4 mmc firmware code, 5 mmc firmware upgrade procedure, 6 hot-swap process – Kontron RTM8242 User Manual
Page 24: Mmc firmware code, Mmc firmware upgrade procedure, Hot-swap process
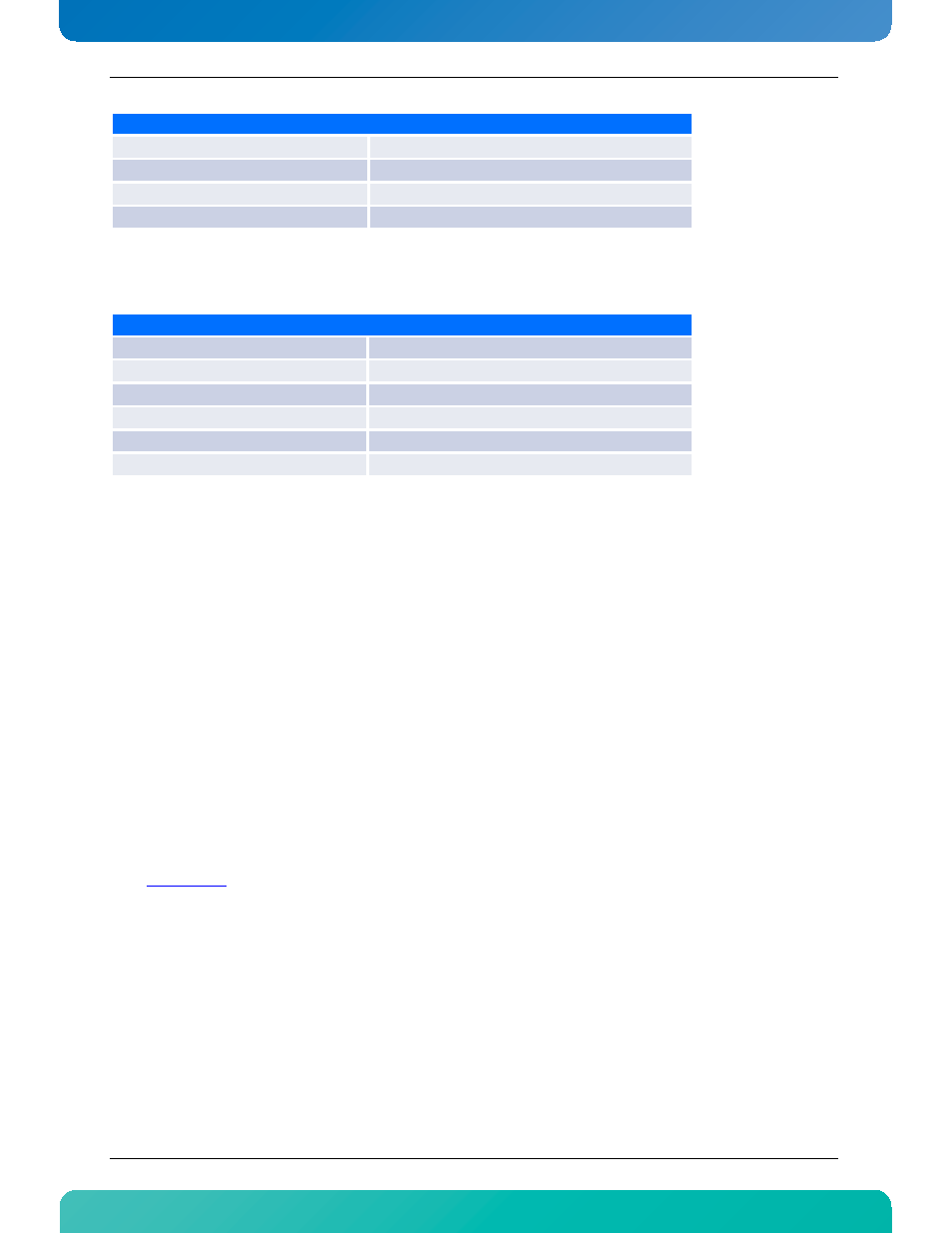
11
www.kontron.com
Table 2-7:Type 16 Module Current Requirements Records
2.5.4
MMC Firmware Code
MMC firmware code is organized into boot code and operational code, both of which are stored in internal
flash memory. Upon an MMC reset, the MMC executes the boot code and performs the following:
1 Self test to verify the status of its hardware and memory.
2 Performs a checksum of the operational code.
3 Set operational state that tells the Boot Block that the firmware operates correctly.
Upon successful verification of the operational code checksum, the firmware will jump to the operational
code.
2.5.5
MMC Firmware Upgrade Procedure
The upgrade procedure is compliant to PICMG HPM.1. MMC Firmware upgrades can be done by using IPMITOOL
from
from the front board or remotely on the chassis. It has been designed to be upgradeable
through any IPMI interface without payload impact.
2.5.6
Hot-Swap Process
The RTM8242 has the ability to be hot-swapped in and out of the front board. The onboard MMC manages the
RTM's power-up and power-down transitions. The list below illustrates this process for power down request.
1 Ejector latch is opened. MMC firmware detects the event.
2 MMC sends "Module Handle Open" event message to the front board. The corresponding M state of
the RTM moves from M4-> M5.
FRU File ID bytes
"FRU5709-YY"**
No more fields
0xC1
Padding
0x00
Product Info Area Checksum
*Calculated
Type 16 – Module Current Requirements Record
Record Type ID
C0h
Record format version
02h
Manufacturer ID
00315Ah (PICMG Record ID)
PICMG Record ID
16h (Module Power Descriptor table)
Record Format Version
00h
Current Draw
15h (2.1 Amps at 12 V => 25.2 Watts)
Product Information Area