Sequenc^of operation, Fig. 1 — control wiring for part-winding start – Carrier 30HS User Manual
Page 2
Attention! The text in this document has been recognized automatically. To view the original document, you can use the "Original mode".
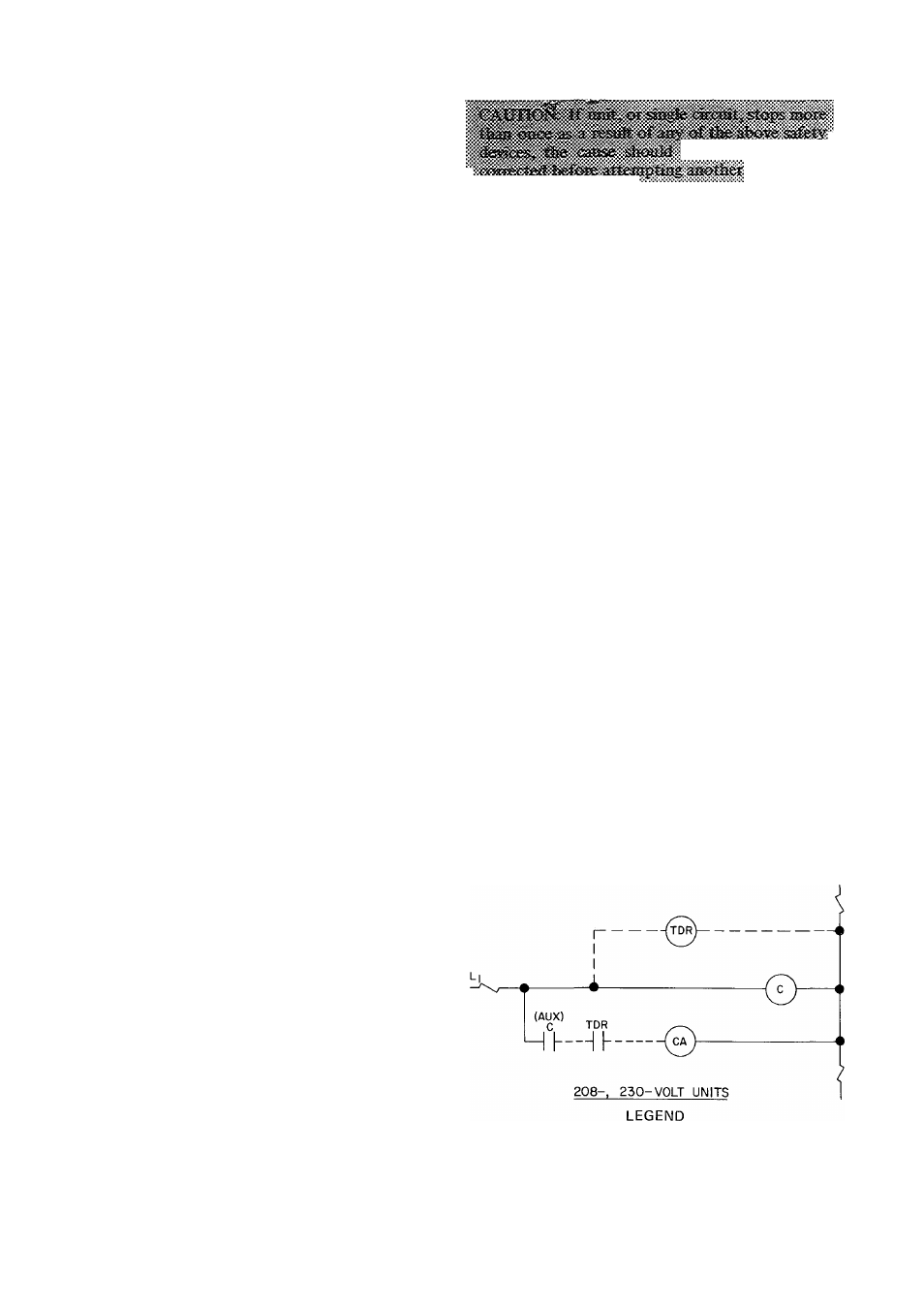
SEQUENC^OF OPERATION
The 115-1-60 control power can be supplied
directly from a separate source thru a code-
approved fused disconnect or thru a field-installed
accessory transformer with the primary side con
nected to the unit power terminal block. A
double-pole circuit breaker protects the control
circuit and serves as the control circuit switch.
Crankcase heaters are wired in the control circuit
ahead of the START switch, so they are always
operative as long as the control circuit breaker is
closed. Heaters are wired so they are on only when
their respective compressors are cycled off.
........... t..
After a prolonged shutdown of 8 hours or
more, the crankcase heaters should be on for 24
hours before starting the unit.
When power is supplied to the control circuit
and the control circuit breaker is closed, the unit is
ready for operation, providing all safety devices are
satisfied, interlocks are closed, and instructions on
warning labels have been followed.
When the START button on the control panel
is pressed, a red indicating light on the control
panel comes on and the step controller and control
relays 1 thru 4 are energized. After a maximum of
1.5 minutes, the recycle relay is energized and the
step controller cycles back (in the load direction)
to the correct cam position to begin the compres
sor starting sequence. The compressors start one at
a time at brief intervals until the load requirement
is satisfied. After completing the starting sequence,
the controller stops and starts, unloads and loads
the compressors to maintain capacity control in
response to water temperature controller demand.
Factory cam settings on the step controller protect
the compressors against rapid recycling.
Complete Unit Stoppage
can be caused by any of
the following conditions: general power failure,
blown fuse in control power feed disconnect, open
control circuit breaker, STOP button depressed,
open contacts in low water temperature cutout,
open contacts in any auxiliary interlock between
terminals 11 and 12 .
Single-Circuit Stoppage
can be caused by open
contacts in any motor thermal protector, open
contacts in low-pressure switch, open contacts in
high-pressure switch, open contacts in oil safety
switch (when used), blown compressor circuit fuse.
Stoppage of one circuit by safety device action
does not affect the other circuit. Besides stopping
compressors, all the devices listed except the
low-pressure switch will close the liquid line
solenoid valve for that circuit.
recast.
Restart Procedure
(after cause tor stoppage is
corrected).
GENERAL POWER FAILURE - Press START
button on control panel.
BLOWN FUSE IN POWER FEED DISCONNECT
— Replace fuse and press START button on
control panel.
LOW WATER TEMPERATURE CUTOUT - Press
reset button on control (inside control box).
Restart is automatic.
AUXILIARY INTERLOCK — Automatic restart
after condition is corrected.
OPEN CONTROL CIRCUIT BREAKER ^ Close
breaker and press START button on control panel.
HIGH-PRESSURE SWITCH - Press START
button on control panel.
LOW-PRESSURE SWITCH — Compressors will
restart automatically when pressure comes up
sufficiently.
COMPRESSOR MOTOR THERMAL PROTEC
TOR — After motor has cooled down, press
START button on control panel.
OIL SAFETY SWITCH — Press reset button on the
switch, and press START button on control panel.
MODIFICATION FOR PART-WINDING START
(See Fig. 1,5 and 6.)
For 208-, 230-Volt Units
— In the control circuit
for each compressor, add a 1.5 second time-delay
relay to actuate the second contactor coil (CA).
Time-delay
relay.
Carrier
part
number
HN67FK001, is available from Carrier Service Parts
Center, Syracuse, N.Y. Contact your local Carrier
representative.
^
AUX. — Auxiliary Contacts
C — Compressor Contactor
CA — Second Compressor Contactor
TOR — Time-Delay Relay
o
Holding Coil
Factory Wiring
f
--------- Field Wiring
Fig. 1 — Control Wiring for Part-Winding Start