Arc Machines 415 WDR User Manual
Page 28
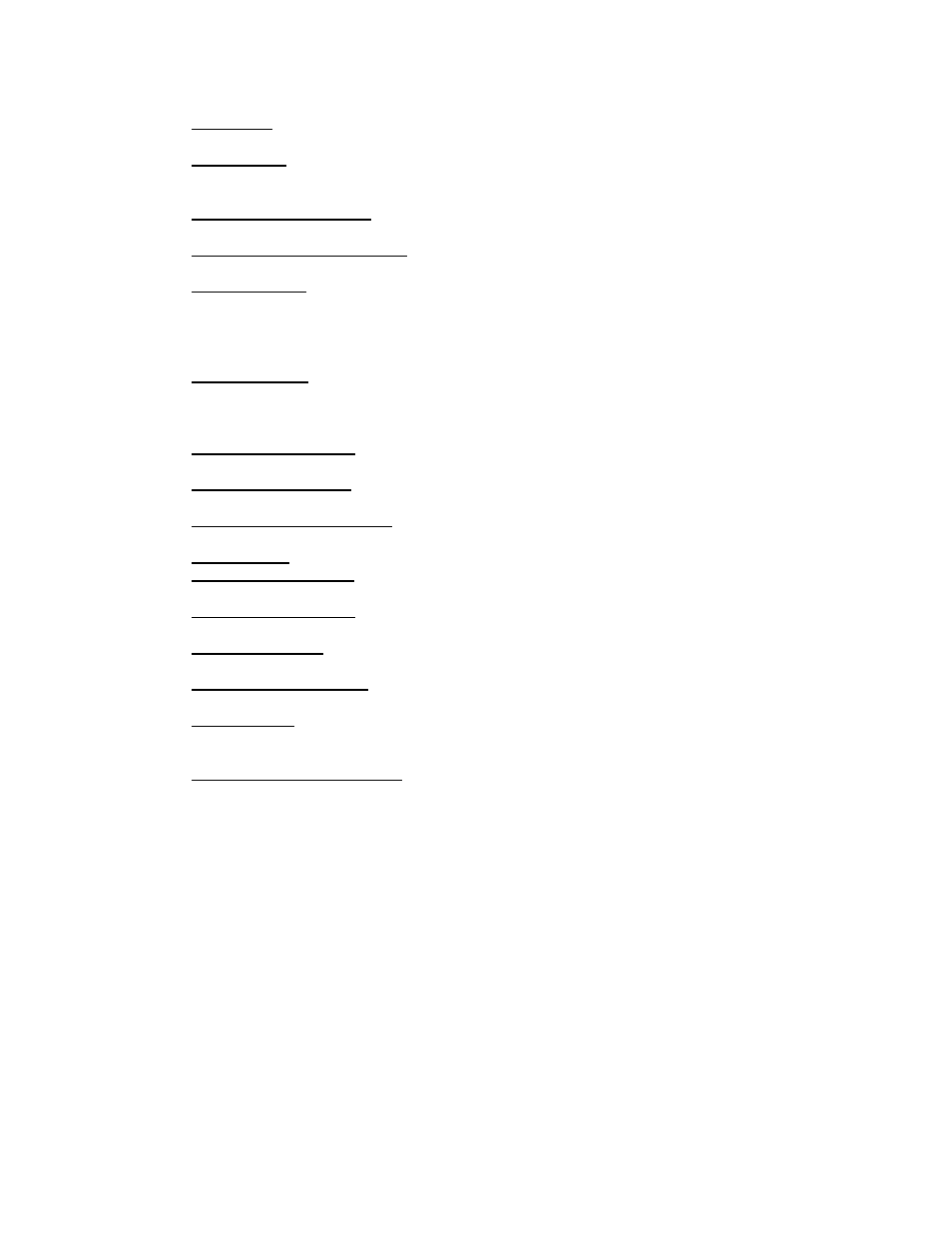
Model 415
Operation Manual
Document No. 740084
Revision N
23
3.
Wire Slope - During the period of Wire Feed Stop Delay the Wire will be sloping toward
0 IPM. When the Wire Feed Stop Delay is complete the Wire will stop running completely.
4.
Set Function - System can be set up, by weld head type to allow the operator to engage
the Set Function which will automatically position the torch (via the AVC servo) to the
correct gap for arc starting.
5.
Torch Position Indicator - Can be set up by Weld head Type to display the position of the
torch in relationship to the center of the Oscillator.
6.
Weld Head Position Indicator - Can be set up by weld head type to display the position of
the Torch in relation to Travel movement (can be in inches, mm or degrees).
7.
Override Limits - User can define how great a change an operator can make to any
overridable
function.
4.4.
SENSORS and FAULTS
1.
Torch Gas Flow - An analog flow sensor provides a signal equal to the Flow rate (CFH)
and the M-415 displays this flow rate and compares it against a program value and creates
an Sequence Stop condition if it is not correct during a weld and prevents sequence if not
correct during Pre-purge. Function is calibratable for Argon Torch gas only.
2.
Coolant Flow Sensors - Monitor coolant flow rate and creates a Sequence Stop if below
0.2 GPM. Fault can be disabled by weld head type.
3.
Coolant Level Sensor - Senses if coolant level in reservoir is low and displays to the
operator that the level is low. No fault is created.
4.
Over Temperature Sensors - Located on critical assemblies will create ALL STOP
conditions if certain assemblies get to hot.
5.
Ground Fault - Creates an ALL STOP condition if no ground return path is connected.
6.
AVC Mechanical Limit - Creates a Sequence Stop if a weld head attempts to exceeds its
AVC stroke. User can disable function by weld head type.
7.
OSC Mechanical Limit - Creates a Sequence Stop if a weld head attempts to exceed its
Oscillator stroke. User can disable function by weld head type.
8.
STUB OUT Detect - Creates an ALL STOP if arc voltage goes below 5 VDC. Can be
disabled by Weld head type.
9.
Over Voltage protection - Creates an ALL STOP if power supply output voltage during a
weld sequence exceeds 30 VDC.
10.
External Fault - Allows the user to input up to 2 outside signals that will, when actuated
from an external signal, create either an ALL STOP, Sequence Stop or WARNING as
defined by the user.
11.
Power Supply Air Flow Fault - Detects a loss of forced air cooling through the Power
Source and creates an ALL STOP condition.
4.5
PENDANT CONTROLS
The M-415 comes standard with an Operators Pendant. This Pendant has all the controls
necessary to Select Weld Schedules and passes, set up the weld head for operation, start/stop
the weld, reset faults and make overrides before and during the weld.
1.
LIBRARY (LBRY) - Key is used to access Weld Schedules.
2.
CLEAR (CLR) - Used to clear entries and reset faults.
3.
ENTER (ENT) - Used to engage an entry.
4.
ID# - Used to enter the Weld Identification number.
5.
PRE WRAP - Used to engage the Auto Wrap Function
6.
SET - Used to engage the Set Function.
7.
OSC MAN - Used to engage Oscillator Manual Mode which will, when not in sequence,
cause the Oscillator to move at the weld schedule program rate and amplitude.
8.
MAN PURGE - Used to engage the Gas Solenoid when not in sequence.
9.
WELD TEST - Sets system to TEST Mode or WELD Mode.
10.
LAMP - Used to turn the illuminating lamps on and off for torches with vision systems.