Nexen PRD1100 966902 User Manual
Page 12
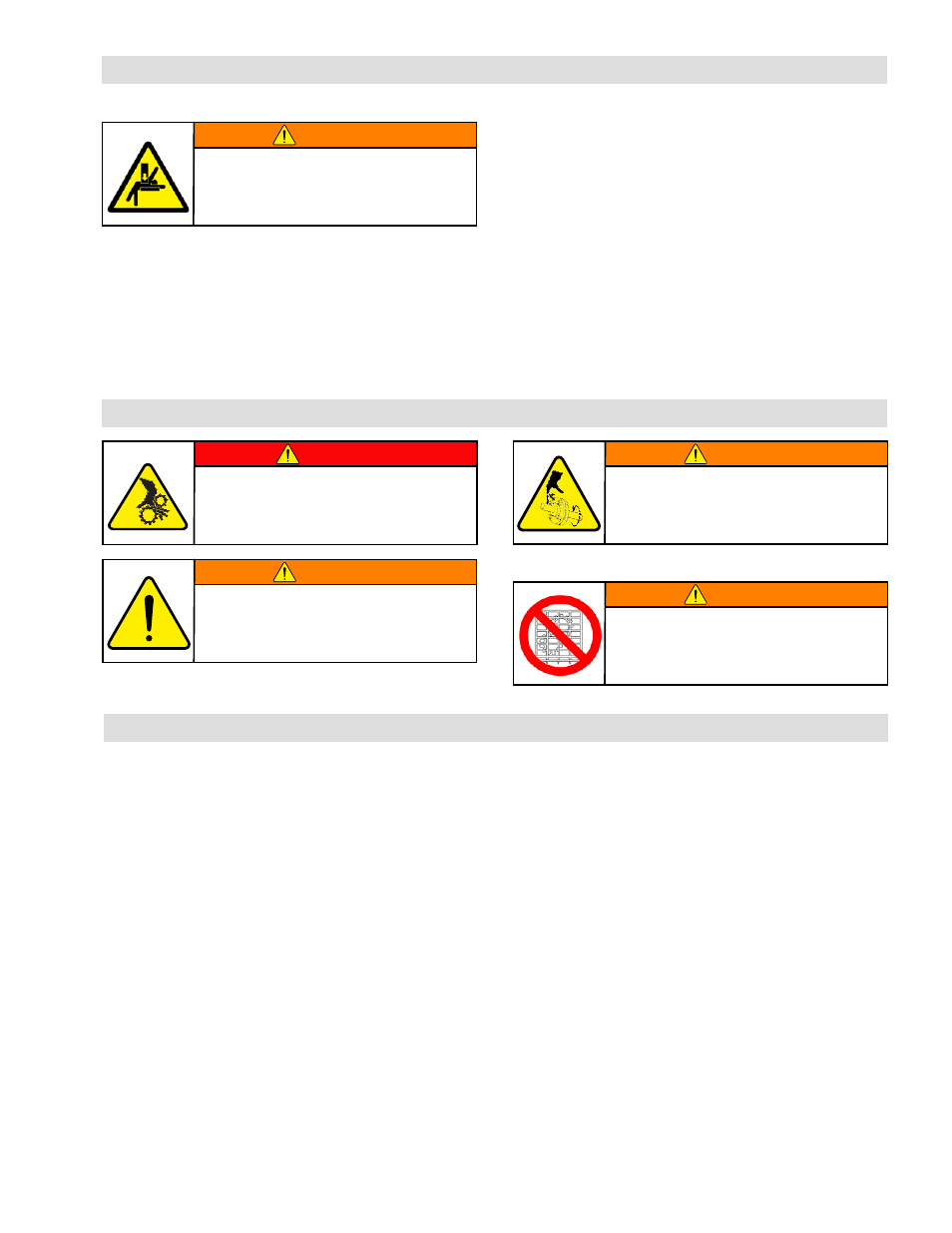
12
FORM NO. L-21274-A-0113
DISENGAGING THE ROLLER PINION
1. De-couple the load from the RPG system.
2. Disconnect the power source, ensuring that no torque
is applied to the roller pinion.
3. Remove pinion preload by loosening the preload
mechanism sliding bolts slightly and then turning the
preload application screw(s) to remove the pinion
preload. You should be able to slightly separate the
pinion from the gear teeth now.
WARNING
Failure to properly support the load before
disengaging the RPG system could cause
serious harm to operators or equipment.
4. Progressively loosen non-adjacent bushing fasteners
in the same order they were tightened until all are
removed from the bushing (Refer to Figure 4).
5. Insert the bushing fasteners into the threaded holes
in the bushing flange and alternately tighten them as
illustrated in Figure 4 to release the locking action of
the bushing.
6 Lift the servo/reducer/preload mechanism assembly
from the gear or slide the servomotor/reducer out of
the pinion bore.
NOTE: Inspect all bushing fasteners and replace any that
show excessive wear. Contact Nexen for replacements.
OPERATION
DANGER
This product has moving parts that
can crush or cut appendages. Provide
adequate spacing or guarding from any
operating product.
WARNING
Never exceed maximum operating
speeds listed for your product.
WARNING
Ensure proper guarding of the product is used.
Nexen recommends the machine builder
design guarding in compliance with OSHA 29
CFR 1910 “Occupational Safety and Health
Hazards”.
WARNING
Use appropriate guarding for rotating
components. Failure to guard could
result in serious bodily injury.
•
Max speed of RPS25 Pinion = 1960 rpm.
LUBRICATION
The pinion needle bearings are sealed and lubricated for
life and cannot be serviced.
Nexen recommends lubricating the gear teeth every 2
million pinion revolutions or 6 months, but it may need to
be lubricated more frequently based on the application
conditions, and observable tooth or roller wear.
When lubricating the RPG system inspect the pinion
rollers and gear teeth for any abnormal wear patterns and
ensure the pinion rollers are not seized or have excessive
play. Wear on the edges of the gear teeth (not uniform
across the tooth face) or rings on the rollers indicate an
alignment problem which should be corrected to obtain
maximum system performance and life.
The rollers in new pinions, especially larger sizes, can
seem difficult to turn due to seal drag. This improves as
the pinion breaks in.
THK AFA grease is recommended for gear tooth
lubrication. Nexen offers this grease under product
number 853901. Greases for special applications such
as food grade, vacuum, or others are allowed if they use
a synthetic base, a polyurea thickener, and meet the
following Kinematic Viscosity Levels: CST@40C = 25;
CST@100C = 5. Contact Nexen for recommendations
on alternative greases.
The RPG system can be lubricated in two ways:
1. Apply grease to the pinion rollers and roll the pinion
back and forth 5 times over one meter circumference
of gear teeth, repeating the process until the entire
gear is lubricated.
2. Using a swab apply a very small dab of grease on the
middle of each tooth face and rotate the ring gear 5
times.
Wipe excess grease from the sides of the gear and pinion
body to prevent grease being thrown off during operation
and for general cleanliness.