Longevity ARCMATE 205 User Manual
Page 31
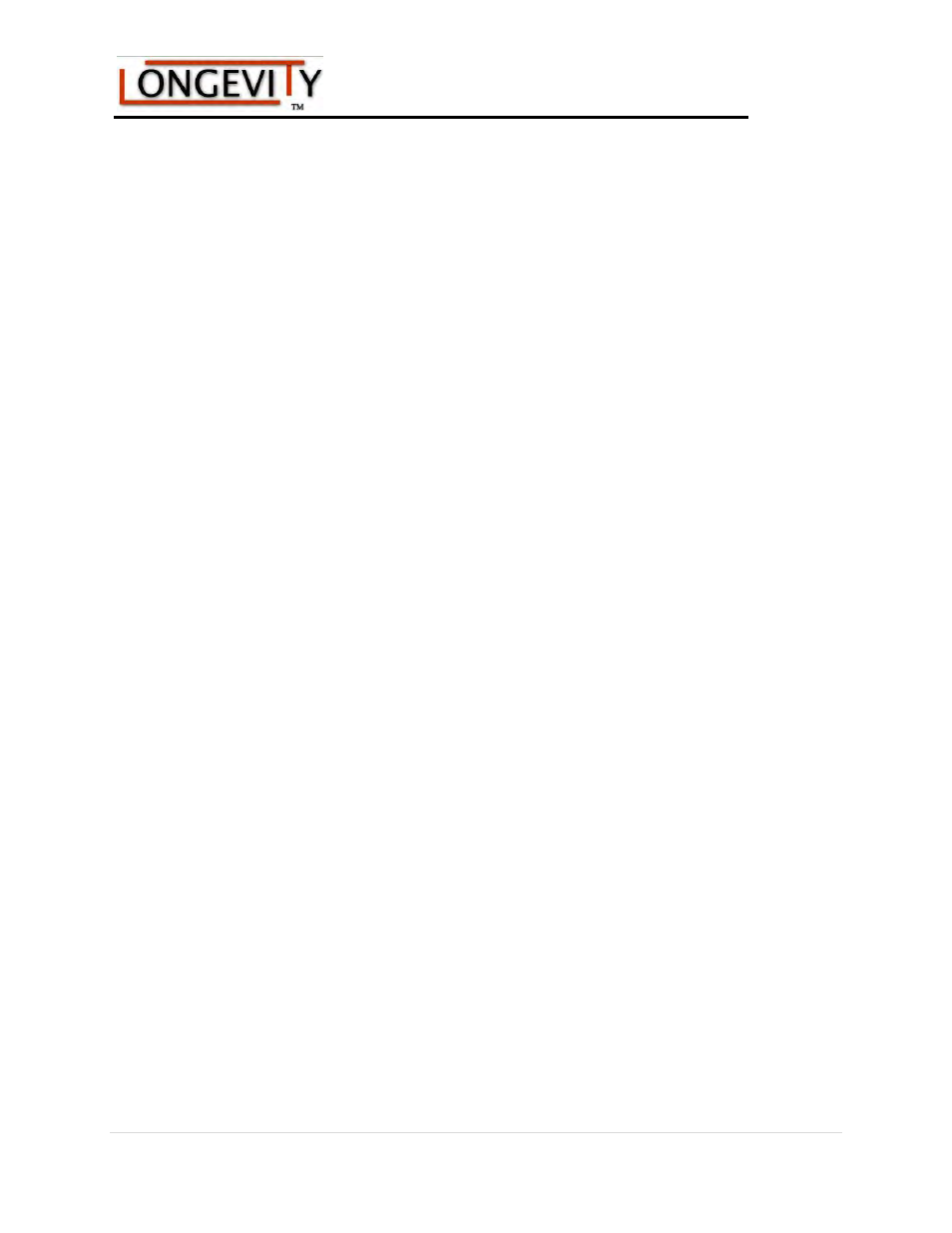
160/205 MIG Welder/ARC Welder
Page 30 of 37
www.longevity-inc.com
of shielding gas used—with pure inert gas’s, the bottom of the torch is often slightly in front of
the upper section, while the opposite is true when the welding atmosphere is carbon dioxide.
Quality
Two of the most prevalent quality problems in GMAW are dross and porosity. If not controlled,
they can lead to weaker, less ductile welds. Dross is an especially common problem in aluminum
GMAW welds, normally coming from particles of aluminum oxide or aluminum nitride present
in the electrode or base materials. Electrode and work piece must be brushed with a wire brush or
chemically treated to remove oxides on the surface. Any oxygen in contact with the weld pool,
whether from the atmosphere or the shielding gas, causes dross as well. As a result, sufficient
flow of inert shielding gases is necessary, and welding in volatile air should be avoided.
In GMAW the primary cause of porosity is gas entrapment in the weld pool, which occurs when
the metal solidifies before the gas escapes. The gas can come from impurities in the shielding gas
or on the work piece, as well as from an excessively long or violent arc. Generally, the amount of
gas entrapped is directly related to the cooling rate of the weld pool. Because of its higher
thermal conductivity, aluminum welds are especially susceptible to greater cooling rates and thus
additional porosity. To reduce it, the work piece and electrode should be clean, the welding
speed diminished and the current set high enough to provide sufficient heat input and stable
metal transfer but low enough that the arc remains steady. Preheating can also help reduce the
cooling rate in some cases by reducing the temperature gradient between the weld area and the
base material.