Bryant 502A User Manual
Page 4
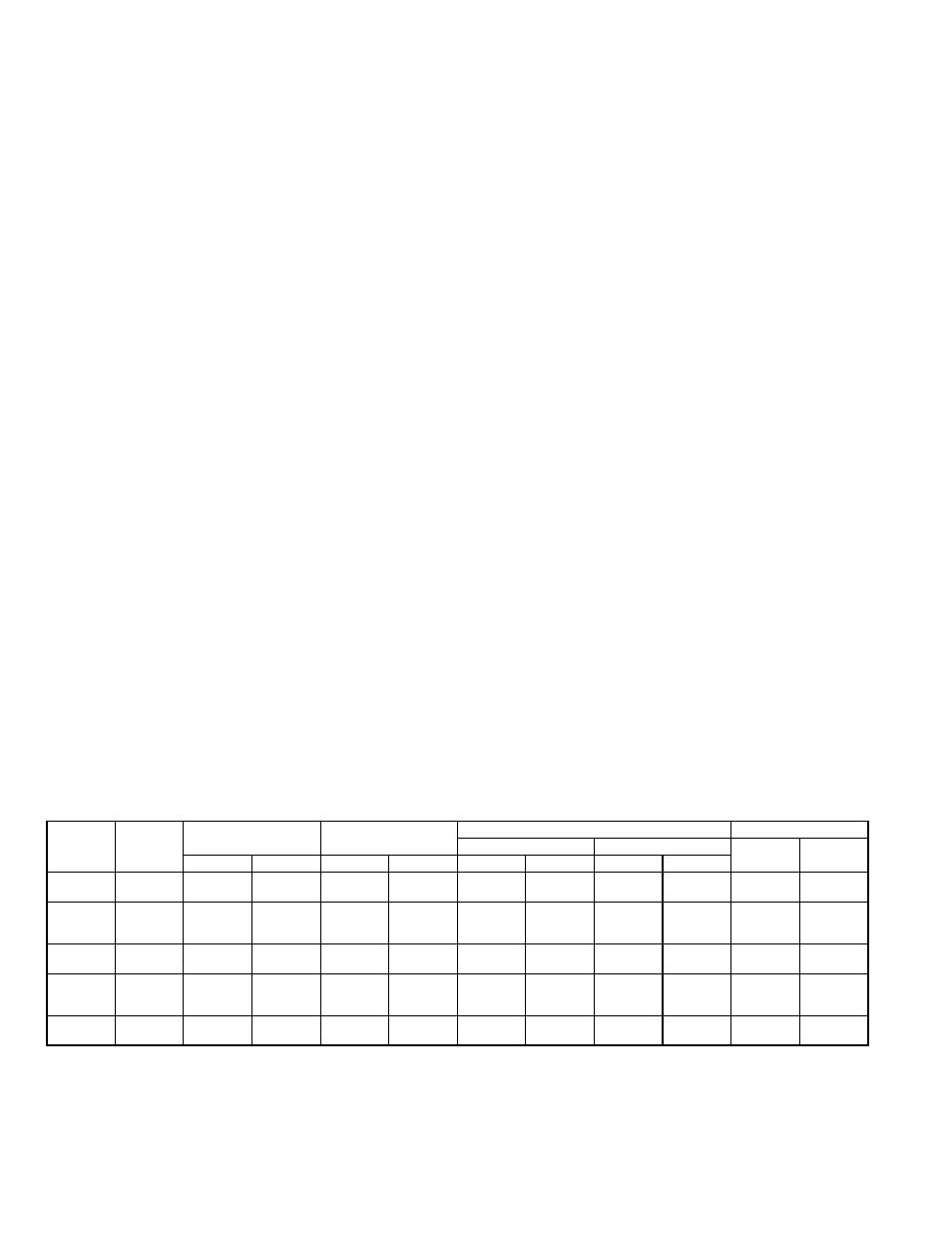
—
4
—
IV. STEP 4 — RIG AND PLACE UNIT
Move and store unit in horizontal position. Provide space
around unit for service, filter access, ductwork, and overhead
clearance as indicated in Fig. 1.
Using suitable hydraulic lift source, raise unit up to meet
bottom of the 4 threaded rods suspended from ceiling. Center
unit so that the 4 threaded rods can be easily inserted into
the factory-drilled holes at each end. Refer to Fig. 3 for rig-
ging details.
Apply washers and locknuts on ends of each of the 4 rods.
Tighten locknuts sufficiently so that unit weight is sup-
ported entirely by the 4 rods. Level unit within the space by
adjusting locknuts.
IMPORTANT: Unit must be level to operate properly.
NOTE: The 2 factory-drilled holes in the middle of the unit
can be used for support if a split system application is
desired. If required, a vibration isolator package accessory is
available for use to minimize vibration that may be trans-
mitted to building structure.
NOTE: For split systems, 8 suspension rods are required.
Refer to Splitting Systems section.
V. STEP 5 — MAKE PIPING CONNECTIONS
Two
3
/
4
-in. pipe thread condensate drain connections are pro-
vided below the evaporator coil. One
3
/
4
-in. pipe thread con-
nection is provided for condenser coil washdown. One of the
evaporator drains is plugged at the factory; plug must be
removed when making field connections. The condenser
washdown pan is plugged at the factory. This drain is to be
used only when condenser coil is being cleaned; plug must be
replaced when cleaning is completed.
VI. STEP 6 — INSTALL DUCTWORK
Use flexible ductwork to attach duct to unit and to help con-
trol transmission of vibrations to building structures. Attach
ductwork to the return and supply ends of both coils.
If unit is located with condenser close to outside of building,
install a field-supplied rainhood. Hood intake dimensions
should be same as condenser return-air dimensions. In addi-
tion, install a triple-layer bird screen over rainhood intake to
eliminate possibility of insects, birds, water, or debris from
entering unit. Ensure hood and/or louvers are installed cor-
rectly to avoid condenser air recirculation.
VII. STEP 7 — MAKE ELECTRICAL CONNECTIONS
Provide and install a safety disconnect switch in accordance
with National Electric Code (NEC) and all local codes.
Connect power wiring to junction box located on unit side
near control box access panel. All wiring must comply
with NEC and all local code requirements.
Operating voltage to compressor must be within voltage
range as indicated on unit nameplate. Voltages between
phases must be balanced within 2% and current must be
balanced within 10%. Contact local power company for
correction of improper voltage or phase imbalance. Unit
failure as a result of operation on improper line voltage or
excessive phase imbalance constitutes abuse and may cause
damage to electrical components. Such operation would
invalidate any applicable Bryant warranty.
Refer to unit nameplate and Table 2 for fuse sizes and wire
amperages for all units.
VIII. SPLITTING SYSTEMS
The 502A roomtop units may be split into 2 sections, if
desired, with condensing section mounted remotely either
horizontally or vertically. If sections are installed in same
horizontal plane they may be separated by up to 50 equiva-
lent ft of tubing. Use type L copper or better.
Condensing section must be located in same plane as, or
above, evaporator section to maintain the liquid refrigerant
seal at the expansion device. This permits expansion device
to feed liquid refrigerant to evaporator coil properly. To split
sections (some of the following steps may be eliminated
depending on particular application):
1. Disconnect all electrical power to unit and tag
disconnect.
2. Remove 4 bolts connecting the 2 sections.
3. Remove top panels from each section.
4. Recover the refrigerant from the system using both
the high and low-pressure ports.
5. Cut refrigerant piping in the evaporator section just
inside the partition between the 2 sections.
Table 2 — Electrical Data
LEGEND
*Optional evaporator-fan motor nameplate data.
UNIT
502A
V-PH
(60 Hz)
VOLTAGE RANGE
COMPRESSOR
FAN MOTORS
POWER SUPPLY
Evaporator
Condenser
Min Ckt
Amps
MOCP
Amps
Min
Max
RLA
LRA
Hp
FLA
Hp
FLA
036
208/230-3
187
254
10.2
77.0
.50
3.20
.75
3.93
19.9
25
460-3
414
508
4.3
37.0
.50
1.50
.75
1.97
8.8
15
048
208/230-3
187
254
13.5
99.0
.75
4.00
1.0
3.93
24.8
35
460-3
414
508
7.4
49.5
.75
2.15
1.0
1.97
13.4
15
575-3
518
632
5.8
40.0
.75
1.40
1.0
1.45
10.1
15
048*
208/230-3
187
254
13.5
99.0
1.5
5.60
1.0
3.93
26.4
35
460-3
414
508
7.4
49.5
1.5
2.80
1.0
1.97
14.0
20
060
208/230-3
187
254
17.3
123.0
.75
4.00
1.5
4.82
30.4
45
460-3
414
508
9.0
62.0
.75
2.15
1.5
2.41
15.8
25
575-3
518
632
7.1
50.0
.75
1.40
1.5
1.90
12.2
20
060*
208/230-3
187
254
17.3
123.0
1.5
5.60
1.5
4.82
32.0
40
460-3
414
508
9.0
62.0
1.5
2.80
1.5
2.41
16.5
25
HACR — Heating, Air Conditioning, and Refrigeration
Hp
— Horsepower
FLA
— Full Load Amps
LRA
— Locked Rotor Amps
MOCP — Maximum Overcurrent Protection (HACR breaker)
RLA
— Rated Load Amps