5 final assembly, 6 fill bearing pedestal with oil, 9 tests – Richter RMI Series User Manual
Page 21: Final assembly, Fill bearing pedestal with oil, Tests, Series rmi
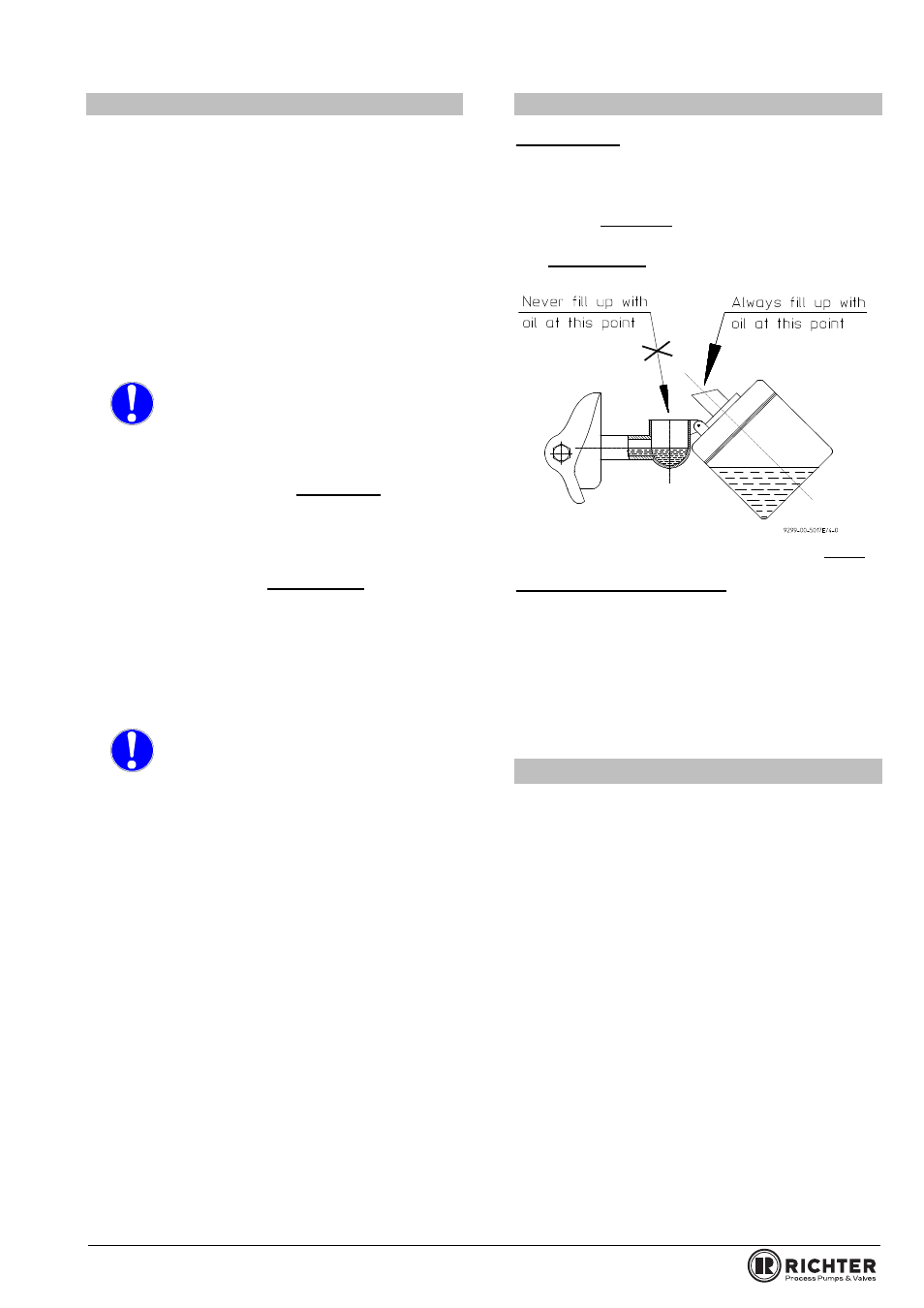
Series RMI
Page 21
9470-050-en
Revision 00
TM 7978
Edition 08/2010
7.8.5 Final assembly
Deposit the housing 100 on a workbench, for
example, with the suction nozzle facing
downwards. In doing so, protect the plastic sealing
strip against damage with a suitable base.
Insert housing gasket 401 into the centering of the
housing 100.
Mount pre-assembled slide-in unit concentrically
onto the shaft spider 338.
Pres outer wear ring 502/1 into the housing 100.
Insert pre-assembled can unit. The lip of the can
insert 158 must rest on the housing gasket 401.
Press shaft 222 carefully through the
bearing bushes 545 into the shaft
spider 338. (Risk of the silicon carbide
breaking)
Mount bracket 344 and tighten hex. screws 901/3
to the required torque, see Chapter 1.1.
Check whether the rotating unit has the necessary
axial play. For this purpose reach through the
suction nozzle and move the rotating unit axially.
The axial play can be determined through the
discharge nozzle. See Chapter 7.7.1.
If the minimum axial play is not attained, insert
another housing gasket 401.
Insert bearing pedestal gasket 404 into the
appropriate location on the bracket 344.
Insert pre-assembled drive unit into the centering
of the bracket 344.
When inserting the unit, high axial
magnetic forces occur which decrease
abruptly after reaching maximum. Only
hold the bearing pedestal in front of the
flange (on motor side).
(Risk of injury from being squeezed)
Alternatively, the unit can be mounted using a
crane. A thread is provided in the drive shaft to
accommodate a crane lug.
Tighten screws 901/5.
Tightening torque group 1.1 + 1.2 = 40Nm
Tightening torque group 1.3
= 55Nm
Check whether the drive shaft can be easily
turned.
Press plugs into the forcing-off bores.
Attach support bracket 183 (with bearing pedestal
group 2), align and tighten.
7.8.6 Fill bearing pedestal with oil
Oil quantities:
For group 1.1
appr. 400 ml
For group 1.2
appr. 600 ml
For group 1.3
appr. 1000 ml
Groups see Chapter 1.
See Chapter 7.2.2 for the type of oil.
Fig. 9
Procedure for filling with oil:
Tilt constant level oiler 638/1.
Fill the oiler with oil.
Swing the constant level oiler into the vertical
position.
If the oil level still falls too much, pour more oil
into the oiler.
7.9 Tests
On request, the pumps are tested with water at the
manufacturer's.
The operating data measured are then documented
in a works test certificate.
If, during a test after repairs, discrepancies
compared with the works certificate are discovered,
the following people can be called in:
1. in-house pump office
2. The manufacturer Richter
or its local agent
The following conveying data can be checked using
the pump performance curves:
Flow rate
Head
Power requirement
NPSHR