LAARS MAX 165 (DV) - Installation, Operation and Maintenance Instructions User Manual
Page 10
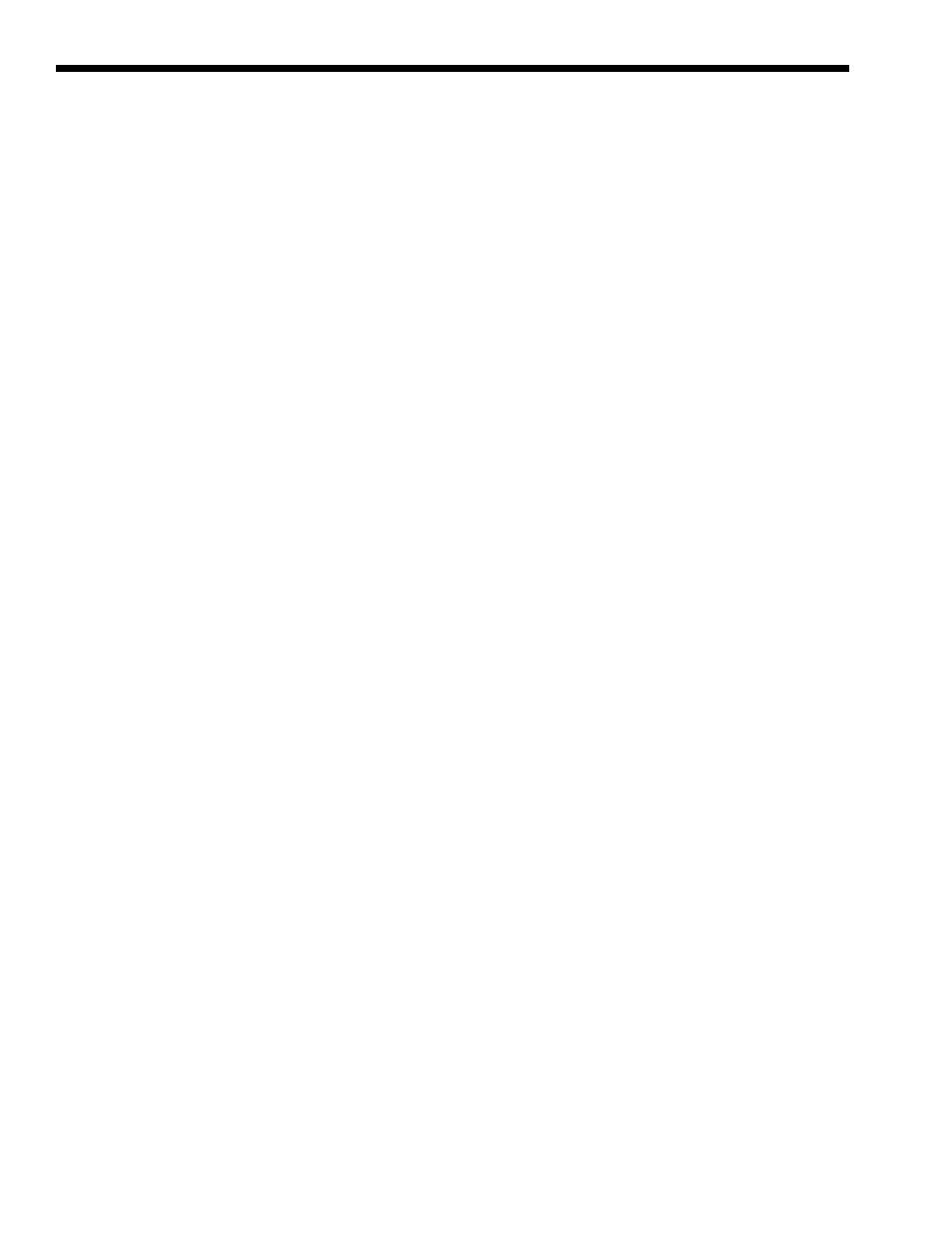
Page 10
LAARS Heating Systems
particular conditions
3M. Indirect Hot Water Tank
Install the tank in accordance with the
manufacturers instructions using recommended pipe
sizes, location of temperature / pressure relief valve
and any other special requirement for correct
installation.
A thermal expansion tank may be required on
hot water tanks equipped with check valves or back
flow preventors on the cold water supply.
3N. Burner Controls
The burner is fitted with a fully automatic
control system which incorporates a cad cell to
monitor the flame and shut down the burner in the
event of flame failure. A push button is provided to
restart the burner, but this must never be pressed more
than once following a flame failure.
Pre-purge (direct vent only) provides an air
supply prior to oil flow to ensure clean combustion
under all conditions.
Post purge is also fitted to direct vent burners to
completely clear all residual gases from the boiler and flue
system. This is necessary with direct vent flues because of
the lack of draft prevailing after the burner shuts down. The
post purge time is factory set at 30 seconds.
3O. Fuel System (oil supply no heavier
than #2 fuel oil)
The oil supply should be run in heavy walled
copper tubing, without any joints, using flared fittings
only. It is important that the oil feed line to the burner
is air tight otherwise firing problems could result.
3P. Gravity Head System
Where the fuel supply is level with or above the
burner only a single pipe is required.
3Q. Suction Lift System
Where the burner is above the fuel supply a
return line must be provided in addition to the supply
line. The arrangement requires the fitting of the
bypass plug (provided) in the return port of the fuel
unit. Air is automatically purged from the fuel unit
and returned to the storage tank with this arrangement.
NOTE: If the suction lift exceeds 10 feet (3m),
a two stage fuel unit should be used. For Riello
burners obtain C700 kit for respective burners.
3R. Oil Filter
An in-line oil filter should be fitted in the supply
line and located inside the building between the tank
shut-off valve and as near to the burner as possible. A
shut-off valve should also be located close to the
burner for ease of servicing.
3S. Wiring
Wiring connections between burner and aquastat
on supply manifold should be made in accordance with
wiring diagrams in this manual (
see Figures 5 through
11
). External wiring must be in accordance with local
codes and regulations.
For convenience of servicing, a fuse disconnect
switch should be fitted near the boiler. Field
connections should be protected with a 15 amp fuse.
If an indirect hot water tank is used, the aquastat
on tank should be wired so as to have preference over
heating of the building. This requires the use of a
Honeywell L6006A-1145 or equivalent aquastat on
the tank working in conjunction with a zone valve or
circulator relay. See wiring diagrams in this manual.
On boilers piped direct (no zones) set anticipator
on thermostat to 0.8 amps.