Kaman ThreadChecker User Manual
Page 10
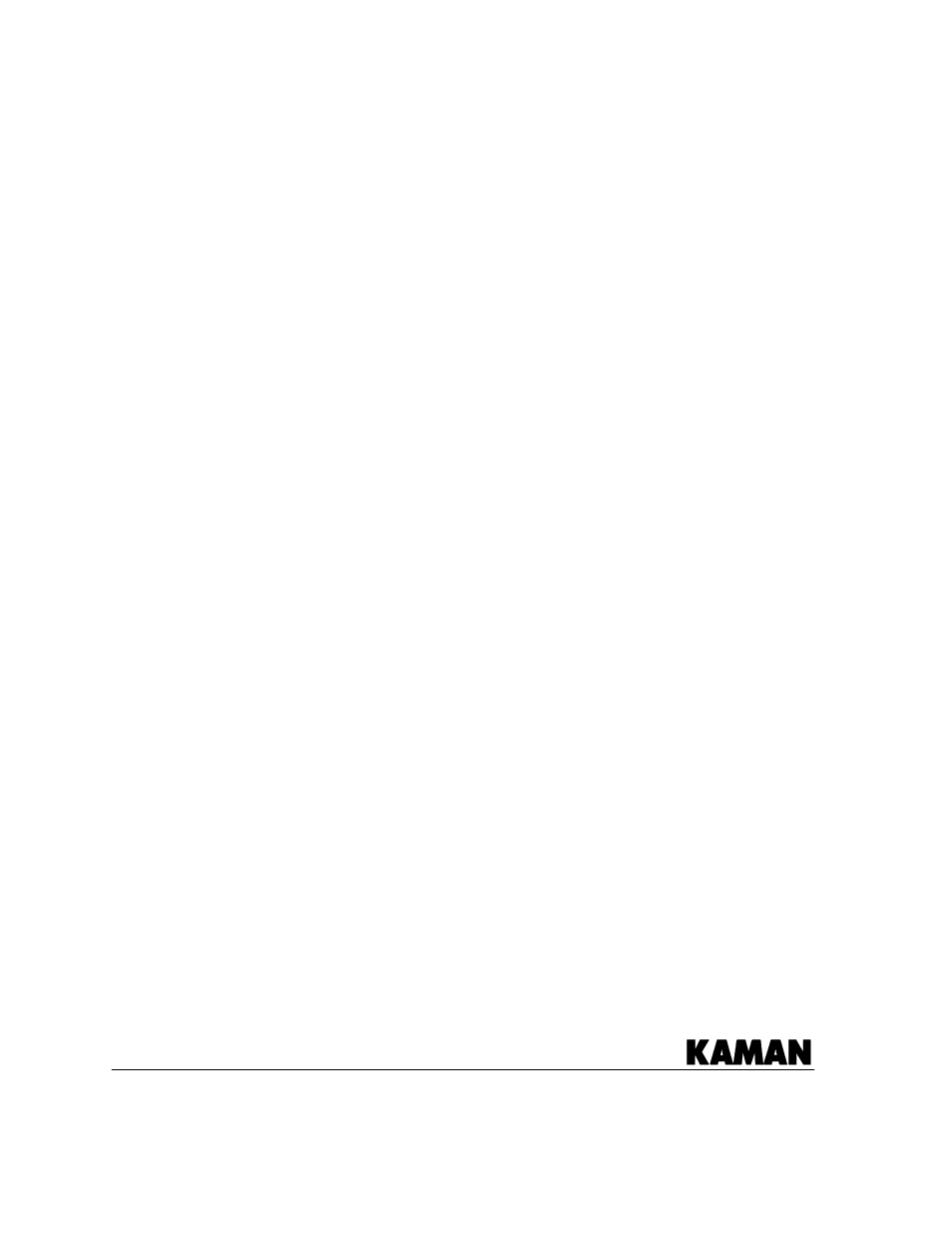
Copyright © 2008
Kaman Aerospace Corporation
PART NO: 860510-001A
Kaman Precision Products
Last Revised: 6/8/11
Measuring & Memory Systems
217 Smith Street
Middletown, CT 06457
www.kamansensors.com or 860-632-4442
Page 10 of 13
Troubleshooting
No LED’s are on.
- Check power input
- Make sure power input is correct polarity and connected to right wires
- If you can verifiy that the proper voltage is across the power input pins +15 to +30V
on the brown wire, the blue wire connected to ground, then contact the factory
Power LED is red all of the time.
- Make sure sensor is connected and is tight
- If sensor is connected, do a “teach” function. If after the teach the power LED is
solid red then the sensor is probably bad – contact the factory. If after the teach
the power LED is flashing red there may not be enough output from the sensor for
the holes or the sensor is bad.
Power LED is flashing red.
- Make sure power input is between +15 and +30VDC
- Make sure the ambient temperature around the electronics is <55C
- If it is red after you do a ‘teach’ it is likely there is not enough output difference
between the threaded and non-threaded holes. You may need a different sensor or
see the section on System not resolving thread/no-thread correctly.
- Make sure sensor connector is screwed on tight before a teach.
Status LED never goes to red when there is no threaded hole.
- Do a ‘teach’ to make sure that it has a good calibration
- It may be that the switch was held down during power up inadvertently – hold the
switch down on power up and release it when powered up to put it back into
Window comparator mode.
System not resolving thread/no-thread correctly
- The difference between a thread and a no thread condition usually produces a
large signal difference (approx 20% of the sensor range). There are cases though
where this may be a smaller percentage. A partially threaded hole may produce
1/10
th
the signal difference (resulting in just a 2% signal difference). In cases where
smaller differences in good/bad thread need to be detected there are a couple of
things that will help. First, when teaching the sensor use an example of the “bad
thread” (a partially threaded part). Next make sure to use as large a sensor as
possible. This results in better resolution. And finally minimize temperature changes
(even with the specified .05%/C temperature compensation a 20C change will
result in a 1% shift).
- Allow the system to warm up to operating temperature before calibrating. A full
warm up usually takes about 15 minutes but usually 5 minutes is adequate.
- Make sure the sensor connector is screwed on tight