3 dismantling of drive unit oil bath lubrication, 4 dismantling of slide-in unit, 5 dismantling housing/shaft spider – Richter RMI Series User Manual
Page 18: 6 changing the radial ball bearings, Lubrication, Dismantling of drive unit oil bath lubrication 18, Dismantling of slide-in unit, Dismantling housing/shaft spider, Changing the radial ball bearings, Series rmi
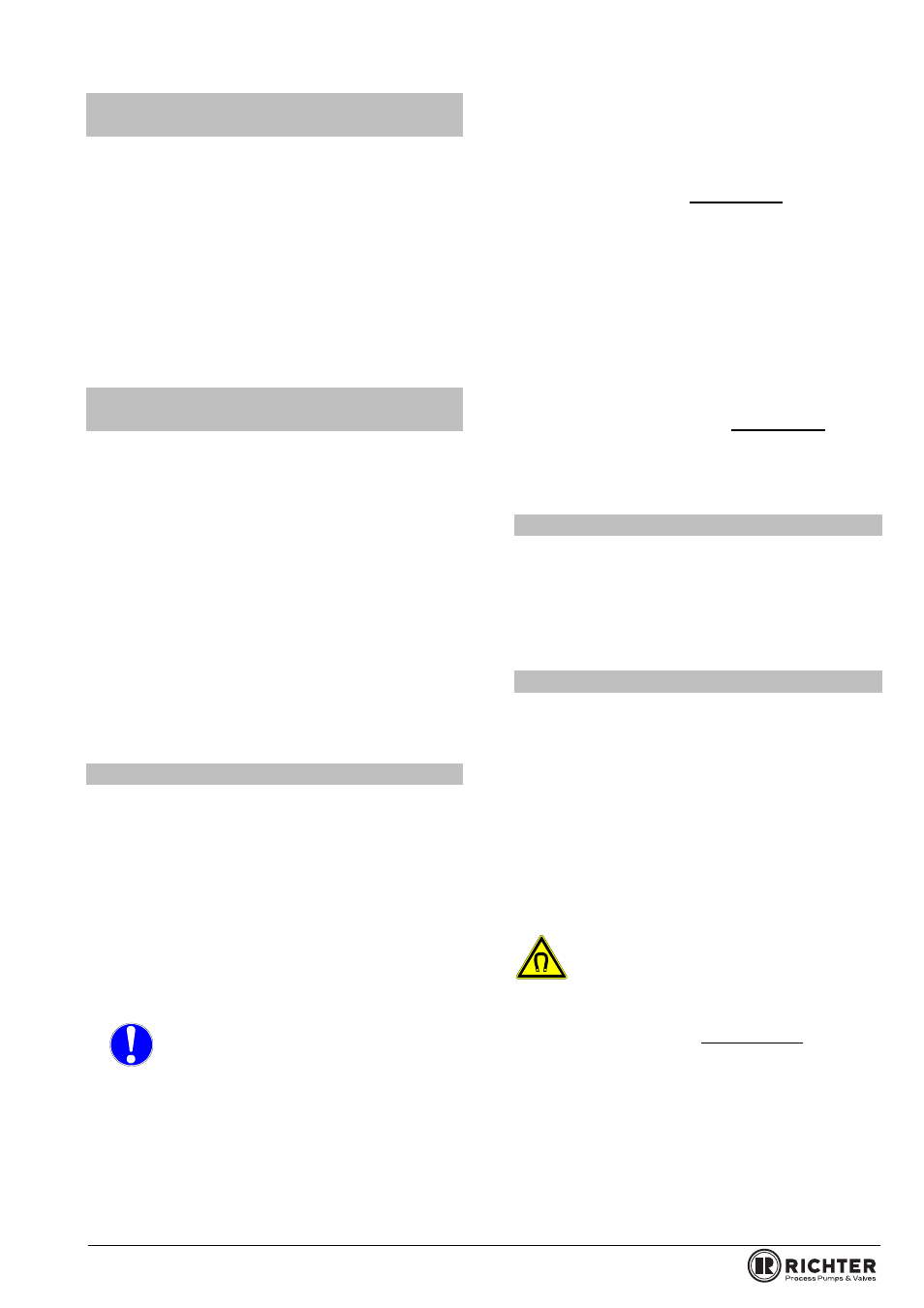
Series RMI
Page 18
9470-050-en
Revision 00
TM 7978
Edition 08/2010
7.6.2 Dismantling of drive unit
long life grease lubrication
Undo hex. socket screw 914/5 with toothed lock
washer 936/1.
Remove drive magnet assembly 858. If necessary,
use a pulling-off device.
Undo screws 914/6 of the rear bearing cover 361.
Remove rear bearing cover 361 and wavy spring
washer 953/1.
Press drive shaft 213 with the two ball bearings
321/1 and 321/2 out of the bearing pedestal 330 in
the direction of the motor.
7.6.3 Dismantling of drive unit
oil bath lubrication
Undo hex. socket screw 914/5 with toothed lock
washer 936/1.
Remove drive magnet assembly 858. If necessary,
use a pulling-off device.
Drain oil from the screw plug 903/1.
Undo screws 914/6 of the rear bearing cover 361.
Press drive shaft 213 with the two ball bearings
321/1 and 321/2 out of the bearing pedestal 330 in
the direction of the motor.
Remove from the drive shaft 213 rear bearing
cover 361 incl. radial ball bearing 421/1 with cover
gasket 403 and wavy spring washer 953/1.
Remove rotary shaft seal 421/2 from the bearing
pedestal 330 resp. the rear bearing cover 361.
7.6.4 Dismantling of slide-in unit
Undo housing screws 901/3.
Screw 2 hex. screws 901/3 into the forcing thread
of the bracket 344.
Press the housing 100 with the aid of these hex.
screws out of the bracket 344.
Remove bracket 344 with bearing pedestal gasket
404 upwards.
Raise can 159 and can insert 158. As the shaft
222 is introduced tightly into the can insert 158,
this shaft is automatically removed together with
the thrust ring 510/3.
Make sure that no plain bearing parts fall
down. Risk of breakage!.
Remove the shaft 222 and thrust ring 510/3 from
the can insert 158. Insert a suitable tool, e.g. a
scribing tool, behind the thrust ring and pull it out
by repeatedly inserting the tool.
Remove housing gasket 401.
Raise inner magnet assembly 859 vertically with
the impeller 230. The wear ring 502/1 is removed
from the housing 100 at the same time.
Remove thrust ring 510/2 using a screwdriver.
Press the bearing bushes 545 and distance ring
504/1 off the impeller from the suction side. Use a
suitable mandrel made of plastic.
Alternatively, the pull-off device can also be used.
See assembly aids in Chapter 10.2.
Remove anti-torsion insert 566/2.
The circlip 932/7 must be destroyed to separate
the impeller 230 and inner magnet assembly 859.
For this purpose, carefully cut the circlip open
with a cutting knife all around the notch.
Press impeller 230 out of the seat of the inner
magnet assembly 859. For this purpose, clamp
the inner magnet assembly 859 in a vice, being
careful not to damage the surfaces, and press the
impeller 230 out towards the suction side.
Alternatively, the dismantling device can also be
used. See assembly aids in Chapter 10.3.
Carefully remove the remaining parts of the circlip
932/7.
7.6.5 Dismantling housing/shaft spider
Pull shaft spider 338 out of the housing seat.
Remove the two anti-torsion inserts 566/1.
Remove shaft sleeve 523/1 from the shaft spider
338.
7.6.6 Changing the radial ball bearings
To change the radial ball bearings 312, only the
bearing pedestal unit can alternatively be
removed from the plant.
Undo support bracket 183 from the base plate.
Undo
screws
901/5
of
the
connection
bracket/bearing pedestal.
Remove bearing pedestal 330 for the centering of
the bracket 344. If necessary, use two levers.
To overcome the axial magnetic forces, pull the
bearing pedestal 330 with a firm jerk in the
direction of the motor.
CAUTION! When pulling out the bearing
pedestal, the axial magnetic forces (up
to max. 400 N without weight force)
decrease abruptly after being at maximum. Risk
of accident!
For further procedure, see Chapter 7.6.2.