Canon PSC 2000 User Manual
Page 56
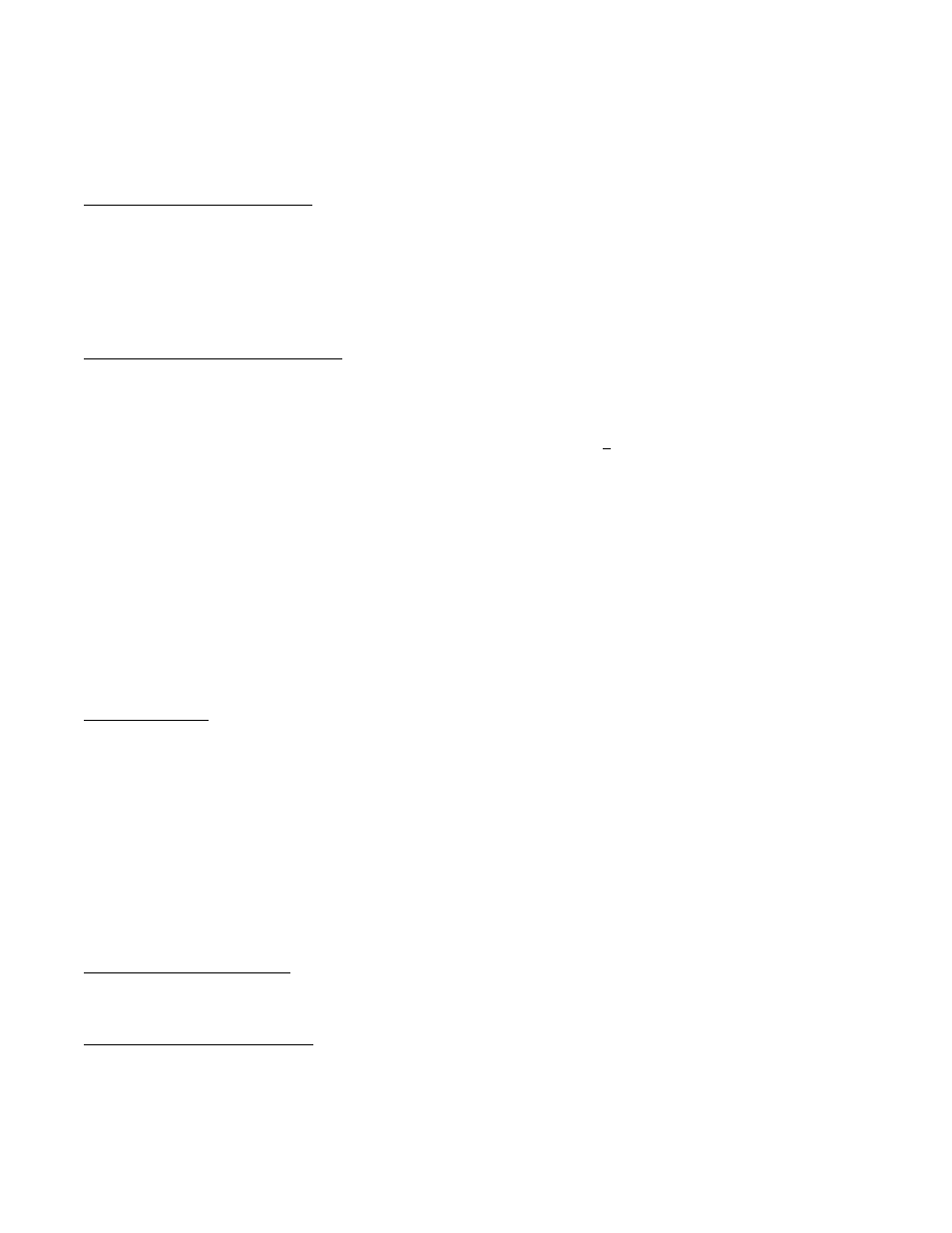
2000 Fire Door-Fan Manual
updated 2002-05-28
Page 56 of 58
for leaks in the gauges by blowing in the tube, then folding the tube over on itself - the gauge should hold
pressure without the needle dropping perceptibly.
Occasionally, a needle will get stuck to the face plate. Replacing the gauge is the only practical option.
Gauge Needle Falls When Tested
Each time the Infiltrometer is used, the gauges should be pressured up, the tube capped off to test for leaks.
A sudden loss of pressure will indicate something has changed. Check, first to see if the translucent
polyethylene quick connect is cracked or split. This is possible, so if unsure replace it. Heat the tube end if
necessary. Next check all the exposed tube for cracks or cuts. Next, if on ROOM/ HOUSE PRESSURE 60 gauge,
flip the switch and check in the other direction. This will show a leak on the other side of the gauge and will
therefore require its removal. If all this fails, contact Retrotec.
Gauge Recalibration and Replacement
The Standard requires that the 0-60 Pa Room Pressure gauge be recalibrated on a yearly basis:
“The room pressure gauge should be capable of measuring pressure differences
from 0 Pa to at least 50 Pa. It should have an accuracy of + 1 Pa and divisions of
2 Pa or less. Inclined oil-filled manometers are not considered to be traceable to
a primary standard and need not be recalibrated. All other pressure
measurement apparatus (e.g., electronic transducer or Magnehelic) should be
calibrated at least yearly."
NFPA does not specifically state that the 0-250 Pa Flow Pressure gauge(s) be recalibrated yearly, however you may
wish to have the Flow Pressure gauge(s) recalibrated as well. If you don't have any problem getting good field
calibration check results, you probably don't need to recheck your flow pressure gauges.
Retrotec offers a service to either calibrate your gauge in its control box, or to send you an exchange.
The complete system must be returned every five years for a complete calibration. For offshore customers this
test may be waived by performing a field calibration check for the AHJ-but that will be up to him.
Blower Blade Rubs
Check to see if blade hits the screen or the edge of the white plastic tube. If it is hitting the screen, check to see
if a screen bracket is off or twisted and adjust as necessary. If the screen is flat and appears to be properly
located, the blade may have moved on the motor shaft. Unplug the blower, remove the rear screen, loosen the
set screw holding the hub to the shaft, tap the hub back slightly towards the motor (ensuring it doesn't actually
touch the motor), ensure the set screw is on the flat edge of the shaft, and re-tighten it. Re-attach the rear
screen with cable ties.
If the blade is rubbing on the inside of the white plastic tube, check to see if the wire motor mounts are straight. If
they have been bent, they can often be straightened out by hand. Otherwise, adjust the position of the motor by
loosening two (2) motor mount bolts (180
o
opposed) and adding or removing white plastic washers. Keep the total
number of washers used the same. If the white plastic is broken due to damage in shipping, contact us for advice.
Repairing Panel Cracks or Chip
Use ABS or crazy glue to repair. Paint with auto touch-up enamel.
Flex duct Maintenance and Repair
The flex duct will eventually wear out and need to be replaced. The duct itself can be ordered from Retrotec, you
can then attach it to the old 2 x 2 panel. Small splits and tears should be taped over to ensure air from the room
doesn't get pulled into it during the test, resulting in an inaccurate reading.