Selection procedure, Maximum flow rates, Oil temperature – Thermal Transfer Systems A Series User Manual
Page 6: Desired reservoir temperature
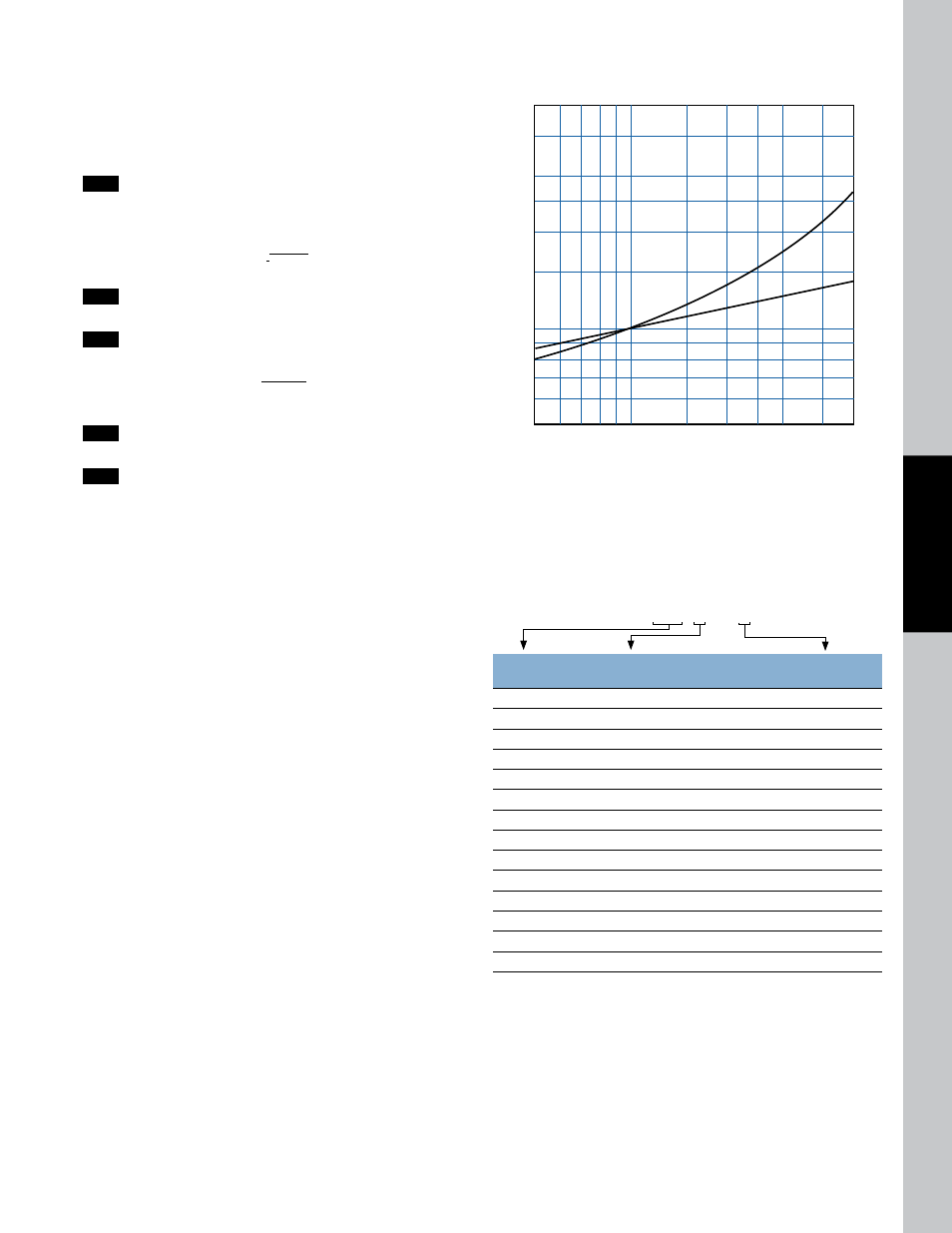
A
www.thermaltransfer.com
262.554.8330
113
W
A
T
E
R C
O
O
L
E
D
A
Caution: Incorrect installation can cause this product to fail prematurely, causing the
shell side and tube side fluids to intermix.
Maximum Flow Rates
5
4
3
2.5
2
1.5
1
.8
.7
.6
.5
50 60 70 80
100
150
200 250 300
400 500
A
B
OIL VISCOSITY - SSU
VISCOSITY CORRECTION
Selection Procedure
Performance Curves are based on 100SSU oil leaving the cooler 40°F
higher than the water temperature used for cooling. This is also referred to
as a 40°F approach temperature. Curves are based on a 2:1 oil to water
flow ratio.
Step 1
Determine the Heat Load. This will vary with different systems,
but typically coolers are sized to remove 25 to 50% of the input
nameplate horsepower. (Example: 100 HP Power Unit x .33 = 33
HP Heat load.)
If BTU/Hr. is known: HP = BTU/Hr
2545
Step 2
Determine Approach Temperature. Desired oil leaving cooler °F
– Water Inlet temp. °F = Actual Approach (Max. reservoir temp.)
Step 3
Determine Curve Horsepower Heat Load. Enter the
information from above:
Horsepower heat load x 40 x Viscosity Curve
Actual Correction A
=
Horsepower
Approach
Step 4
Enter curves at oil flow through cooler and curve horsepower.
Any curve above the intersecting point will work.
Step 5
Determine Oil Pressure Drop from Curves:
j
= 5 PSI; M = 10 PSI; l = 20 PSI. Multiply pressure drop from
curve by correction factor B found on oil viscosity correction curve.
Oil Temperature
Oil coolers can be selected using entering or leaving oil temperatures.
Typical operating temperature ranges are:
Hydraulic Oil
110°F - 130°F
Hydrostatic Drive Oil
130°F - 180°F,
Bearing Lube Oil
120°F - 160°F
Lube Oil Circuits
110°F - 130°F.
Desired Reservoir Temperature
Return Line Cooling: Desired temperature is the oil temperature leaving the
cooler. This will be the same temperature that will be found in the reservoir.
Off-Line Recirculation Cooling Loop: Desired temperature is the oil
temperature entering the cooler. In this case, the oil temperature change
must be determined so that the actual oil leaving temperature can be
found. Calculate the oil temperature change (oil sT) with this formula:
Oil sT = (BTU’s/Hr.) / (GPM Oil Flow x 210).
To calculate the oil leaving temperature from the cooler, use this formula:
Oil Leaving Temp. = Oil Entering Temp – Oil sT.
This formula may also be used in any application where the only
temperature available is the entering oil temperature.
Oil Pressure Drop: Most systems can tolerate a pressure drop through the
heat exchanger of 20 to 30 PSI. Excessive pressure drop should be avoided.
Care should be taken to limit pressure drop to 5 PSI or less for case drain
applications where high back pressure may damage the pump shaft seals.
Example Model No.
A - 1024 - 2 - 6 - F
Unit
Baff le
Shell Side
Tube Side (GPM)
Size
Spacing
(GPM)
O
T
F
400
.75, 2
7, 19
18
–
–
608
1, 2
14, 29
48
24
12
614
1.5, 4
21, 29
48
24
12
624
2, 4
29
48
24
12
814
1.5, 3
29, 57
87
44
22
824 & 836
2, 4
38, 69
87
44
22
1014
1.5, 3
32, 64
146
73
37
1024 & 1036
2, 4
42, 69
146
73
37
1224
2, 4
51, 103
224
112 56
1236 & 1248
3, 6
77, 115
224
112 56
1260
4, 6
103, 115
224
112 56
1624
2, 6
66, 200
280
140 70
1636 & 1648
3, 6
100, 200
280
140 70
1660 & 1672
4, 6
133, 200
280
140 70