Tsn (cam-over wrench) operating instructions – Checkline TSN User Manual
Page 3
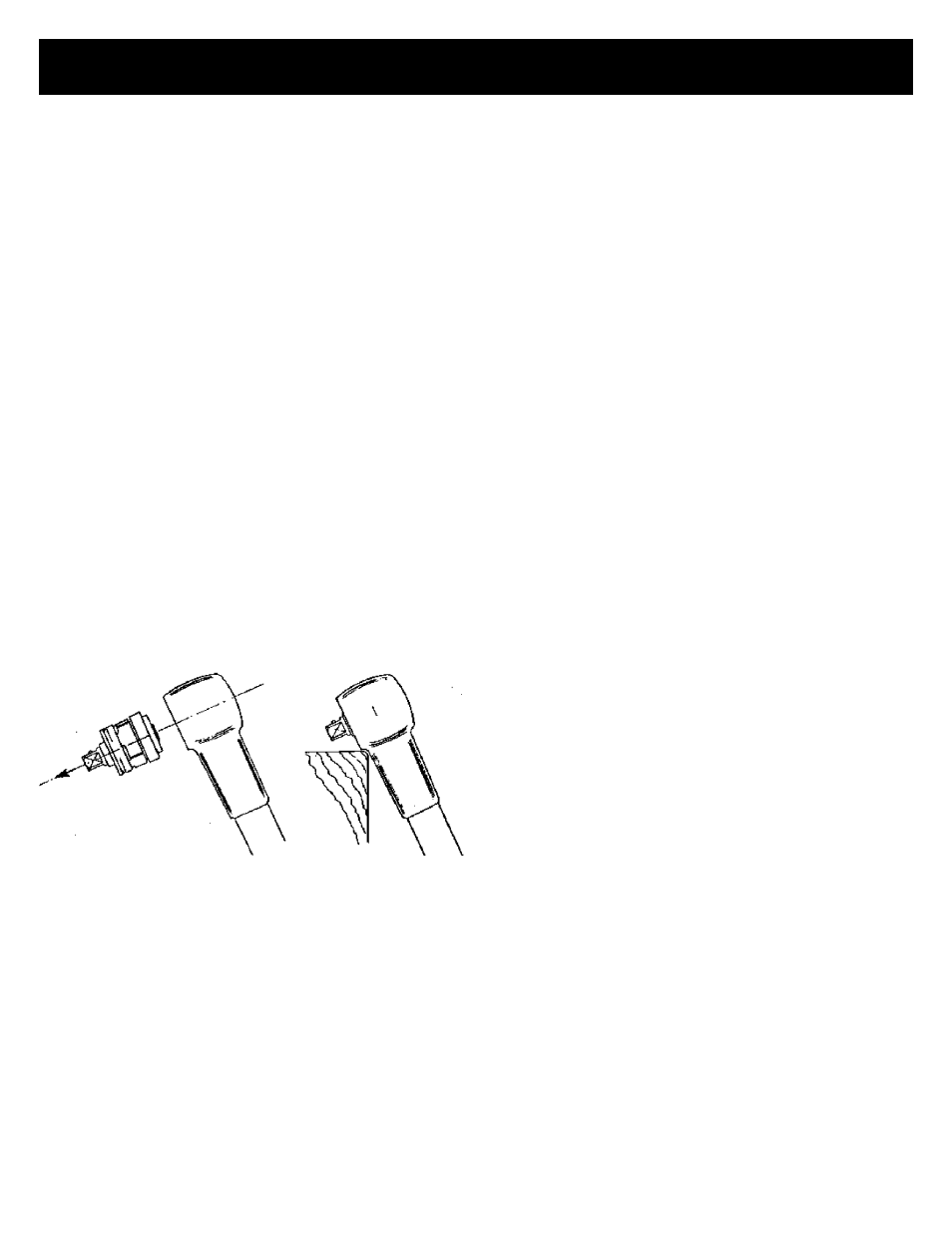
TSN (Cam-Over Wrench) Operating Instructions
Rev 2.0 (March 20, 2008)
Procedure (continued)
4. Ensure the roller is below the surface of the main bearing housing and remove the rear main bearing using special
removal tool.
Note: It may not be necessary to replace the main bearings in every TSN unless there are signs of extreme wear, or the
cam will not rotate smoothly within the bearings.
5. With the cam/spindle assembly removed, check the condition of the roller guide and roller. It may be necessary to remove
the rear main bearing to carry out this check.
6. Degrease, clean and inspect all parts, replacing those which are worn or broken.
7. Replace rear main bearing in the head using special insertion mandrel ensuring that the roller is fully retracted so as not
to interfere with the bearing as it is inserted. Ensure that the rear main bearing sits squarely on the rear face of the housing.
8. Re-lubricate the rear main bearing with anti-scuffing paste.
9. Re-assemble spindle and pawls into the cam ensuring that the pawl springs are correctly positioned. Also ensure that the
pawls are located with their half rounded long edge resting in the spindle journals and that the pawls and spindle “ratchet”
when turned within the cam. The pawls and spindle should be lubricated with light machine oil.
10. Lubricate the cam faces and main bearing journals with anti-scuffing paste and insert the cam spindle assembly into the
head ensuring that the nylon thrust bearing is located on the spindle end and within the rear main bearing.
11. Insert the front main bearing into the head with the large chamfer outwards.
12. For TSN 55 and 125 Wrenches. Locate one or two ‘0’ rings on the front bearing chamfer and replace the cover plate and
Spirolox Ring.
For TSN 25 Wrenches Only. Replace the lip seal with the lip uppermost ensuring the seal is located squarely in the bore.
Tap fully home onto abutment washer using suitable tubular drift and replace the Spirolox Ring.
13. Progressively tighten the torque setting adjustment screw, operating the tool several times as torque increases.
The wrench is now ready for use. It is advisable to operate the wrench approximately 100 times at the upper end of its
designed capacity to ensure that new parts “settle in” properly before final calibration is carried out.
Testing & Servicing
In order to maintain accuracy, it is crucial that torque control measuring
equipment be calibrated regularly.
We recommend a general once a year calibration interval. However, it is
the user’s organization that must determine suitable intervals based upon
equipment performance, application, degree of usage and management
objectives.
For calibration, re-adjustment or repairs, please send the tool to one of
our 3 service locations.