Maintenance – Blodgett KLS-E Series User Manual
Page 13
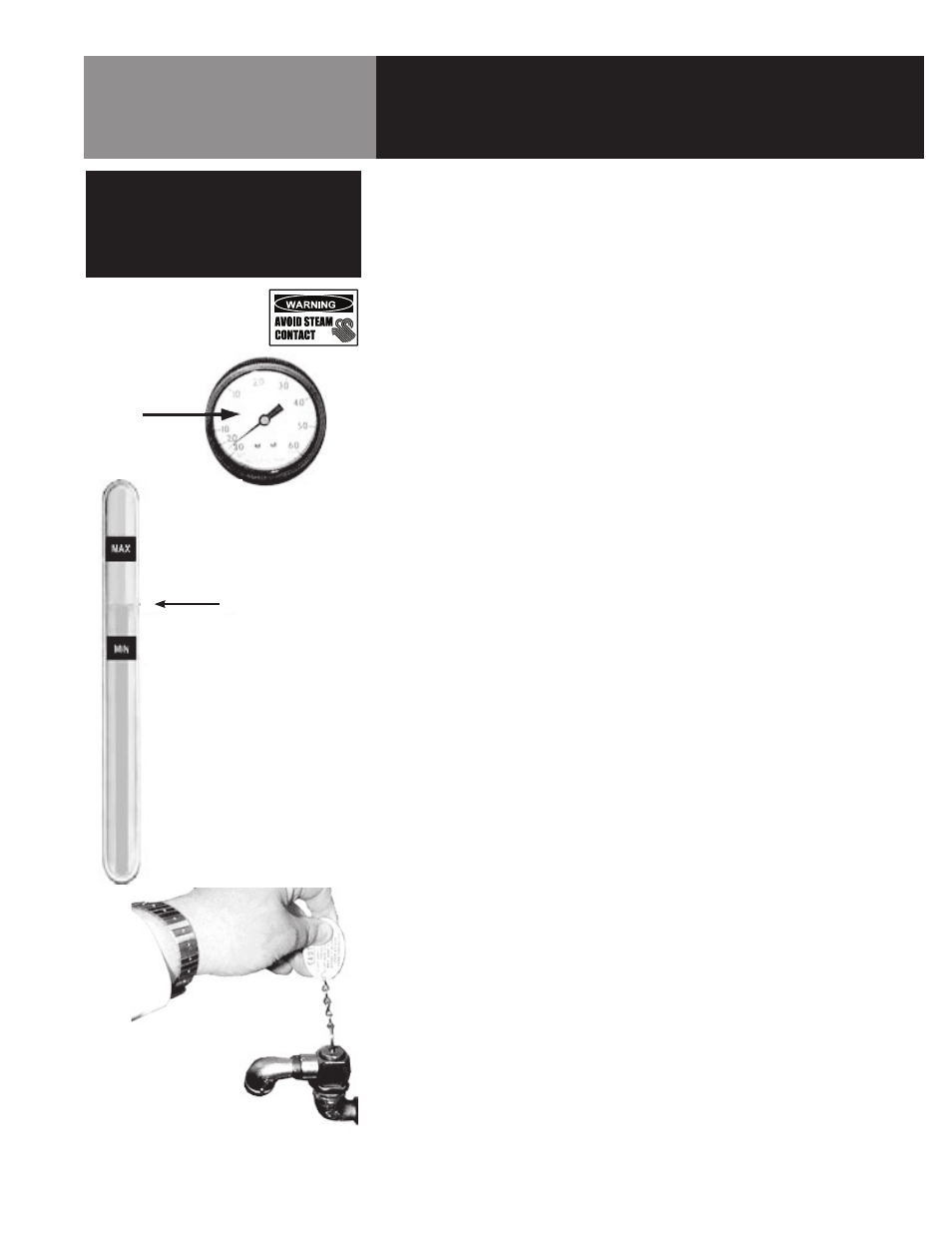
OM-KLS-E 11
Maintenance
NOTICE: Contact an authorized representative when repairs are required.
A.
Periodic Maintenance
A Maintenance and Service Log is provided at the back of this manual with the
warranty information. Each time maintenance is performed on your kettle, enter
the date on which the work was done, what was done, and who did it. Keep this
manual on file and available for operators to use.
Periodic inspection will minimize equipment down time and increase the
efficiency of operation. The following points should be checked:
1.
Check the pressure/vacuum gauge every day. The gauge should show
a vacuum of 20 to 30 inches, when the kettle is cold. If it does not, see
“Jacket Vacuum” below.
2.
Also check the jacket water level every day. It should be between the
marks on the gauge glass. If the level is low, see “Jacket Filling and
Water Treatment”.
3.
Test the safety valve at least twice each month. Test the valve with the
kettle operating at 15 psi (105 kPa), by pulling up the test valve chain
for at least 5 seconds. Then release the lever and let the valve snap
shut. If the valve does not activate, or there is no evidence of discharge,
or the valve leaks, stop using the kettle and contact a qualified service
representative.
B.
Jacket Vacuum
When the kettle is cold, a positive pressure/vacuum gauge reading or a reading near
zero indicates that there is air in the jacket. Air in the jacket slows kettle heating.
To remove air:
1.
Start the unit. (Be sure there is water or product in the kettle when heating.)
2.
Make sure that the elbow of the safety valve outlet is turned so that escaping
steam is directed toward the floor.
3.
When the pressure/vacuum gauge reaches a positive pressure reading of 5
psi, release the trapped air and steam by pulling up or out on the safety valve
lever or ring for about 1 second. Repeat this step, then let the pull ring or
valve lever snap back into the closed position.
C.
Jacket Filling and Water Treatment
The jacket was charged at the factory with the proper amount of treated water. You
may need to restore this water because it was lost as steam during venting or by
draining.
1.
If you are replacing water lost as steam, use distilled water. If you are
replacing treated water that ran out of the jacket, prepare more treated water
as directed in step 6, “Water Treatment Procedure.” Do not use tap water.
WARNING
WHEN TESTING, AVOID ANY EXPOSURE
TO THE STEAM BLOWING OUT OF THE
SAFETY VALVE. DIRECT CONTACT
COULD RESULT IN SEVERE BURNS.
PRESSURE
20 - 30
BELOW
ZERO
WATER LEVEL
BETWEEN
LINES
Test the safety valve at least twice monthly.