3 discharge conditions and reaction forces, 3 valve connecting dimensions, 4 flange caps and gaskets – Richter LPV/F Series Low-Pressure Safety Valves User Manual
Page 10: 5 weights, 6 direction of flow and installation position, 7 grounding, Discharge conditions and reaction forces, Valve connecting dimensions, Flange caps and gaskets, Weights
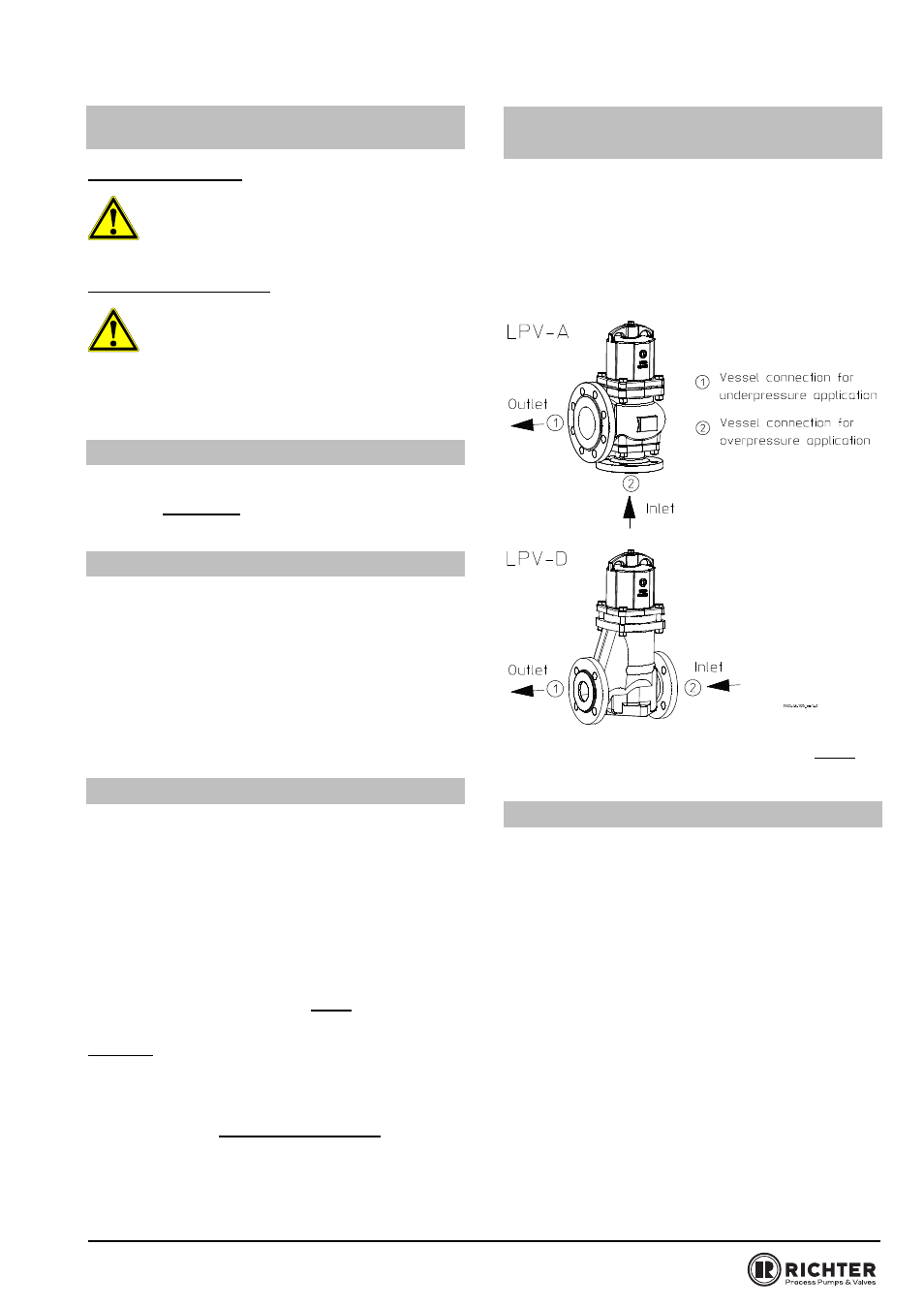
Series LPV-A/F, LPV-D/F
Seite 10
9530-060-en
Revision 01
TM 7464
Edition 02/2009
6.2.3 Discharge conditions and reaction
forces
At low temperatures:
Outlet lines must be protected against
freezing. This applies in particular if gas
cooling as a result of expansion is to be
expected or lines are laid outdoors.
With crystallising media:
In the case of media which tend to
crystallise, solidify or stick, appropriate action
must be taken to ensure that the
solidification process cannot take place in
the inlet or outlet lines or in the body (e.g. installed
rupture disc, insulation, heating).
6.3 Valve connecting dimensions
The main dimensions are contained in the sectional
drawing in Section 10.
6.4 Flange caps and gaskets
Contamination of or damage to the sealing
surfaces is best avoided if the protective caps
remain on the flanges until just before installation.
If plastic sealing surfaces can be damaged, e.g. with
mating flanges made of metal or enamel, use PTFE-
lined seals with a metal inlay.
These are available as special accessories from the
Richter product range.
6.5 Weights
The test pressure is varied with max. 5 weights, either
plastic-lined with metal core (20 mbar each) or of solid
PTFE (5 or 10 mbar each).
The weights are marked with the appropriate mbar
values.
The round cord 522 secures the weights 239 in the
groove of the plug 204 together with the retainer ring
544.
The test pressure of he valve depends on the back
pressure in the valve outlet (see Fig. 1).
Set pressure = test pressure + back pressure
Example:
Test pressure = 100 mbar
Back pressure =
10 mbar
Set pressure
= 110 mbar
See also enclosed Drawing 9530-00-4070
6.6 Direction of flow and
installation position
The direction of flow must be observed when installing
the valve. It is indicated by a direction arrow on the
valve body.
Always install the overflow valve with the plug in a
vertical position.
A mix-up of the inlet and outlet will result in the valve
becoming ineffective.
Fig. 1
6.7 Grounding
The valve must be grounded. The simplest solution is
to use tooth lock washers which are placed under one
pipe bolt of each flange.
At the customer's request a setscrew M6 with a hex.
nut and washer will be provided at each flange as an
additional grounding connection.
Otherwise grounding must be ensured by different
measures e.g. a cable link.