LAARS Mighty Therm HH-PH (Sizes 175-400) - Installation, Operation and Maintenance Instructions User Manual
Page 15
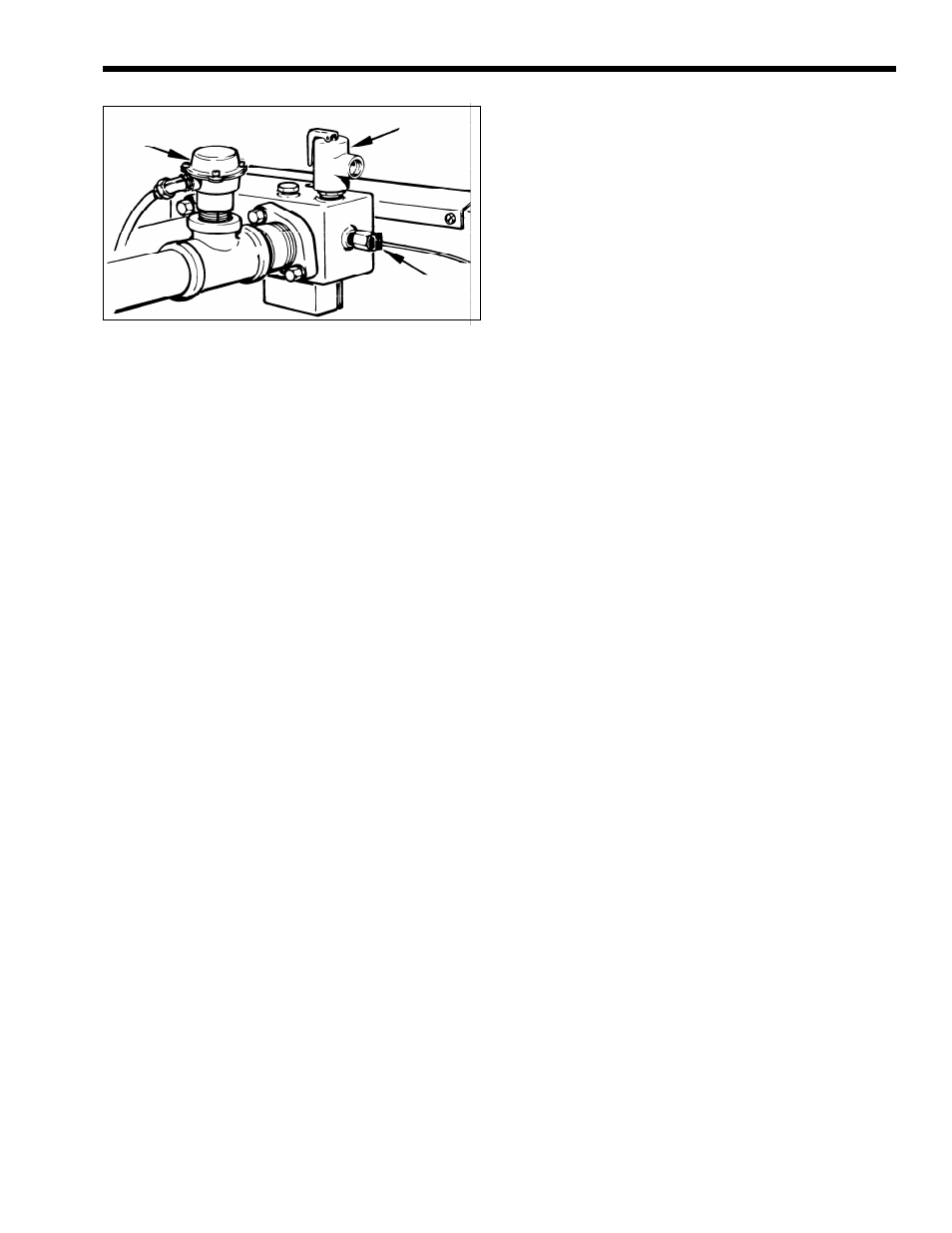
Mighty Therm HH-PH Hydronic Boilers
Page 15
2F-6. Chilled Water Systems
If the boiler is part of a refrigeration system,
include the right valves to isolate the boiler from the
refrigeration system during times when the boiler is
not operating.
When the boiler piping is connected to heating
coils, which are close to refrigerated air circulation,
install flow control valves or other automatic methods
to prevent gravity circulation of the boiler water
during the cooling cycle.
2F-7. System to Boiler Piping
1.
Install gate valves at the inlet and outlet to the
boiler so it can be isolated for service.
2.
Make sure the pressure relief valve (see Figure
26) has its outlet piped to a drain or floor sink.
Pay special attention to relief valve settings in
installations where the boiler is located on the
ground floor of a tall building, or where the
operating temperature of the boiler is above
210°F (99°C). In both cases, the static pressure
of the system is raised. This would bring raw
water into the system. The factory will furnish a
75 psi (516.8 kPa) setting unless a special setting
is ordered.
3.
Install a low water cutoff device if the boiler is
installed above radiation level.
4.
Install manual and/or automatic air venting
devices at high points in the system to get rid
of air.
5.
Install a correctly sized expansion or
compression tank in accordance with the
manufacturer's instructions.
6.
Support the weight of all water and gas piping
with suitable hangers or floor stands.
7.
Check piping diagrams with local applicable
plumbing, heating and building safety codes.
2F-8. Filling the System
1.
Close all air vents and open the makeup water
valve. Let the system fill slowly.
2.
If a makeup water pump is used, adjust the
pressure switch on the pumping system to
maintain at least 12 psi (82.7 kPa) at the highest
point in the heating loop.
3.
If a water pressure regulator is installed on the
makeup water line, adjust the pressure regulator
to provide at least 12 psi (82.7 kPa) at the
highest point in the heating loop.
4.
Open air vents on all radiation units at the high
points in the piping throughout the system,
unless automatic air vents are installed at those
points.
5.
Run the system circulating pump for at least 30
minutes with the boiler shut off.
6.
Recheck all air vents as described in Step 4 above.
7.
With the system full of water and under normal
operating pressure, the air pressure in the expansion
tank should be at least 12 psi (82.7 kPa).
8.
Start up the boiler following the instructions
found on the inside of the boiler.
9.
Operate the whole system, including the pump,
boiler, and radiation units for 1 hour.
10. Shut down the entire system and vent all
radiation units and high points in the system
piping as described in Step 4 above.
11. Close the makeup water valve and check the
strainer in the pressure reducing valve for sedi-
ment or debris. Reopen the makeup water valve.
12. Check the gauge to make sure the water pressure
is right, and check water level in the system. If
the water level indicated above the boiler shows
that water is at the highest point in the circulating
loop, then the system is ready for operation.
13. Within 3 days of start-up, recheck all air vents
and expansion tank as described in Steps 4 and 8
above.
2F-9. Minimum Boiler Temperature
The boiler inlet water temperature must be
minimum 110°F (43°C) when the system has come up
to normal operating conditions. Lower temperature
inlet water may allow the production of condensation
on the outside of the copper finned tubes, which can
block the flue gases and/or cause improper
combustion, leading to heat exchanger sooting.
For systems with lower than 110°F (43°C)
temperature, boiler must be protected from low
temperature return water. There are many methods of
achieving low temperature protection. Figures 22 and
25 shows an example of such a system.
FLOW
SWITCH
PRESSURE
RELIEF
VALVE
HIGH-LIMIT
DRY WELL
Figure 26. Pressure Relief Valve.