Bell & Gossett AC8584D Series HSCS Base Mounted Centrifugal Pumps User Manual
Page 16
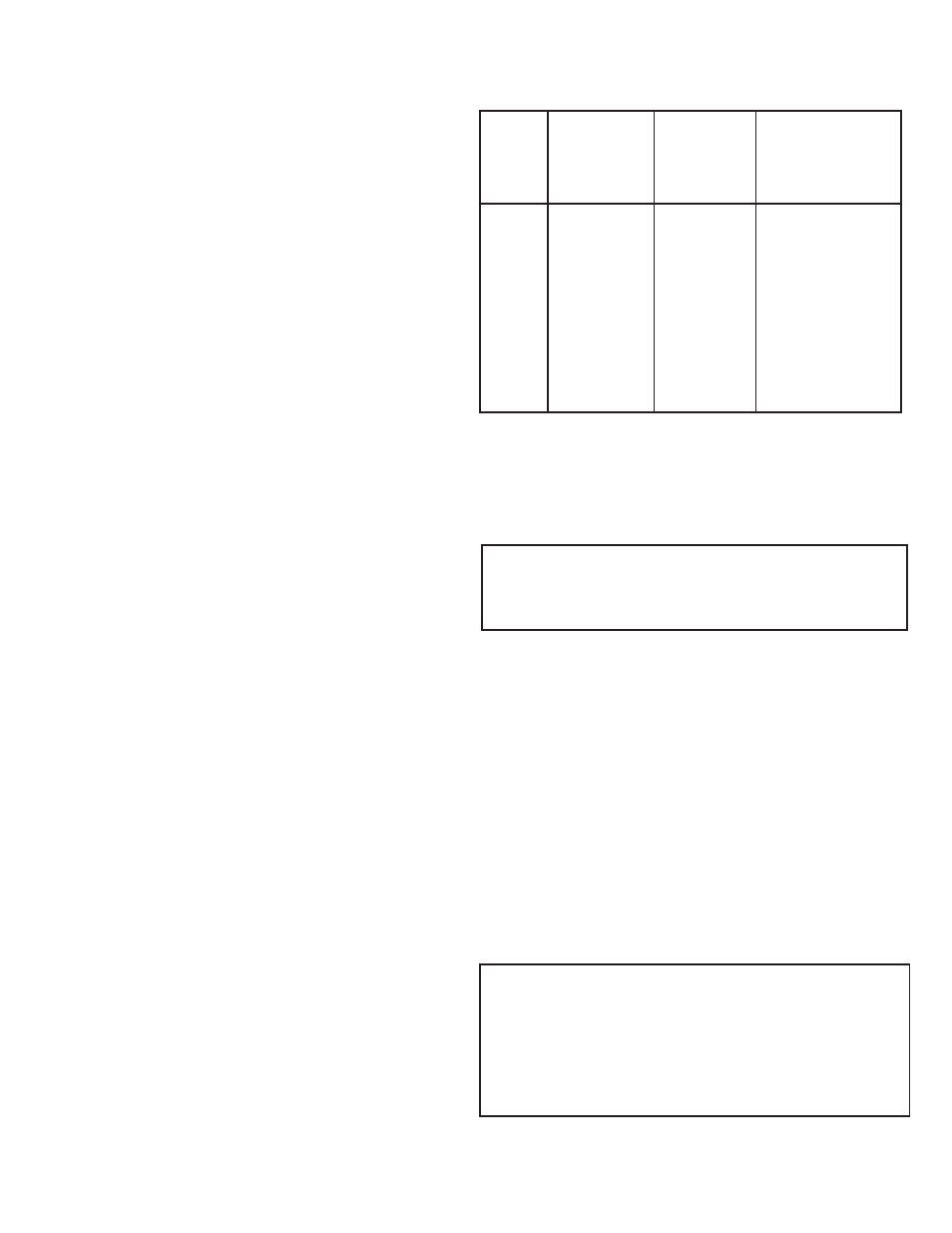
16
Regrease the grease-lubricated bearings
It is important to lubricate pumps and motors that require regreasing
with the proper grease. See the motor service instructions and
nameplate for motor regreasing information. Pumps are to be
regreased using the grease types listed below or approved equal.
Always keep pump and motor properly lubricated.
NOTICE:
Make sure the grease container, the greasing device, and the
fittings are clean. Failure to do so can result in impurities entering
the bearing housing when you regrease the bearings.
1. With fully enclosed coupling guards, regrease pump while pump
is running.
a. With old style open ended guards, stop pump, re-grease,
and hand turn shaft before re-starting.
2. Wipe dirt from the grease fittings before greasing.
3. Fill both of the grease cavities through the fittings with the
recommended grease. Stop when grease leaks out at shaft.
4. If needed, stop pump and wipe off excess grease.
5. Restart pump.
The bearing temperature usually rises after you regrease due
to excess supply of grease. Temperatures return to normal in
about two to four operating hours as the pump runs and purges
the excess grease from the bearings. Maximum normal bearing
housing temperature for polyurea-based grease is 225°F (107°F)
and for lithium-based grease 180°F (82°C).
Lubricating grease requirements
NOTICE:
• Never mix grease of different consistencies (NLGI 1 or 3 with
NLGI 2) or with different thickeners. For example, never mix
lithium-based grease with a polyurea-based grease. This can
result in decreased performance.
• Remove the bearings and old grease if you need to change
the grease type or consistency. Failure to do so can result in
equipment damage or decreased performance.
Type of
bearing
First lubrication,
assembled
pumps and
replacement
bearing frames
First
lubrication,
replacement
bearings
Lubrication interval,
pump, polyurea-based
grease, operating hours
Grease-
lubricated
bearings
Not applicable,
lubricated before
shipment
Hand pack
bearings before
pressing on
the shaft. After
bearing frame
assembly,
follow relube
instructions to
lube bearings.
• 3600 hours, 2 pole
• 7200 hours, 4 pole
• 50% for severe
conditions: dirty, wet
and/or above 100°F
(38°C) ambient
• 50% for bearing frame
temperature above
180°F (82°C)
• 75% for lithium-based
grease
BEARING MAINTENANCE
3. Bearing lubrication schedule
MAINTENANCE
1. General Maintenance
Operating conditions vary so widely that to recommend one
schedule of preventative maintenance for all centrifugal
pumps is not possible. Yet some sort of regular inspection
must be planned and followed. We suggest a permanent
record be kept of the periodic inspections and maintenance
performed on your pump. This recognition of maintenance
procedure will keep your pump in good working condition,
and prevent costly breakdown.
One of the best rules to follow in the proper maintenance of
your centrifugal pump is to keep a record of actual operating
hours. Then, after a predetermined period of operation has
elapsed, the pump should be given a thorough inspection.
The length of this operating period will vary with different
applications,and can only be determined from experience.
New equipment, however, should be examined after a relatively
short period of operation. The next inspection period can
be lengthened somewhat. This system can be followed until
a maximum period of operation is reached which shouldbe
consideredthe operating schedule between inspections.
2. Maintenance of Pump Due to Flood Damage
The servicing of centrifugal pumps after a flooded condition is
a comparatively simple matter under normal conditions.
Bearings are a primary concern on pumping units. First, dismantle
the bearings; clean and inspect them for any rusted or badly worn
surfaces. If bearings are free from rust and wear, reassemble and
relubricate them with one of the recommended pump lubricants.
Depending on the length of time the pump has remained in the
flooded area, it is unlikely that bearing replacement is necessary;
however, in the event that rust or worn surfaces appear, it may be
necessary to replace the bearings.
Next, inspect the stuffing box, and clean out any foreign matter
that might clog the box. Mechanical seals should be cleaned and
thoroughly flushed.
Couplings should be dismantled and thoroughly cleaned.
Any pump that is properly sealed at all joints and connected to
both the suction and discharge should exclude outside liquid.
Therefore, it should not be necessary to go beyond the bearings,
stuffing box, and coupling when servicing the pump.