Bryant Air Cooled Condensing Units 569C User Manual
Page 9
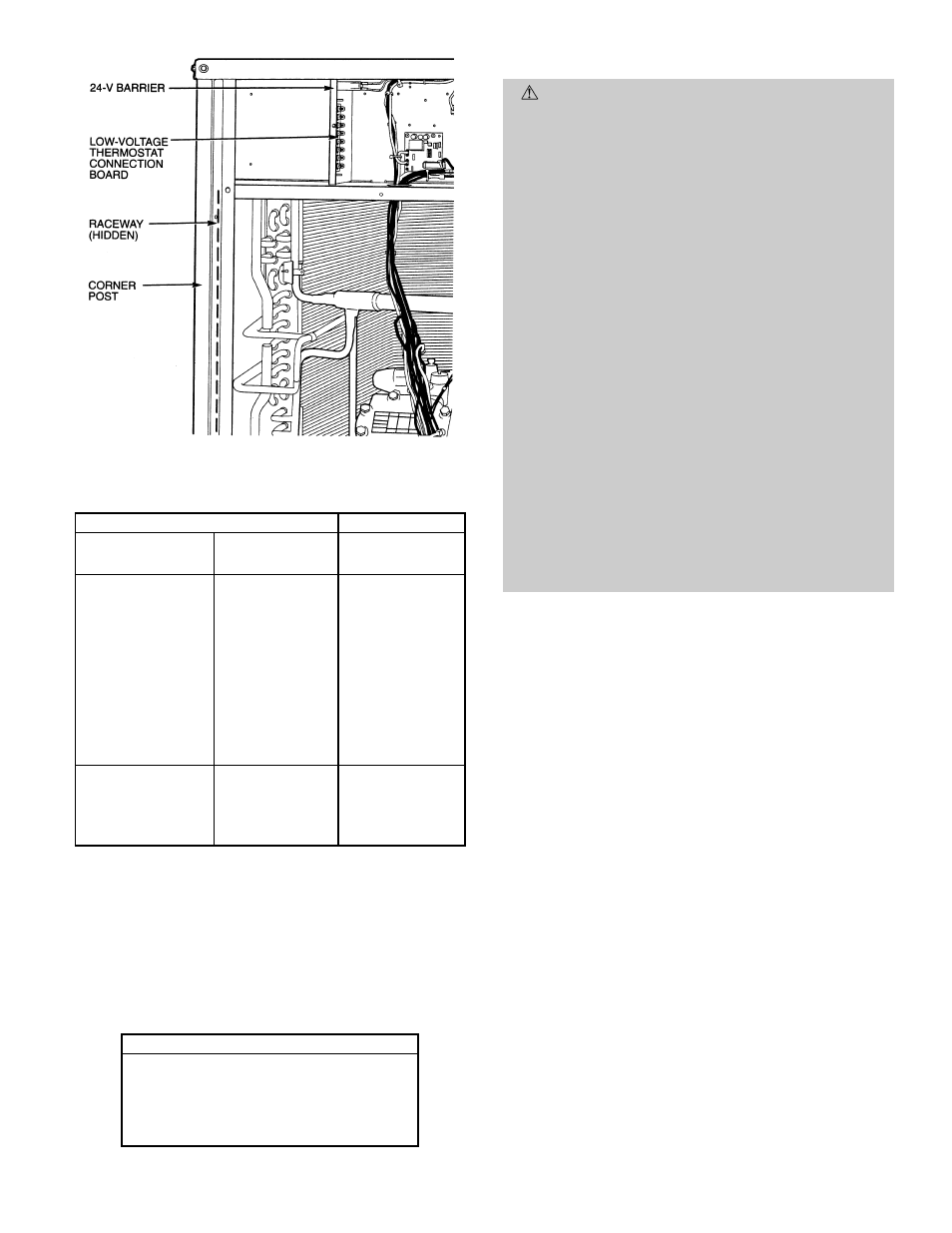
Table 5 — American/European Wire Conversions
AMERICAN
EUROPEAN
Industry
Standard Size
American
Conversion
(mm
2
)
Industry
Standard
Size (mm
2
)
18 AWG
0.82
1.0
16 AWG
1.30
1.5
14 AWG
2.08
2.5
12 AWG
3.30
4.0
10 AWG
5.25
6.0
8 AWG
6.36
10.0
6 AWG
13.29
16.0
4 AWG
21.14
25.0
3 AWG
26.65
—
2 AWG
33.61
35.0
1 AWG
42.39
50.0
1/0 AWG
53.49
—
2/0 AWG
67.42
70.0
3/0 AWG
85.00
95.0
4/0 AWG
107.19
120.0
250 kcmil
126.64
150.0
300 kcmil
151.97
—
350 kcmil
177.90
185.0
400 kcmil
202.63
240.0
500 kcmil
253.29
300.0
600 kcmil
303.95
—
LEGEND
AWG — American Wire Gage
kcmil — Thousand Circular Mils
VI. ACCESSORY INSTALLATION
At this time any required accessories should be installed on
the unit. Refer to Table 6 for available accessories. Control
wiring information is provided in the unit wiring book.
Table 6 — Accessory List
ACCESSORY
Gage Panel
Winter-Start Relay Package
Weatherprobe™ II Low Ambient Kit
Hail Guard Package (072)
Hail Guard Package (090,102,120)
Thermostats
Subbase
PRE-START-UP
WARNING:
Failure to observe the following warn-
ings could result in serious personal injury:
1. Follow recognized safety practices and wear pro-
tective goggles when checking or servicing refrig-
erant system.
2. Do not operate compressor or provide any electric
power to unit unless compressor terminal cover is
in place and secured.
3. Do not remove compressor terminal cover until all
electrical sources have been disconnected.
4. If refrigerant leak is suspected around compres-
sor terminals, recover refrigerant whenever pos-
sible and relieve all pressure from system before
touching or disturbing anything inside terminal box.
5. Never attempt to repair soldered connection while
refrigerant system is under pressure.
6. Do not use torch to remove any component. Sys-
tem contains oil and refrigerant under pressure.
To remove a component, wear protective goggles
and proceed as follows:
a. Shut off electrical power to unit.
b. Recover refrigerant. Relieve all pressure from
system.
c. Cut component-connecting tubing with tubing
cutter and remove component from unit.
d. Carefully unsweat remaining tubing stubs when
necessary. Oil can ignite when exposed to torch
flame.
Proceed as follows to inspect and prepare the unit for initial
start-up:
1. Field electrical power source must agree with unit name-
plate rating.
2. Check voltage imbalance as shown in Table 4, Note 2.
3. Check that all internal wiring connections are tight and
that all barriers, covers, and panels are in place.
4. Ensure all service valves are open. On 576B units, be
sure all compressor service valves are backseated.
5. Verify that compressor holddown bolts have been loos-
ened and that flat/snubber washers can be rotated by
applying finger pressure (snug, but not tight).
6. On 569C and 576B units, verify compressor crankcase
heater is securely in place. Crankcase heater must op-
erate for a least 24 hours before start-up.
7. Note that compressor oil level is visible in the sight
glass (576B units only).
8. Check for leaks in refrigerant system by using soap
bubbles and/or electronic leak detector.
9. Check that liquid line solenoid valve is located at evapo-
rator coil as shown in Filter Drier and Moisture Indi-
cator section, page 6.
10. Check that both outdoor and indoor units are properly
mounted in accordance with installation instructions
and applicable codes.
Fig. 8 — Field Control Wiring Raceway
(576B Unit Shown)
—9—