Red Lion IFMR User Manual
Page 7
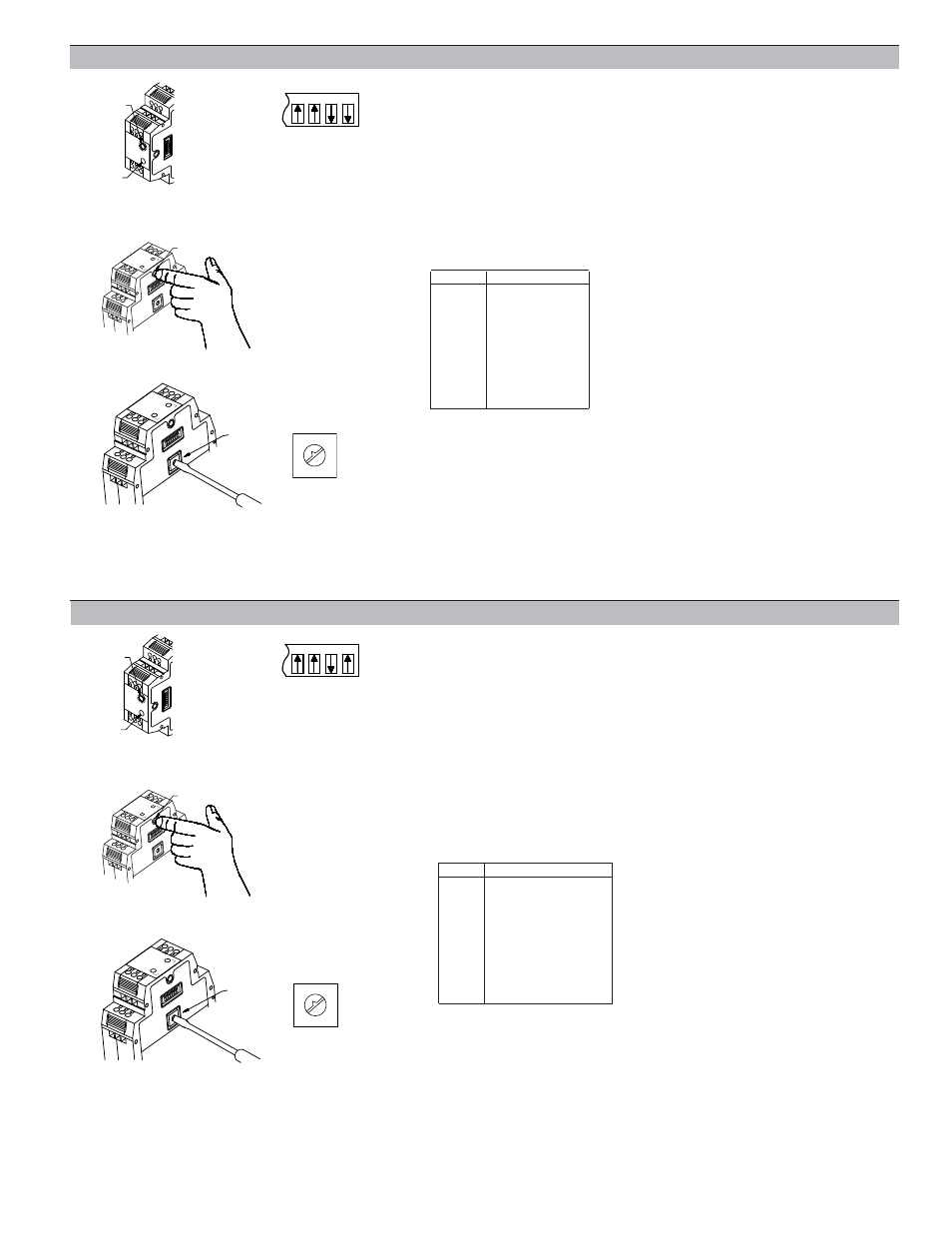
7
For Overspeed operation, the Relay Trip point is internally set to the Trip Frequency plus the
Offset value. For Underspeed operation, the Relay Trip point is internally set to the Trip Frequency
minus the Offset value. The Offset value is equal to the Trip Frequency multiplied by the selected
Offset percentage.
Example: The Offset value is calculated as shown below.
Trip Frequency
= 250 Hz
Rotary Switch Setting = 4 (2.00%)
Offset Value
= 250 Hz x 2.00% (0.02) = 5 Hz
Trip
Point:
OVERSPEED
= 250 + 5 = 255 Hz
UNDERSPEED
= 250 - 5 = 245 Hz
5.1 Place DIP switch 4 to the ON position and DIP switches 5, 6, and 7 as shown.
5.2 The Green input LED blinks the existing setting (see following list), pauses and repeats.
Setting Percentage
0
0.00% (NO Offset)
1 0.25%
(0.0025)
2 0.50%
(0.0050)
3 1.00%
(0.0100)
4 2.00%
(0.0200)
5 5.00%
(0.0500)
6 10.00%
(0.1000)
7 20.00%
(0.2000)
8 25.00%
(0.2500)
9 33.33%
(0.3333)
5.3 Press the push-button. The Green input LED blinks rapidly. Trip Point Offset setting is now
accessed.
5.4 Turn the rotary switch to the selected numerical value for Trip Point Offset desired (see list in
Step 5.2).
5.5 Press the push-button. The Green input LED blinks the value entered, pauses, and repeats the
new setting.
If the new Trip Point Offset setting is acceptable, this section is complete
*
.
If the new Trip Point Offset setting is not the desired setting, repeat Steps 5.3, 5.4, and 5.5.
If the Red relay LED blinks, the rotary switch numerical value is invalid. Repeat Steps 5.4
and 5.5.
*
Section complete; place DIP switch 4 to the down position for normal operation, or change DIP
switches 5, 6, and 7 for the next Configuration Section.
6.0 Set Relay Release Point (Hysteresis)
5.0 Set Relay Trip Point (Offset)
For Overspeed operation, the Relay Release point is set to the Relay Trip point minus the
Hysteresis value. For Underspeed operation, the Relay Release point is set to the Relay Trip point
plus the Hysteresis value. The hysteresis value is calculated by multiplying the hysteresis
percentage by the current trip frequency. If No Hysteresis (setting = 0) is selected, the Relay Trip
and Release points are identical, which can lead to chattering or cycling of the relay at input
frequencies hovering around the Relay Trip point.
Example: Using the Trip Frequency and Offset value as shown in the example above, the
hysteresis value is calculated as shown below.
Rotary Switch Setting = 3 (1.00%)
Hysteresis Value
= 250 Hz x 1.00% (0.01) = 2.5 Hz
Release
Point:
OVERSPEED
= 250 + 5 - 2.5 = 252.5 Hz
UNDERSPEED
= 250 - 5 + 2.5 = 247.5 Hz
6.1 Place DIP switch 4 to the ON position and DIP switches 5, 6, and 7 as shown.
6.2 The Green input LED blinks the existing setting (see following list), pauses, and repeats.
Setting Percentage
0
0.00% (NO Hysteresis)
1
0.25%
(0.0025)
2
0.50%
(0.0050)
3
1.00%
(0.0100)
4
2.00%
(0.0200)
5
5.00%
(0.0500)
6
10.00%
(0.1000)
7
20.00%
(0.2000)
8
25.00%
(0.2500)
9
33.33%
(0.3333)
6.3 Press the push-button. The Green input LED blinks rapidly. Trip Point Hysteresis setting is
now accessed.
6.4 Turn the rotary switch to the selected numerical value for Hysteresis desired (see list in Step 6.2).
6.5 Press the push-button. The Green input LED blinks the value entered, pauses and repeats the
new setting.
If the new Trip Point Hysteresis setting is acceptable, this section is complete
*
.
If the new Trip Point Hysteresis setting is not the desired setting, repeat Steps 6.3, 6.4, and 6.5.
If the Red relay LED blinks, the rotary switch numerical value is invalid. Repeat Steps 6.4
and 6.5.
*
Section complete; place DIP switch 4 to the down position for normal operation, or change DIP
switches 5, 6, and 7 for the next Configuration Section.
5
4
7
6
5
4
7
6
Step 5.2
Step 5.1
Step 6.2
Step 6.1
0
9
8
7 6 5 4
3
2
1
Setting ‘9’
Selected
0
9
8
7 6 5 4
3
2
1
Setting ‘9’
Selected
LED
LED
OUTPUT
RED
GREEN
INPUT
BLINKS
OFF
IN
OUT
LED
LED
OUTPUT
RED
GREEN
INPUT
BLINKS
OFF
IN
OUT
PUSH-BUTTON
OUT
IN
STATUS
Step 5.3
PUSH-BUTTON
OUT
IN
STATUS
Step 6.3
ROTARY
SWITCH
OUT
IN
STATUS
Step 5.4
ROTARY
SWITCH
OUT
IN
STATUS
Step 6.4