Installation of carbon graphite bushings, Thrust bearing adjustment – Viking Pump TSM142.1: H-LL 225/4225 User Manual
Page 12
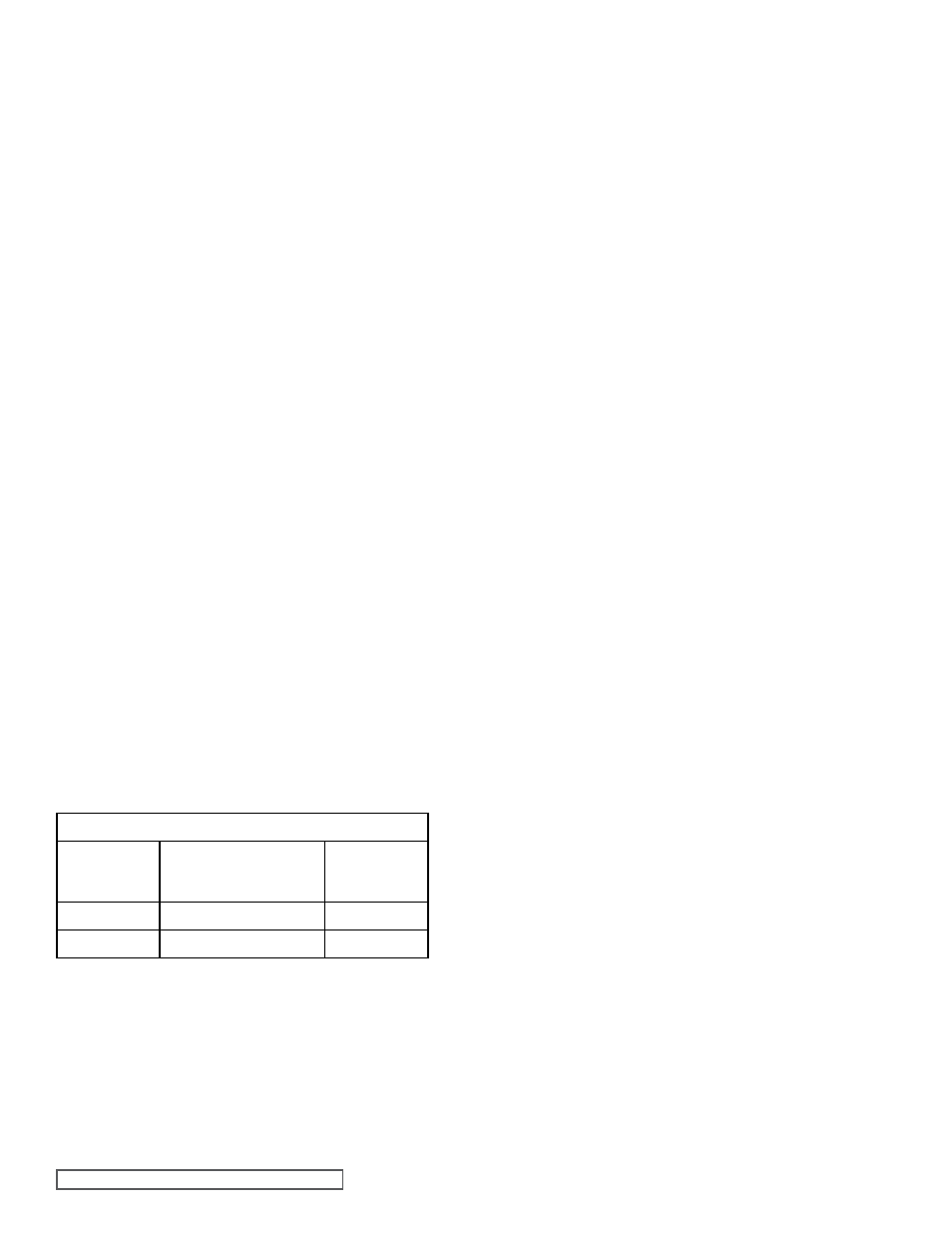
SECTION TSM 142.1
ISSUE
F
PAGE 12 OF 13
When installing carbon graphite bushings, extreme care
must be taken to prevent breaking. Carbon graphite is a
brittle material and easily cracked. If cracked, the bushing will
quickly disintegrate. Using a lubricant and adding a chamfer
on the bushing and the mating part will help in installation.
The additional precautions listed below must be followed for
proper installation:
1. A press must be used for installation.
2. Be certain bushing is started straight.
3. Do not stop pressing operation until bushing is in proper
position. Starting and stopping will result in a cracked
bushing.
4. Check bushing for cracks after installation.
Carbon graphite bushings with extra interference fits are
frequently furnished for high temperature operation. These
bushings must be installed by a shrink fit.
1. Heat bracket or idler to 750 °F.
2. Install cool bushings with a press.
3. If facilities are not available to reach 750 °F. temperature,
it is possible to install with
450 °F. temperature; however,
the lower the temperature, the greater the possibility of
cracking bushing.
Consult factory with specific questions on high temperature
applications.
Refer to Engineering Service Bulletin ESB-3.
INSTALLATION Of CARBON
gRAPHITE BUSHINgS
TOTAL END CLEARANCE CHART
PUMP
SIZE
TURN OUTER END CAP
COUNTER-CLOCKWISE
NO. Of NOTCHES
TOTAL
END
CLEARANCE*
H & HL
5
.007
K - LL
8
.010
THRUST BEARINg ADJUSTMENT
1. Loosen setscrews over outer and inner end caps. Two
for H and HL size pumps, four for all other sizes.
2. Turn inner end cap clockwise, viewed from shaft end, until
it projects slightly from bracket exposing approximately
three threads.
3. Turn outer end cap clockwise until rotor is tight against
head and rotor shaft cannot be turned.
4. Make a reference mark on bracket end, opposite a
notch on outer end cap. Back off outer end cap required
number of notches.
Refer to figure 14.
Each 0.25 inch travel on circumference of end cap is
equivalent to approximately .0015 inch for all sizes.
5. End clearances set per Step 4 are adequate for
viscosities up to 750 SSU (SAE20 lube oil at room
temperature). Higher viscosity liquids require additional
end clearances.
As a general guideline, for viscosities between 750 and
7500 SSU (heavier lube oils) double the amount of end
clearance indicated in Step 4; for viscosities between
7500 and 75,000 SSU (e.g., resins) triple the amount
and for viscosities greater than 75,000 SSU (e.g., black
strap molasses) use 4 times the amount.
For specific recommendations for end clearances for
viscosity or for operating temperatures above 225 °F,
check with your Viking representative or consult the
factory.
6. Tighten inner end cap with a spanner wrench. Tap
spanner wrench lightly but
DO NOT OVER TIgHTEN as
it will only damage the threads.
7. Tighten all setscrews that hold inner and outer end caps
to prevent their turning in the bracket.
8. Rotor and shaft should turn smoothly by hand one
complete revolution. If rotor and shaft doesn’t turn
smoothly, go back and repeat
Thrust Bearing
Adjustment Steps 1 thru 8.
* Total End Clearance includes extra clearance for
temperatures of 450°f.
fIgURE 14