Gas trains – Beckett CG10 User Manual
Page 10
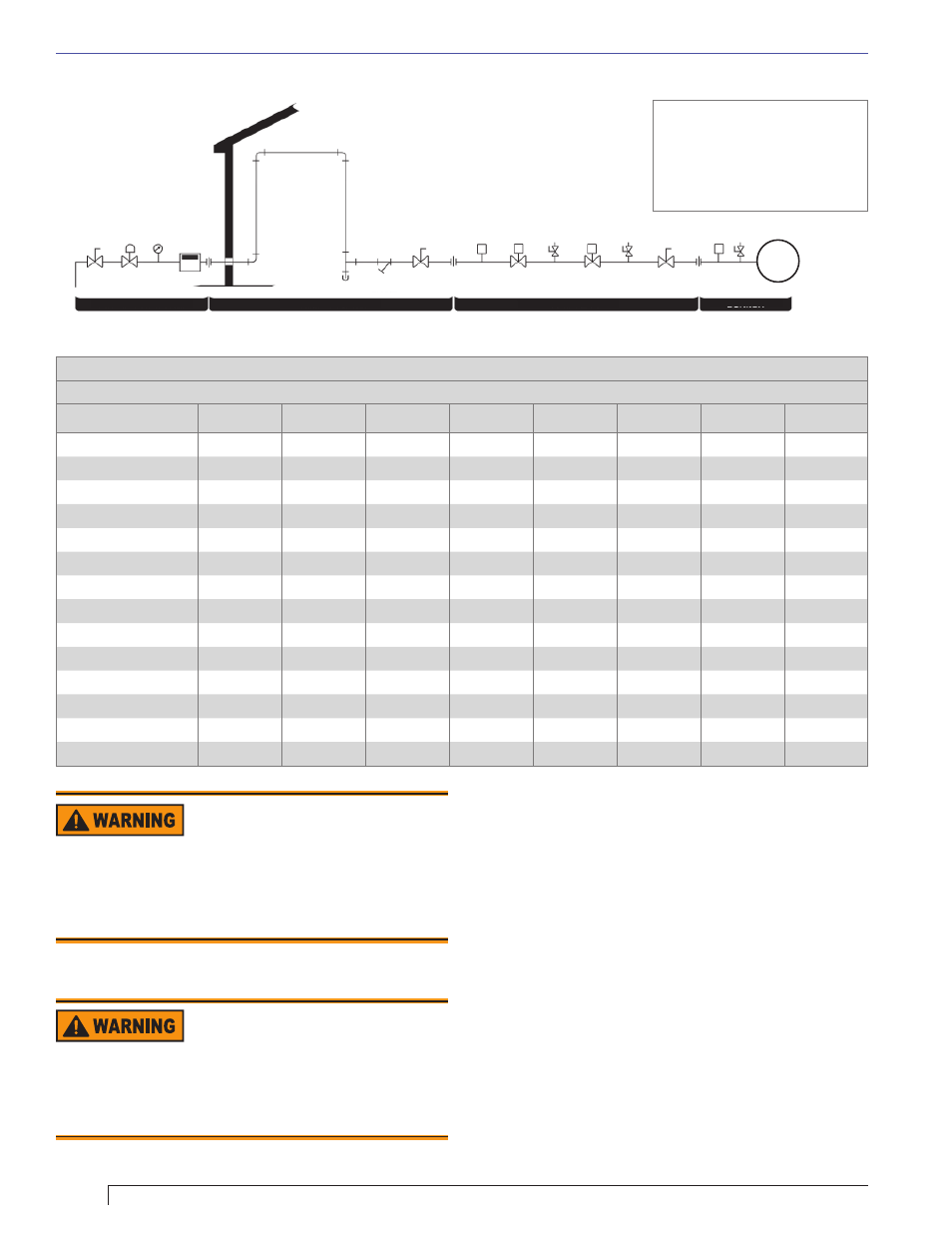
10
Figure 7. Typical Gas Piping Layout
Schedule 40 metallic pipe with 0.50 psi or less inlet pressure and 0.30” W.C. pressure drop
Maximum capacity in cubic feet of gas per hour (CFH). Natural gas with 0.60 specifi c gravity. Pipe size (inches) IPS
Pipe Length (ft.)
0.75”
1.0”
1.25”
1.5”
2.0”
2.5”
3.0”
4.0”
10
278
520
1050
1600
3050
4800
8500
17500
20
190
350
730
1100
2100
3300
5900
12000
30
152
285
590
800
1650
2700
4700
9700
40
130
245
500
760
1450
2300
4100
8300
50
115
215
440
670
1270
2000
3600
7400
60
105
195
400
610
1150
1850
3250
6800
70
96
180
370
560
1050
1700
3000
6200
80
90
170
350
530
990
1600
2800
5800
90
84
160
320
490
930
1500
2600
5400
100
79
150
305
460
870
1400
2500
5100
125
72
130
275
410
780
1250
2200
4500
150
64
120
250
380
710
1130
2000
4100
175
59
110
225
350
650
1050
1850
3800
200
55
100
210
320
610
980
1700
3500
Table 1. Gas supply piping capacity
Gas Trains
Standard – An Underwriters Laboratories (UL) listed
gas train is standard for the CG10 gas burner. This
confi guration also meets CSD-1 requirements. See
Figure 8 for typical component layout.
Propane (LP) – When the correct propane restrictor
is added to a burner’s gas pipe assembly it changes
the burner’s gas pressure drop so that the propane
pressure drop is equal to the natural gas pressure drop
of the same BTU fi ring rate. That is why the Manifold
to Furnace Pressure Drop curves of Figures 12 and
13 are correct for both propane and natural gas. That
is also why a gas train adjusted for the burner’s natural
gas requirements will be correctly adjusted for its
propane requirements. R. W. Beckett provides the same
pressure regulating safety shutoff valve in the gas train
(usually a Honeywell V4944B) for both natural gas and
propane. The valve is marked for natural gas due to
its primary usage in a pressure range normally used
LGPS
HGPS
S
(IF USED)
DRIP LEG
BURNER
METER
MSC
SSOV1
2PRV
MLTC
U
TC
U
TC
TC
U
PG
REGULATOR
ABBREV.
HGPS
LGPS
MSC
MLTC
PG
S
SSOV1
TC
U
2PRV
ITEM DESCRIPTION
HIGH GAS PRESSURE SWITCH
LOW GAS PRESSURE SWITCH
MAIN SHUTOFF COCK
MAIN LEAK TEST COCK
PRESSURE GAUGE
STRAINER
SAFETY SHUTOFF VALVE #1
TEST COCK
UNION
TWO POSITION REGULATING VALVE
GAS UTILITY PIPING
FACILITY PIPING
GAS TRAIN
BURNER
Section: Connect Gas Piping
Install a Drip Leg in Gas
Supply Piping
Foreign matter could lodge in gas valve cutoff seals,
resulting in gas leak-through, explosion or fi re.
Install a full-size drip leg or dirt pocket in the piping directly
ahead of the main shutoff valve to capture foreign matter.
Gas Leaks and Exposion
Hazards
Provide Over-pressure Protection
CSD-1 requires that if gas pressure entering the
building exceeds the rating of any gas train component
an overpressure protection device must be installed.