0 connections, 1 connection resistance, 2 retorquing connections – Exide Technologies Section 93.10 User Manual
Page 16
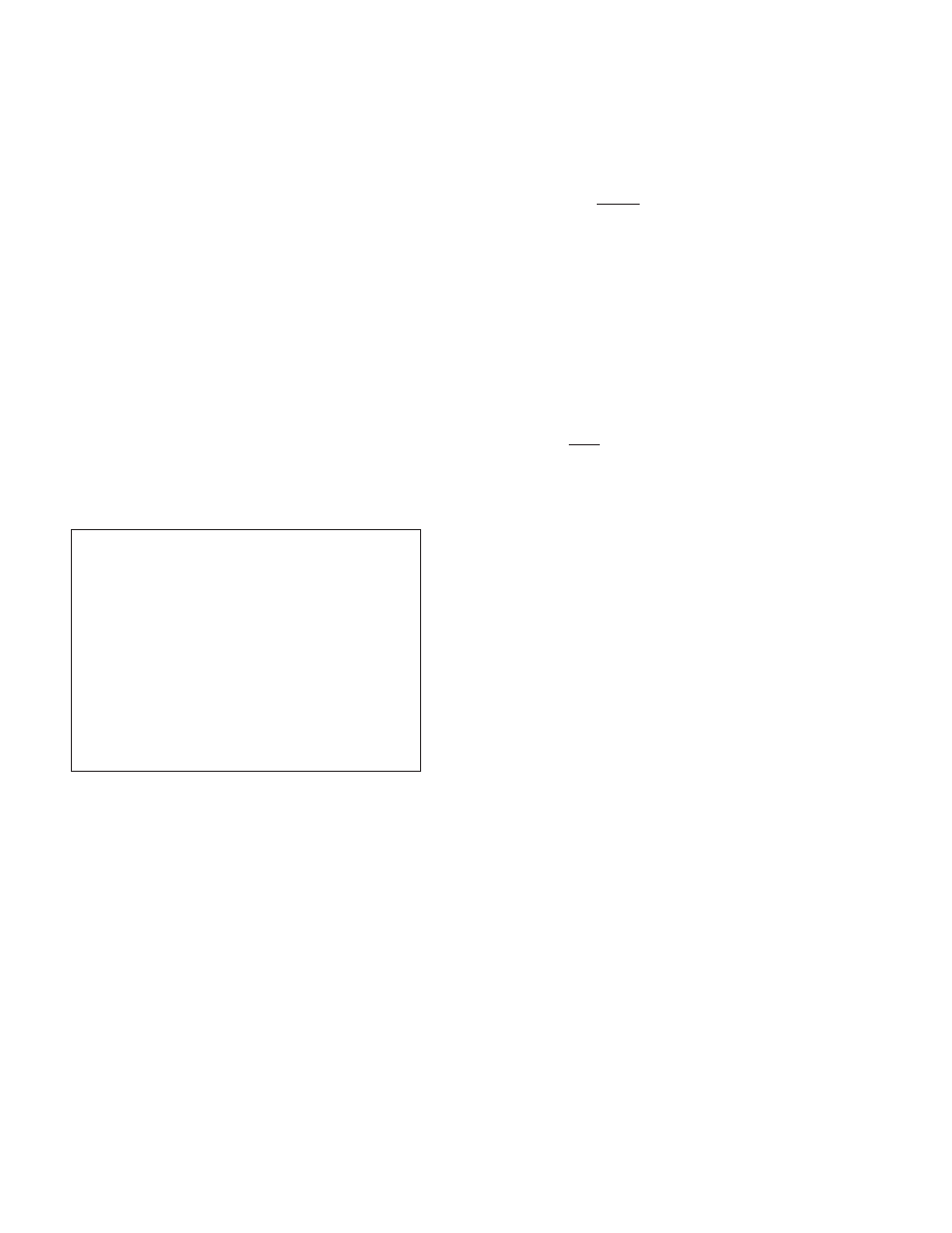
cloth. Any surface that is damp with electrolyte should be
neutralized with a baking soda—water solution (1 lb. of bak-
ing soda per gallon of water). DO NOT USE AMMONIA,
SODIUM HYDROXIDE OR ANY STRONG ALKALIES.
SECTION 19
19.0 Connections
Battery terminal connections should be corrosion free and
tight to provide satisfactory operation while supplying emer-
gency
power
and
when
on
floating
charging.
Visual monitoring of all connections should be made quar-
terly. When corrosion is observed on any connection, DO
NOT retorque.
Retorquing does not improve electrical
integrity but only restores mechanical compression. Any
connection suspected of having corrosion should be disas-
sembled, cleaned and neutralized.
All post contact sur-
faces, intercell connectors, terminal plates, cable lugs and
hardware should be neutralized using a solution of baking
soda (1 lb./gallon water). After allowing to dry, all contact
surfaces should be burnished using 3M Scotch Brite scour-
ing pads or a brass suede brush. Stubborn oxidized coat-
ings on solid lead parts may be removed using a narrow
paint scraper.
After contact surfaces are burnished, a thin coating of NO-
OX-ID grease should be applied to all contact surfaces and
hardware. The connectors and hardware should then be
reassembled and torqued per Section 7.6 - Connecting
Cells.
It is important that properly prepared contact surfaces be
coated with a thin film of NO-OX-ID grease to reduce possi-
bility of oxidation or corrosion. Tests reveal that this will also
prevent measurable increase in the connection resistance.
19.1 Connection Resistance
Electrical integrity of connections can be objectively estab-
lished by measuring the resistance of each connection.
These resistances are typically in the microhm range.
Meters are available which determine connection resistance
in microhms by measuring voltage drop upon the application
of a fixed direct current (DC) through the external cell con-
nections. Some precautions must be observed to get con-
sistent and meaningful values, however, and these are
described in Section 19.3.
13
Resistance measurements or microhm measurements
should be taken at the time of the installation and annually
thereafter. Initial measurements at installation become the
benchmark values and should be recorded for future moni-
toring of electrical integrity.
Specific values of connection resistance vary with cell type,
quantity of connectors, etc. It is important that the bench-
mark value for all similar connections should be no greater
than 10% or 5 microhms, whichever is greater, above the
average resistance of all such connections in the battery. If
any connection resistance exceed the average by more than
10% or 5 microhms, whichever is greater, the connection
should be remade so that an acceptable benchmark value
is established.
Benchmark values for connection resis-
tances should also be established for terminal plates, where
used, as well as cable connections.
Benchmark values
should preferably be established upon installation. However,
if that was not done, they may be established later provided
the special procedure described below is followed.
Disconnect the battery from the charger and load and dis-
assemble at least three (3) of the intercell connections.
Clean, neutralize and burnish these connection components
as though they had corrosion (See Section 19.0)
Reassemble each connection per Section 7.7 and deter-
mine its resistance. Measure the resistance of all similar
connections in the battery.
If any connection resistance
exceeds the average of the three remade connections by
10% or 5 microhms, whichever is greater, that connection
should be remade to establish an acceptable benchmark
value.
All benchmark values should be recorded. Annually, all con-
nection resistances should be remeasured. Any connection
which has a resistance value more than 20% above the
benchmark value should be corrected.
Increase in connection resistance of more than 20% above
the recorded benchmark definitely indicates a degrading
connection. Such degradation may be caused by corrosion
(See Section 19.0) or by relaxation in hardware torque
value. If there is no sign of corrosion, the higher resistance
at the connection may be corrected by retorquing (See
Section19.2). If connection resistance is reduced to within
20% of the benchmark value, no further action will be nec-
essary. Failure to restore resistance to an acceptable value
will necessitate reworking the connection.
Maintaining electrical integrity of connections is important
as poor connection will result in reduced battery output and
in extreme cases may cause melted cell posts, circuit inter-
ruptions or battery fires.
19.2 Retorquing Connections
Retorquing of connections should be performed annually
(See Section 9, 14) and when connection resistances have
increased to more than 20% over the benchmark.
Retorquing should not be done if visual inspection shows
evidence of corrosion. Retorquing when corrosion is pre-
sent only restores mechanical compression but will not
improve electrical integrity.
CAUTION!
1
DO NOT USE POWER WIRE BRUSH AS
THIS MAY REMOVE LEAD PLATING
EXPOSING COPPER OR CAUSE RIP-
PLING OF LEAD CONTACT SURFACES.
2.. DO NOT USE PAINT SCRAPER ON POSTS
WITH COPPER INSERTS. INTERCELL CON-
NECTORS OR TERMINAL PLATES AS LEAD
PLATING WILL BE REMOVED EXPOSING
COPPER.