Longevity ARCMATE 205 User Manual
Page 27
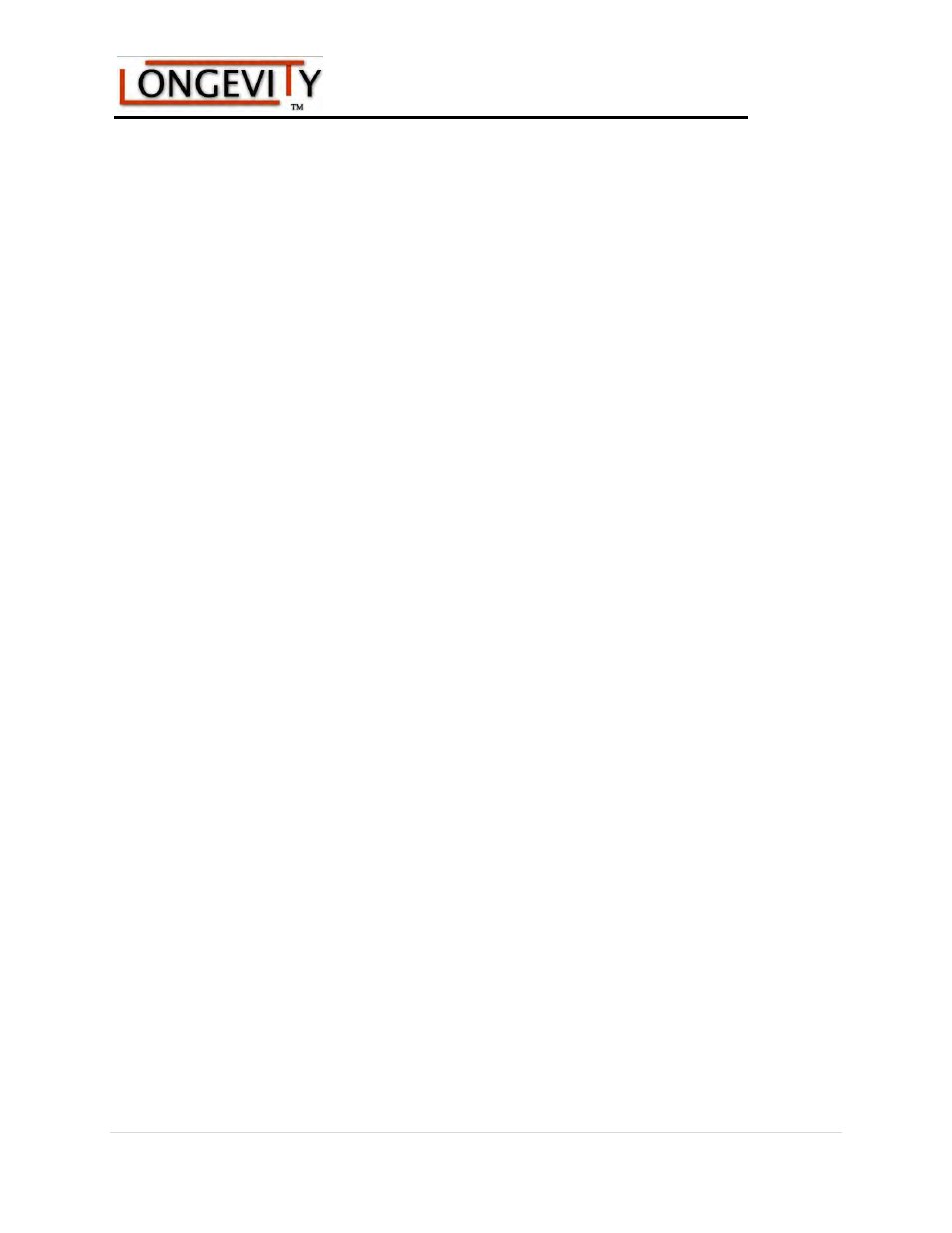
160/205 MIG Welder/ARC Welder
Page 26 of 37
www.longevity-inc.com
The wire feed unit supplies the electrode to the work, driving it through the conduit and on to the
contact tip. Most models provide the wire at a constant feed rate, but more advanced machines
can vary the feed rate in response to the arc length and voltage. Some wire feeders can reach feed
rates as high as 30.5 m/min (1200 in/min), but feed rates for semiautomatic GMAW typically
range from 2 to 10 m/min (75–400 in/min).
Tool Style
The top electrode holder is a semiautomatic air-cooled holder; compressed air is circulated
through it to maintain moderate temperatures. It is used with lower current levels for welding
lap- or butt joints. The second most common type of electrode holder is a semiautomatic water-
cooled; the only difference being that water takes the place of air. It uses higher current levels for
welding T- or corner joints. The third typical holder type is an automatic electrode holder that is
water cooled; this holder is used typically with automated equipment.
Power supply
Most applications of gas metal arc welding use a constant voltage power supply. As a result, any
change in arc length (which is directly related to voltage) results in a large change in heat input
and current. A shorter arc length will cause a much greater heat input, which will make the wire
electrode melt more quickly and thereby restore the original arc length. This helps operators keep
the arc length consistent even when manually welding with hand-held welding guns. To achieve
a similar effect, sometimes a constant current power source is used in combination with an arc
voltage-controlled wire feed unit. In this case, a change in arc length makes the wire feed rate
adjust in order to maintain a relatively constant arc length. In rare circumstances, a constant
current power source and a constant wire feed rate unit might be coupled, especially for the
welding of metals with high thermal conductivities, such as aluminum. This grants the operator
additional control over the heat input into the weld, but requires significant skill to perform
successfully.
Alternating current is rarely used with GMAW; instead, direct current is employed and the
electrode is generally positively charged. Since the anode tends to have a greater heat
concentration, this will result in faster melting of the feed wire, which increases weld penetration
and welding speed. The polarity can be reversed only when special emissive-coated electrode
wires are used, but since these are not popular, a negatively charged electrode is rarely
employed.
Electrode
Electrode selection is based primarily on the composition of the metal being welded, the process
variation being used, joint design and the material surface conditions. Electrode selection greatly
influences the mechanical properties of the weld and is a key factor of weld quality. In general
the finished weld metal should have mechanical properties similar to those of the base material
with no defects such as discontinuities, entrained contaminants or porosity within the weld. To
achieve these goals a wide variety of electrodes exist. All commercially available electrodes