Zone separation, Zone 1 – JUMO 902820 PROCESStemp RTD Temperature Probe for Process Technology (Also with ATEX Approval) Ex i Operating Manual User Manual
Page 9
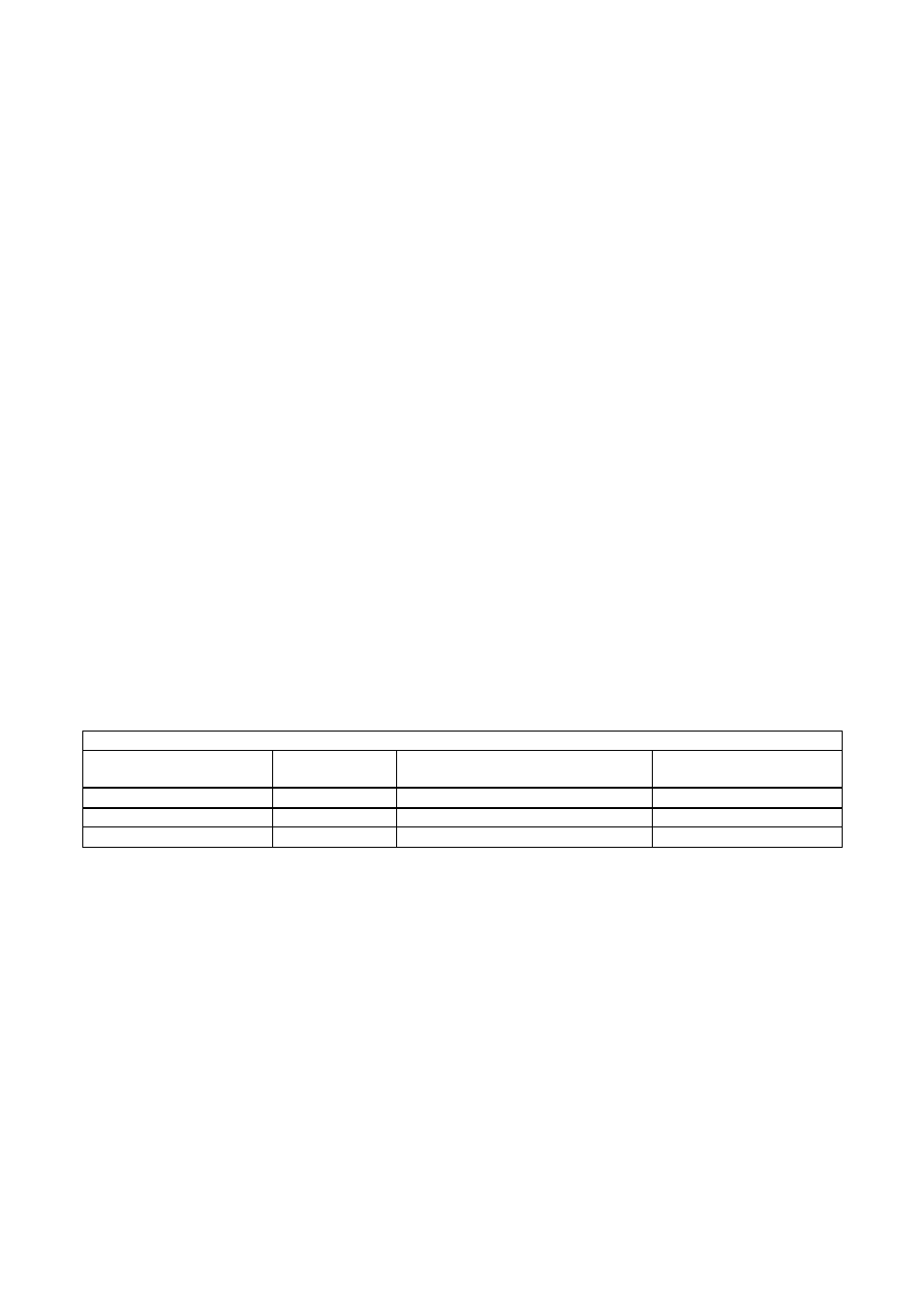
- 8 -
6 Installation
The valid European and national regulations must be observed for installation and operation. The generally
accepted state of the art and these operating instructions must be applied.
RTD temperature probes from JUMO are used to measure temperature within areas with an explosion
hazard, containing flammable or non-flammable materials, gases, air-gas mixtures or potentially explosive
dusts. In the case of equipment with type Ex "i" protection, the supply of power and evaluation are performed
by certified intrinsically safe circuits.
The RTD temperature probes are mounted by means of the process connection on site. The RTD
temperature probe may need to be built into an additional screw-in or weld-in pocket, depending on the
process connection. If a thread is provided as a process connection, then the entire thread length of the RTD
temperature probe must be in contact.
The feed wire of the RTD temperature probe must be fixed in position when mounted to containers or
pipelines that contain potentially explosive gas/air mixtures (zone 0, 1G or EPL Ga) or dust (zone 20, 1D or
EPL Da).
Metallic connector housings must be grounded via the connecting cables, for equipotential bonding.
Non-metallic connector housings must not exceed the max. surface area specified by EN 50284 (4.4).
The screw-in or weld-in pocket can also serve to separate zones, and is made from steel, stainless steel,
Hastelloy, etc. with a minimum wall thickness of 1 mm.
Norm EN 60079-14 "Explosive atmospheres - Part 14: Electrical installations design, selection and erection"
needs to be observed!
Equipment for potentially explosive areas which contain hybrid mixtures has to be especially checked for this
use. Hybrid mixtures are potentially explosive mixtures out of combustible gases, vapors, or mists with
combustible dust. The operator bears the responsibility of checking if the equipment is suitable for such
uses.
Caution:
In all cases, zoning is the responsibility of the plant/system operator, and not of the
manufacturer/supplier of the equipment!
Zone separation
Gases, mists, vapors
Dusts
Potentially explosive
atmosphere present
Guide values
Zone 0
Zone 20
continually, long-term, or frequently
1000 hours/year
Zone 1
Zone 21
occasionally
10 to 1000 hours/year
Zone 2
Zone 22
infrequently, short-term
10 hours/year
Table 3: Zone separation
7 Maintenance
The valid European and national regulations must be observed for maintenance, servicing and testing.
During maintenance, all parts must be tested that are relevant for the Ex (explosion protection) rating.
In addition, thermometers with a plastic terminal head as well as all plastic components (e.g.
connectors and the like) must only be cleaned with a damp cloth, to avoid building up an
electrostatic charge.