Taylor-Wharton LS Series User Manual
Page 3
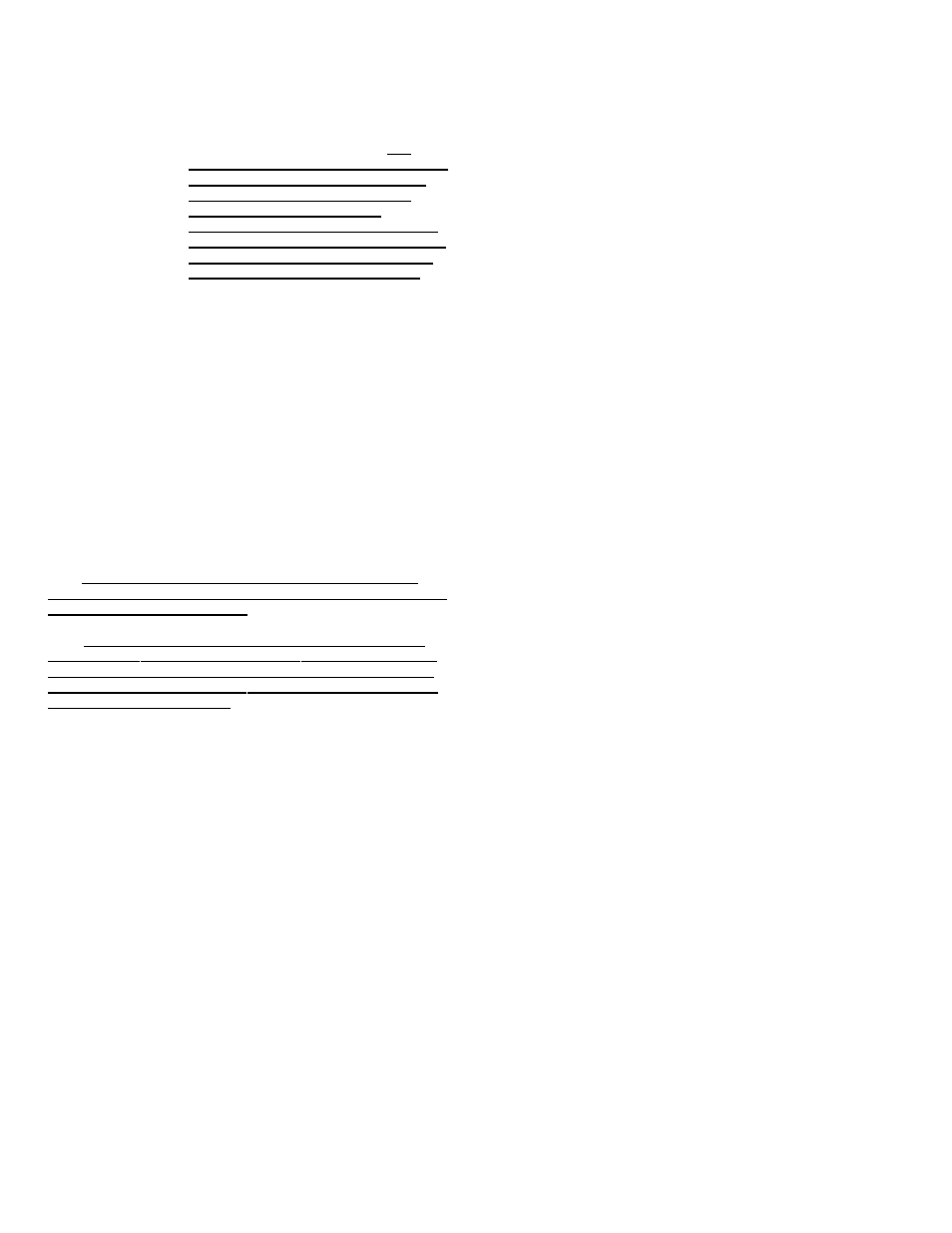
AUTO FILL OPERATION
WARNING: In order to prevent the
relief device on nitrogen
refrigerator(s) from opening when
the system is in operation, the
liquid nitrogen supply system must
be protected by a pressure relief
device that will open when the
pressure at the inlet to the
refrigerator(s) is approximately 22
psig (1.5 bar/152 kPa). Never install
the supply system pressure relief
device into a liquid service line.
Filling the Refrigerator (Initial Fill)
The LS6000-AT uses the AutoTend controller that comes
preset from the factory to operate.
The liquid nitrogen supply pressure at the inlet to the unit
should be in the range of 10 psig (0.7 bar/69 kPa) to 20
psig (1.4 bar/138 kPa) for optimum performance. Higher
operating pressures will increase transfer losses and
create excessive turbulence of the liquid in the unit which
can generate false signals to the liquid level controller
causing the unit to underfill. In liquid phase storage
applications, excessive turbulence can cause splashing
which could result in personal injury and/or damage to the
unit.
If the liquid nitrogen supply pressure at the inlet to the unit
rises above the opening pressure of the relief valve on the
unit, liquid nitrogen will be discharged into surrounding
area which can cause rapid and very dangerous depletion
of oxygen in the atmosphere. Once this pressure relief
device has opened and cooled to liquid nitrogen tempera-
ture, it will not reset until it has warmed to near ambient
temperature. THIS COULD PERMIT THE ENTIRE CON-
TENTS OF THE LIQUID NITROGEN SUPPLY SYSTEM
TO BE DISCHARGED INTO THE IMMEDIATE AREA OF
THE REFRIGERATOR(S).
WARNING:
Maintain adequate ventilation to
prevent asphyxiation hazard. (See Safety Precautions)
Power Supply Connection
Connect the 24 Volt AC power supply to the rear of the
cryostorage system; then plug the power supply into a 110/
120 VAC outlet. (See Figure 5 for the Electrical Supply
Connections.) Turn on the AutoTend by turning the key on
the front panel (see Figure 5) to the on position. The
audible alarm may sound during setup; silence the alarm
by pressing the button labeled MUTE.
WARNING: If the fill fails to stop for
any reason, quickly close the liquid
supply valve to prevent overfilling
until the cause of the problem can
be determined.
The unit is now under automatic fill control. Liquid will be
added by the controller as long as the liquid supply and
electrical power are maintained.
Operating Parameters
When materials are immersed in liquid nitrogen, they will
assume the temperature of the liquid -320° F (-196° C).
When material is stored in the vapor phase of the liquid, the
liquid nitrogen is still a very cold refrigerant, but the units
interior temperature increases somewhat as product is
stored higher above the liquid. This temperature differential is
not significant in many biological storage applications, and is
affected by the amount of product stored in the unit, the type
and size of inventory control system, and the liquid level in
the unit.
The liquid level in the unit is determined by the position of the
sensor probes in the tube located next to the fill tube. These
probes are set at installation to maintain a specific liquid
level. (See Figure 4) The cycle repeats when the liquid level
drops to the low level sensor over time. Sensor probes may
be moved to define new high and low levels, and these levels
may be set independently to vary the liquid level differential
between fills. For adjusting the temperature probes see
Changing Liquid Level section in this manual.
Vapor Phase Storage
Vapor phase storage is normally utilized when stored product
is unable to withstand liquid nitrogen temperatures, or when
the storage medium (vials, ampules, etc.) is not designed for
liquid phase storage.
In a typical vapor phase storage system, the liquid level
sensors are positioned to maintain the liquid level at or below
the top of the spider. This positioning allows stored product to
be kept at cryogenic temperatures without being exposed to
liquid nitrogen, reducing the possibility of leakage or cross-
contamination. Care must be taken in the positioning of the
level of refrigerant in the event of power outages, which may
disable the controller for an extended period of time. Consid-
eration must also be given to liquid nitrogen availability and
delivery schedules.
Liquid Phase Storage
Liquid phase storage is normally utilized when liquid nitrogen
temperatures are required to maintain stored product viability
and the storage mediums are adequate for storage in liquid
nitrogen.
In a typical liquid phase storage system, the liquid level
sensors are positioned to maintain the liquid level at or below
the top level of the inventory control system. During opera-
tion, the upper levels of the inventory control system will at
times become exposed as the liquid level fluctuates.
Care must be taken to ensure that the liquid level remains
below the bottom of the lid. Operating the refrigerator with
high liquid levels characteristic of liquid phase storage may
result in turbulence during fill cycles. Caution must be
exercised if the unit lid is opened during a fill, and appropri-
ated safety equipment should always be worn.
Sensor Positioning for the AutoTend Controller
The longer sensor probe (orange/yellow wires) contains the
Low Level sensor in a pod. The shorter probe (red/black
wires) contains the High Level sensor. The factory sensor
positions will maintain a liquid level between 2.0 in. to 4.0 in.
The dimensions used for the factory sensor installation are
shown in Figure 2.