Tjernlund COP2 Constant Operating Pressure Exhaust Control 8504208 User Manual
Page 9
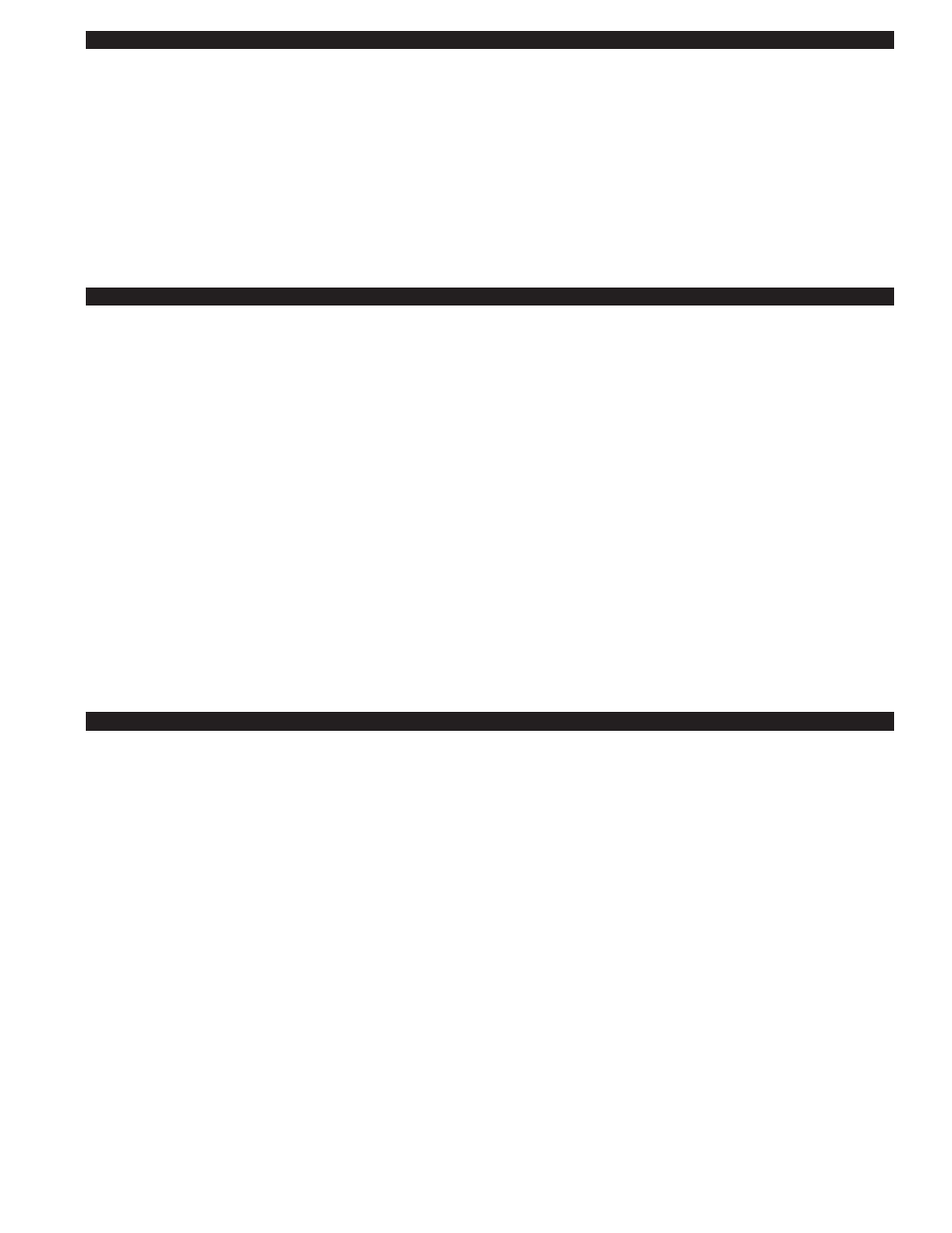
8
ADJUSTMENT OF BALANCING BAFFLE(S) FOR KITCHEN AND BATH FANS
IMPORTANT: Balancing Baffles must not be used for dryer applications due to the potential for lint buildup.
1. With all balancing baffles closed and starting with connection at lowest floor drill a small sampling hole in duct connection to
the chase 1 foot behind the Balancing Baffle (opposite side of chase connection).
2. With the COP2, RT-Series Fan and Bath/kitchen fans connected to the duct operating, gradually open the Balancing Baffle
until desired negative exhaust pressure is measured and lock in place. Typically a measurement of a -0.02 to -0.05" W.C. is
Adequate.
3. Repeat steps 1 and 2 for each floor, moving up towards the RT-Series Fan.
4. After all are set, review all measurements on each and readjust as needed.
OPERATION OVERVIEW
With 115 VAC supplied to L1 and N and the VFD power switch in the off position the following circuits are powered. The discon-
nect that powers L1 and N must be switched off to remove power from these circuits:
24 Volt Transformer
Pressure Transducer
BLK and WHT terminals to the thermostat of the Exhauster motor cooling fan
Thermostat for the VFD heat sync cooling fan
When the VFD switch is turned on, the VFD is powered but still must have Activation terminals C1 & C2 closed for the RT-Series
fan to operate.
With the activation circuit closed the COP2 controller will reference the sampling tube pressure via a 1-10 VDC signal with 2.8
VDC = 0.00” W.C. As pressure is reduced by additional exhaust volume, winds or interior negative pressures the transducer will
output a lower voltage to the VFD, increase the frequency from the VFD, causing the Exhaust Fan to speed up until the set point
pressure is reached. Further fluctuations in measured pressure will cause the VFD to modulate the frequency to the Exhaust Fan
so that the set point exhaust pressure is maintained.
If the fan cannot maintain the setpoint pressure within ±0.02” W.C. at anytime for more than a 50 second period, the Green LED
on the middle left side of the VFD will turn Red and cause the system to fault. Reset the VFD by turning the on/off switch “Off” for
one minute to reset the fault and cycle the fan to determine if a problem exists. If the set point is low enough to allow natural venti-
lation to exceed the set point jumper “B” to “GND” on the green logic terminal strip to disable over draft protection. The control will
now only fault for an under draft condition.
TROUBLESHOOTING ELECTRICAL PROBLEMS
It is necessary to measure voltage during troubleshooting. Extreme caution must be exercised to prevent injury. If you are unable
to determine the defective part with the use of this guide, call your Tjernlund distributor or Tjernlund Products direct at
1-800-255-4208 for further assistance.
EXHAUST FAN MOTOR DOES NOT OPERATE
Check that the COP2 control has power by verifying that the top LED is Green.
If this LED is Red, turn the VFD power switch off for a minimum of 1 minute to reset the fault. A Red status indicates an over-cur-
rent or circuit board over-temperature issue. In some cases an acceleration rate that is too fast can cause an over-current fault. In
most cases the RT-series fan should be checked to verify that the shaft rotates freely with power disrupted. Since the RT-Series
fan may not operate if the exhaust set point is reached by natural means perform the following test:
Top LED is Green
Verify that the supply power to the COP2 is switched on and the Activation terminals C1 & C2 are closed with a switch or jumper to
start the RT-Series fan. Disconnect the sensing tube from the barbed fitting on the Transducer electrical box. The fan should ramp
to full speed. Reconnect the tube. The fan should slow down to the original speed. This change in fan performance can be demon-
strated by viewing a draft gauge that is teed into the tubing from the pressure transducer as shown in Diagram E.
If removing the sensing tube does not cause the fan to speed up measure AC voltage at terminals V+ and COM of the Transducer
and look for a reading between 22 - 30 VAC. If voltage in this range is measured remove tube from the barbed connection on the
Transducer and look for between 2.7 - 2.9 VDC when measuring terminals 1-10 and COM.