S&S Cycle Big Twin Oil Pump Kits User Manual
Page 17
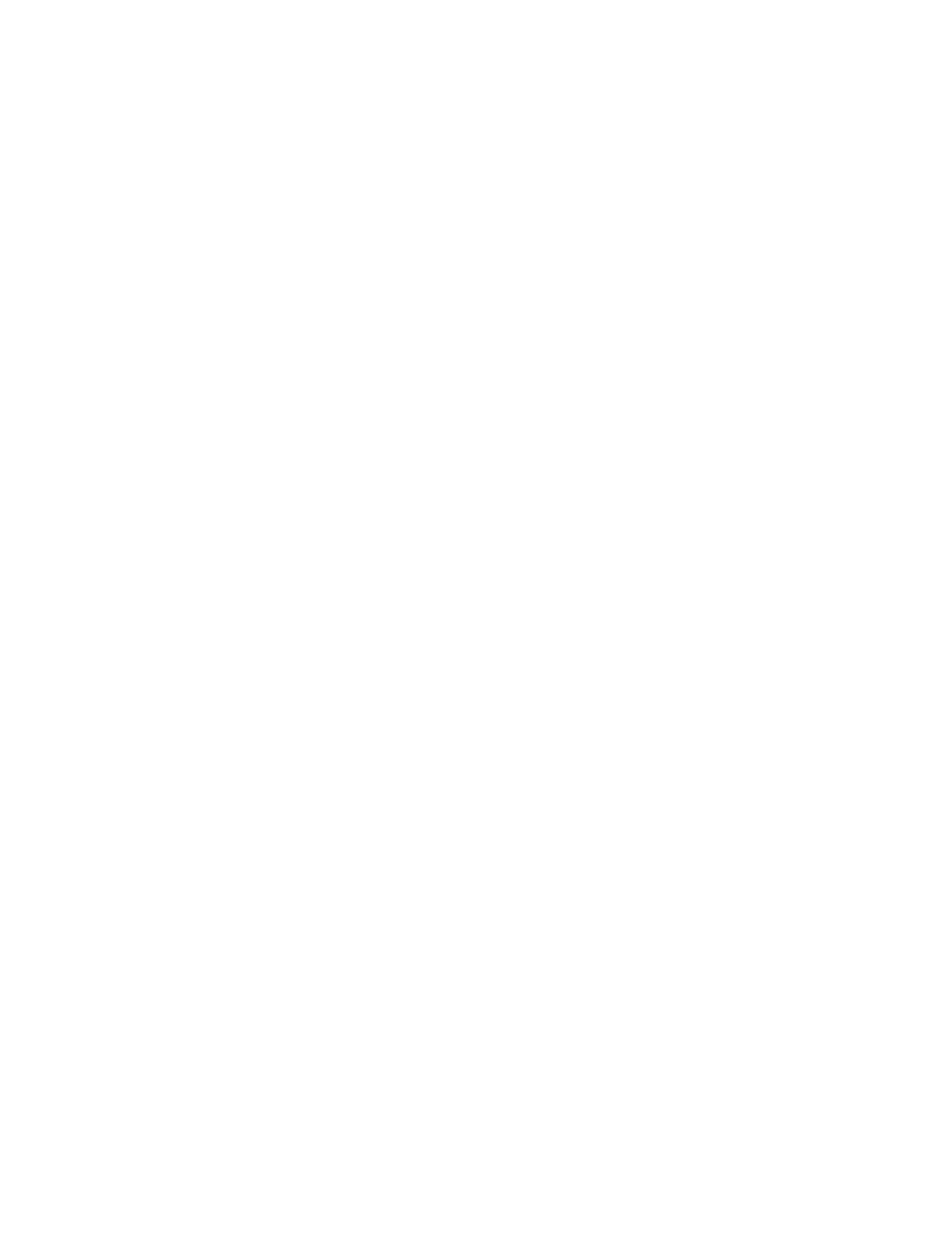
17
NOTES:
●
Low oil pressure is often blamed on oil pump when
actual cause is worn bearings, bushings or other
internal component. A new oil pump will not repair worn
parts and excessive operating clearances. If low oil
pressure exists after new oil pump installation, check
bearing clearances and other possible causes such as
installation of different gear cover, tappet guides etc.
●
With engine hot, typical oil pressure reading is 3-4
PSI at 1000 RPM idle, 12-15 PSI at normal highway
speeds or approximately 2500 RPM. Faulty oil pressure
gauge should not be overlooked as possible source if
low pressure reading is encountered. H-D “idiot” light
comes on at approximately 3 PSI, and is fairly reliable.
Light may flicker at low RPM, but should quickly go out
with slight increase in engine speed.
●
Sudden clatter in previously quiet hydraulic lifter
may indicate lifter failure OR excessively low oil
pressure, and should be investigated. It is not unusual
for hydraulic lifters to clatter when a new or recently
rebuilt engine is first started, but noise should disappear
within a reasonable amount of time as lifters pump up.
Time required depends on several factors including
brand of lifter, oil viscosity rating, and temperature.
●
Dyna Glides, late FLís and other models with oil
tank below transmission require precautions to prevent
air entering oil pump during oil changes if S&S Custom
Billet pump cover #31-6045 is used or if top oil supply
fitting location is utilized on ìUniversal Coverî #31-6047.
If oil lines are rubber, supply line from tank should be
clamped during oil changes on these models, and
clamp removed after tank has been refilled. If it is not
possible to clamp lines, oil circulation must be confirmed
after each oil change.
●
Increased oil volume generated by S&S pump may
overwhelm stock scavenging system in Knucklehead
top end. If oil return becomes a problem, it can be
corrected by metering oil supply to heads. Oil fitting for
top end supply line can be filled with solder and orifice
drilled in solder for this purpose. S&S has performed
tests and has successfully operated engines including
Panheads and Shovelheads with metering holes as
small as .060". Some Knucklehead owners have
installed S&S carb main jet in cam cover top end oil
supply fitting for same purpose, and adjusted oil flow
with different size jets.
●
Paper gaskets are supplied as standard with each
kit. S&S recommends paper gaskets but can provide
mylar gaskets for 1936 to 1991 engines if desired.
CAUTION: “Air lock” or cavitation can occur if
trapped air is not released from oil pump after
installation. It can occur with new pump as well as
used pump that has been removed from engine, and
interferes with oil circulation. It is owner’s
responsibility to remove trapped air by priming pump
prior to running engine and to confirm correct pump
operation.
I.
Install pinion shaft oil pump drive gear, pinion
gear and remaining parts in gearcase following
standard H-D procedure. Note that pinion shaft
oil pump drive gear has chamfer on one side.
Place gear on pinion shaft with chamfer toward
shoulder on shaft, facing center of engine.
Connect oil lines.
CAUTION: Installing pinion shaft oil pump drive gear
backwards on pinion shaft may cause stress riser
resulting in eventual failure of shaft.
9. Initial Startup and Post-operation Checks -
All Years
After pump has been installed and primed, oil lines
connected in correct manner and oil tank filled to
correct level, confirm oil circulation with oil pressure
gauge and by removing cap from oil tank and
observing oil return to tank. If oil is not seen returning
to tank, S&S recommends removing return line from
tank and placing end in drain pan to confirm oil
circulation.
NOTE - Engine oil circulates under pressure. Areas
exposed to escaping oil should be covered with rags
and engine turned off immediately after oil circulation is
confirmed to minimize oil loss.
WARNING - Oil on tires or brakes can cause loss of
control of motorcycle resulting in serious injury to
operator and others.
A. After confirming oil circulation run engine for
several minutes and check for leaks.
B. If applicable, adjust primary and rear chain
oilers as needed.