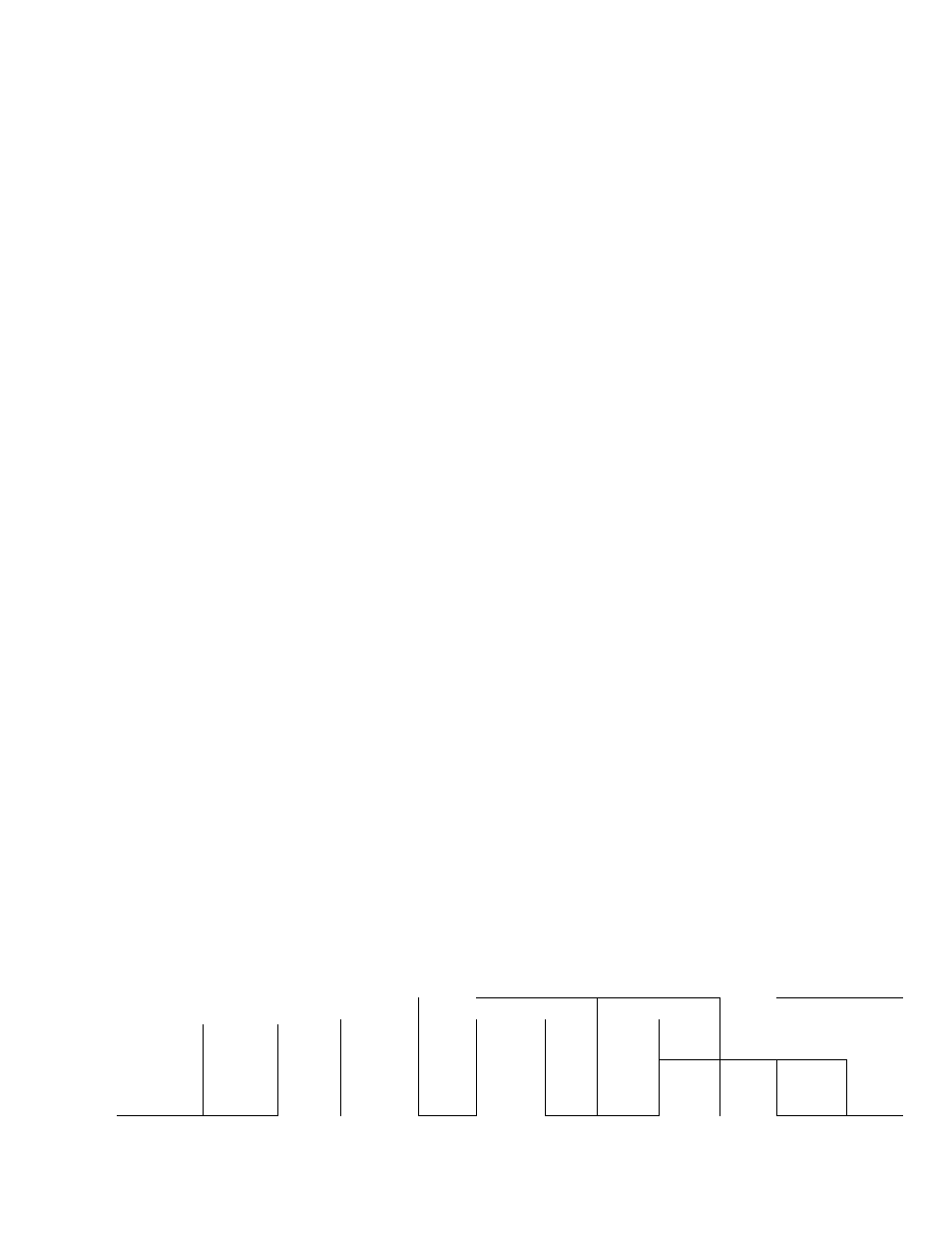
Field-Fabricated
Ductwork
connects
to
unit
flanges with flexible connections. Secure all ducts
to building structure. Seal all joints and roof
openings with sheet metal flashing and mastic.
All external ductwork must be insulated and
weatherproofed. Ducts passing thru unconditioned
spaces must be insulated and covered with vapor
barrier.
Roof Adapter Curb and Duct Adapter Fabrication
— This accessory installation may be properly
accomplished by referring to Fig. 3. If the installa
tion should require more than the 12 in. provided
by the roof adapter curb for clearance under the
outdoor coil, then the roof adapter curb, 1 ft
dimension, must be increased to the desired height.
This curb must be field fabricated.
Condensate Drain
is open to the atmosphere and
must be trapped. Trap must be at least 3 in. deep
and made of flexible material or insulated to
prevent freeze-up.
Fill trap with water to provide an air seal during
unit operation.
Outdoor Coil Condensate
— Do not obstruct area
below coil drain opening. Provide adequate area for
condensate runoff.
Field Power Supply Wiring
— Unit is factory wired
for voltage shown on nameplate. Provide an ade
quate fused disconnect switch within sight of unit
and out of reach of children. Provision for locking
switch open (off) is advisable to prevent power
from being turned on while unit is being serviced,
especially if disconnect is not visible from unit.
Disconnect switch, fuses and field wiring must
comply with National Electrical Code and local
requirements.
Install conduit connectors in unit panel knock
outs (Fig. 2). Route power lines thru connectors to
control box and accessory heaters as shown in
Fig. 8. (Physical installation of heaters shall be
performed in accordance with instructions in the
accessory package.)
Affix crankcase heater sticker to unit dis
connect switch.
Voltage to unit during operation must be
within voltage range indicated on nameplate. On
3-phase units, voltages must be balanced within
2%. Amps must be balanced within 10%. Contact
local power company for correction of improper
voltage or phase unbalance. See Table 2.
Failure, due to operation of unit on improper
line voltage or with excessive phase unbalance,
constitutes abuse and is not covered by Carrier
Warranty.
Field Control Wiring
— Locate a Carrier-approved
accessory thermostat assembly according to the
installation instructions included with accessory.
Locate thermostat assembly in the conditioned
space where it will sense average temperature. Use
one thermostat assembly for each unit on multiple
unit installations.
Route thermostat cable or equivalent single
leads of no. 18AWG colored wire from subbase
terminals, thru connector on side of unit, to low
voltage connections as shown in Fig. 9. Use no. 16
AWG wire for lengths exceeding 50 ft.
START-UP
Unit Preparation
— Make sure that unit has been
installed in accordance with installation instruc
tions and all applicable codes. The following items
must be performed before starting unit.
Internal Wiring
— Check all electrical connections in
unit control boxes, compressor terminal boxes and
other electrical components. Tighten as required.
Crankcase Heater
must be turned on prior to
starting compressor to prevent loss of oil at
start-up. The heater is automatically energized
when compressor is stopped and de-energized when
compressor is operating.
Turn on main power to unit to energize heater
for at least 24 hours before start-up. Area near
heater element should be warm to the touch.
Compressor Oil Sight Glass
should be about 1/2
full of oil.
Compressor Mounting
— Loosen compressor hold
down bolts until sidewise movement of flanged
washers under bolt heads can be easily obtained.
Do not loosen completely. Bolts are self-locking
and retain their adjustment.
t
Table 2 — Electrical Data (3-Ph, 60-Hz)
UNIT
Model
Series
50DQ016
400
500
600
FLA — Full Load Amps
Norn
200
230
460
TACE
UNIT
COMPR
IFM
OFMi
OFM2
Range
Min-Max
WSA
ICF
FU
FLA
LRA
FLA
180-229
100.0
283.8
125
63.6
266
8 8
4 5
4 5
198-254
90.1
257.2
110
57 2
240
8.2
4 5
4 5
414-506
44.4
127.9
50
28.6
120
4 1
1.9
1.9
FU
ICF
— Fuse (max allowable amps; dual element)
— Max Instantaneous Current Flow during start-up (sum of compressor LRA
plus FLA of all other motors in unit)
IFM — I ndoor Fan Motor
LRA — Locked Rotor Amps
OFM — Outdoor Fan Motor
WSA — Wire Sizing Amps (per NEC)
275