Ustang, Eries – Watts M1110-14 User Manual
Page 5
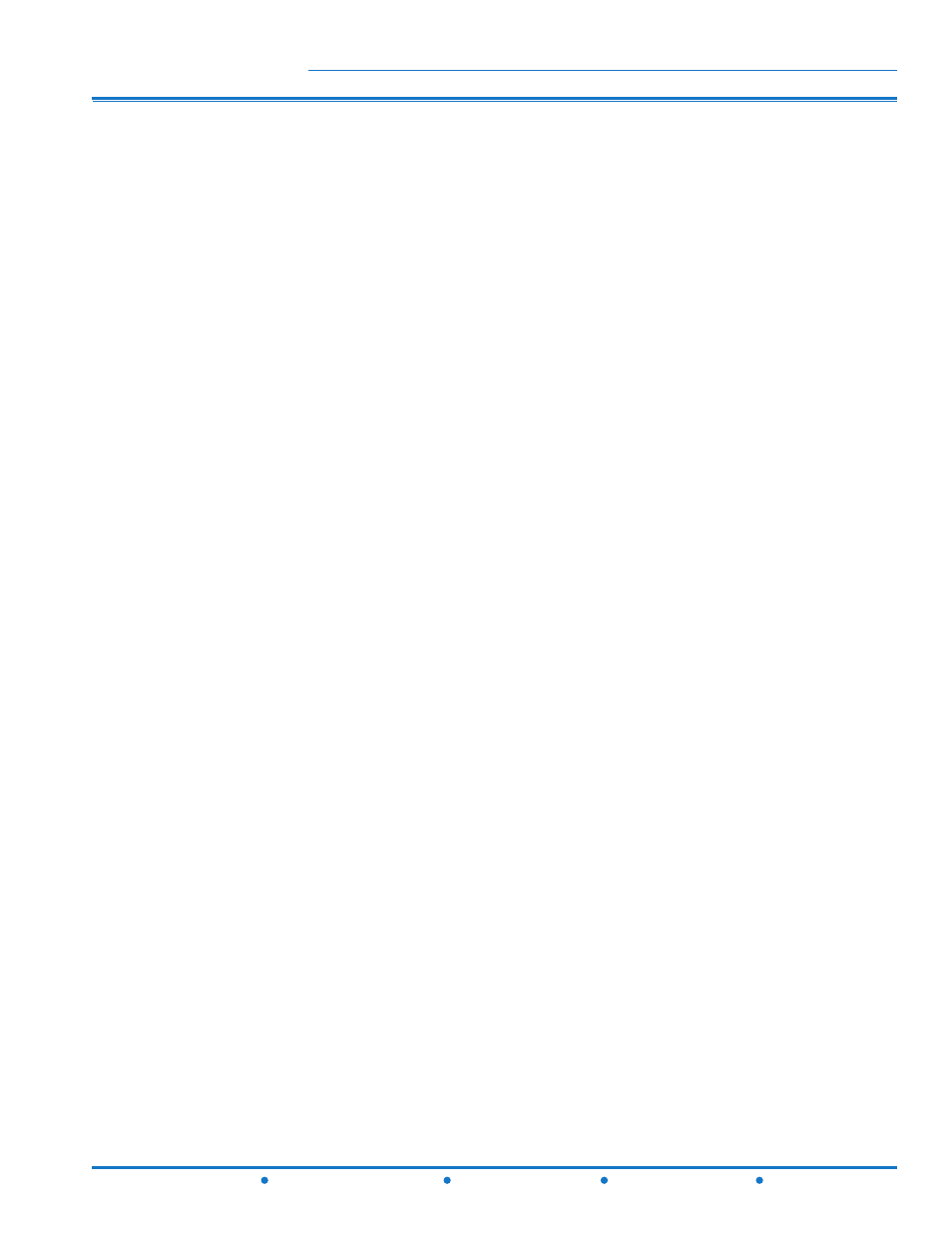
2 4 6 8
10
20
40
60 80 100 200 500 1000 2000 5000 10000 20000
100000
M
ustang
s
eries
12541 Gulf Freeway
•
Houston, Texas 77034
•
(Ph) 713.943.0688
•
(Fx) 713.944.9445
•
www.watts.com
M110-14 (Globe)
M1110-14 (Angle)
Proper Automatic Control Valve start-up requires bringing the valve into service in a controlled manner. All adjustments
to control pilots and speed controls should be made slowly, allowing the valve to respond and the system to stabilize.
NOTE: Control Valves should be set‑up in a dynamic (flowing) condition for proper start‑up. Provisions for
flow must be made to insure proper settings.
• If Float Control is remote mounted, field installed control lines should be 3/8” minimum copper tubing for dis-
tances no greater than 10 feet. For greater distances use 1/2” minimum copper tubing or pipe.
• Remote mount – without Accelerator (4” and smaller):
Port 1 = Supply Pressure
Port C = Valve Cover
Port 2 = Atmosphere
• Remote Mount – with Accelerator (6” and larger):
Port 1 = Atmosphere
Port C = Accelerator Cover
Port 2 = Supply
1. Close upstream and downstream valves to isolate the valve from line pressure. Open all Isolation Ball Valves,
if so equipped. If valve is fitted with adjustable speed controls, turn needle(s) in (clockwise) until seated, and
return out (counterclockwise) 1‑1/2 to 2‑1/2 turns. These are approximate settings, and should be fine tuned to
suit system requirements after level adjustments have been made.
2. Slowly open upstream isolation valve to allow controlled filling of the valve. Vent entrapped air by carefully
loosening control tubing or pipe plug at the highest point possible. If valve is equipped with a Position Indicator,
open Air Bleed Petcock to vent air. Water will be milky in appearance and will begin to clear as air is vented.
Re-tighten when water vents clearly.
3. Setting Float Control: Install desired number of Float Rods and Low and High Level Stop Collars (less Float).
Manually position Float Control to the center point in its travel and balance by positioning Counterweight “in” or
“out” until Float Control holds in position. Proper balance is achieved when Float Control moves to the “down/
on” or “up/off” position with minimal force or drag. The position of Counterweight on the Counterweight Rod
will vary based upon the number and material of Float Rods being used. Install Float.
4. Position Low and High Level Stop Collars on Float Rods to match desired valve opening and closing levels.
Slowly open downstream isolation valve.
5. Fine tune Speed Controls (if equipped) to suit system requirements. Adjust Closing Speed Control clockwise
for slower closure and counterclockwise for faster closure. Adjust Opening Speed Control clockwise for slower
opening and counterclockwise for faster opening.
Start-Up
Installations
• Prior to installation, flush line to remove debris.
• Install valve horizontally “in line” (cover facing UP), so flow arrow matches flow through the line.
Avoid installing
valves 6” and larger vertically. Consult factory prior to ordering if installation is other than described.
• Install inlet and outlet isolation valves.
NOTE: When using butterfly valves, insure disc does not contact control
valve. Damage or improper valve seating may occur.
• Provide adequate clearance for valve servicing and maintenance.
• Install pressure gauge to monitor valve inlet pressure.
• Provide adequate drain for cover chamber discharge. Consult “Valve Cover Capacity” chart on appropriate main
valve Engineering Bulletin.
• If On‑Off Float Pilot is remotely mounted it should be field connected with 3/8” minimum copper tubing in accordance
with factory piping schematic.
• Float Pilot, Rods, and Ball should be mounted in a field installed “stilling well” for protection against surface turbu-
lence and interference.
• Additional 12” Float Rods available. Consult Factory.
910 Ops & Inst