Losi LOSB0021 User Manual
Page 15
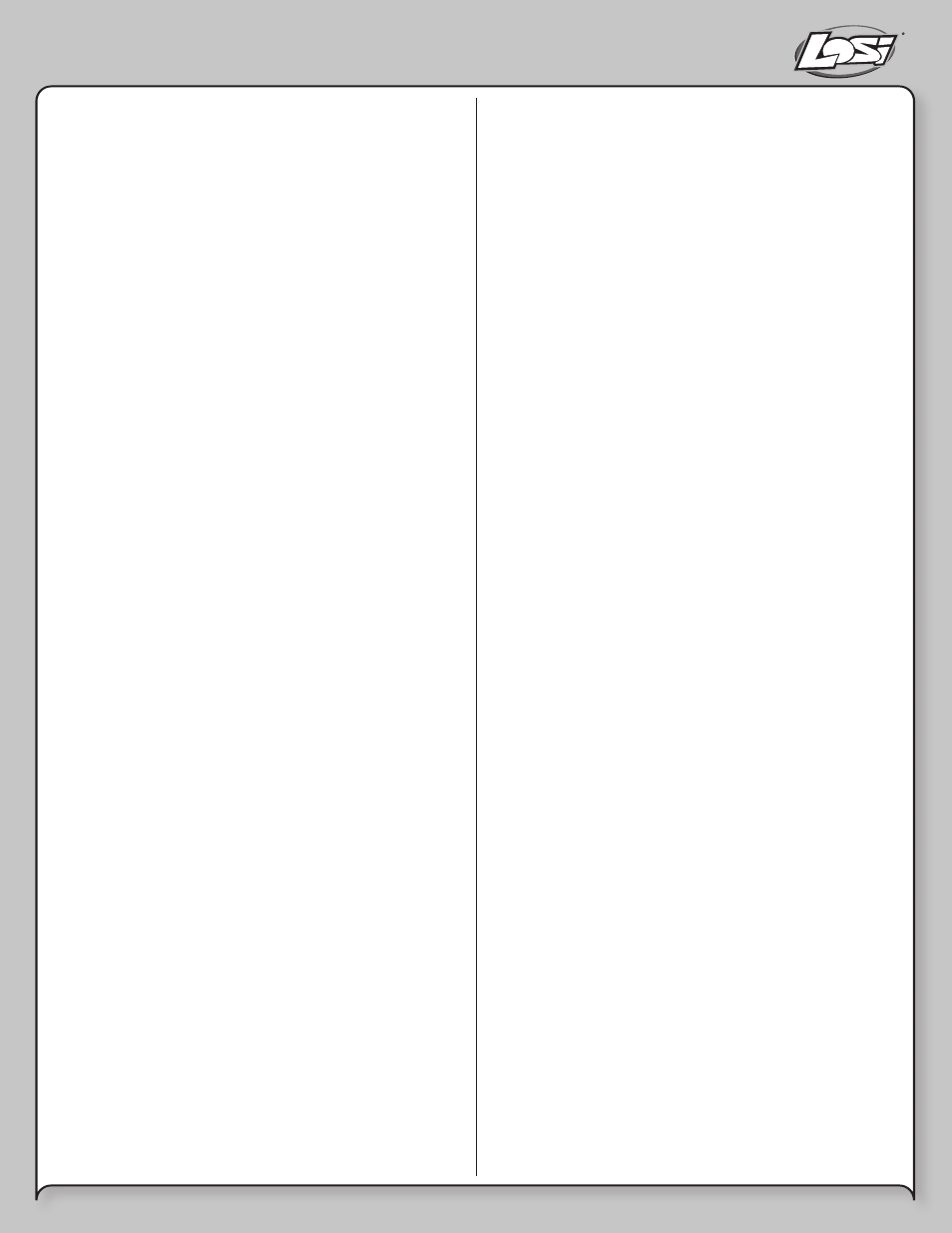
15
Engine is hard to turn over:
1. The engine may be flooded. Remove the glow plug,
turn the model upside down over a rag and turn the
engine over using the pull start. Raw fuel should spray
out of the glow plug hole. Replace the glow plug
making sure you replace the small copper gasket that
goes on it.
2. If the engine will not turn over it is probably still new
and stuck at top dead center. Use a screwdriver to
rotate the flywheel on the engine counterclockwise
until it moves freely, turn the model off then on again
and retry. It may take several such tries to get it to start.
After the engine has been run 30 to 45 minutes, you
will find this will not occur.
Engine tries to start but will not run:
1. Engine may be loaded up with excess fuel inside. Pull
the trigger 1/4-inch and count to 5 before trying to
start. If starting improves repeat until the engine runs
and idles.
2. Engine may be overheated. Let cool, open high-speed
needle 2 hours and retry.
3. If the fuel has been left open or is over 6 months old try
replacing the fuel including that in the fuel line.
4. If the engine refuses to start, read the “Engine Tuning”
section for more help.
Servicing Your Shocks
From time to time you should check your shocks for adequate
fluid. If the fluid is low, or it is getting dirty, you should
change the fluid in the shocks. You may also want to change
the shock fluid and or the pistons to better address the
conditions you are running on. Regardless of what the reason
you will want to follow these simple steps to service, refill,
and bleed your 810 shocks. Note that if you are cleaning or
changing the fluid you will find the LOSA99217 Nitrotec
™
Spray Cleaner to be the quickest and easiest way to remove
oil fluid and dirt safely.
1. If you are changing the pistons, clean the threads on
the end of the shock shaft and apply thread locker
(LOSA99202) to the threads.
2. Install the small shock piston washer and shock piston
using the 4-40 mini lock nut on the shock shaft to
secure them.
3. Put a drop of shock fluid on the shaft before replacing
it in the shock body.
4. If you are changing the shock end use the shock tool
provided with the 810 to hold the shaft. You will see
that this plastic tool has serrations on both sides that
allow you to hold it with a pair of pliers and not scratch
up the micro finished surface. This method works very
well to protect the shock shafts from damage.
5. After installing, make sure the shaft is fully extended
when filling the shock.
6. Fill the shock body with 30–35-weight shock fluid until
it is to the top of the Body.
7. Work the shock shaft up and down a few times. This will
release the air bubbles trapped beneath the piston.
8. Place the filled shock, in the upright position, off to the
side for a few minutes until the air bubbles escape from
the fluid.
9. Once all the air bubbles are out of the fluid, gently
place the shock bladder onto the top of the shock.
Some fluid will “bleed” from around the bladder.
10. Screw the shock cap onto the body until a little
resistance is felt.
11. Slowly push the shock shaft up. This will allow excess
fluid to bleed out.
12. Tighten the cap all the way down using the shock tools
included in your kit.
13. Move the shock shaft up and down. The shaft should
be easy to push up into the body of the shock.
14. If increased pressure is felt towards the top, there is too
much oil in the shock. Loosen the shock cap and bleed
the shock as done in steps 11 & 12.
15. Make sure each pair (front/rear) of shocks has the same
rebound and compression. This is checked by holding
one shock in each hand horizontally and pushing them
together by the shock end. Watch carefully to ensure
that both compress evenly. Now release both shocks
and again; watch carefully as they should rebound the
same.