Dwyer 295 User Manual
Page 9
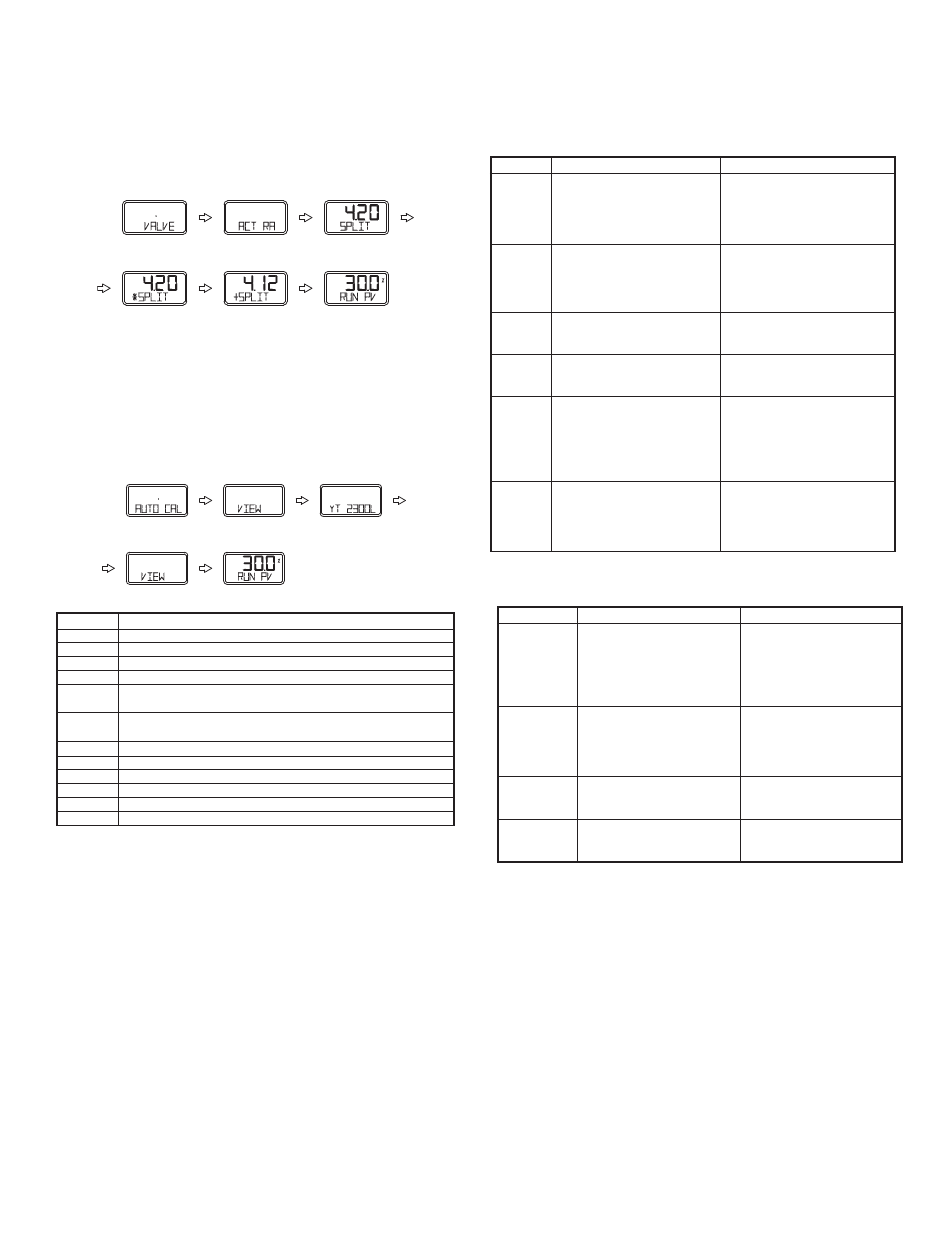
Adjustment of Split Range (SPLIT)
1. Push
2. Push
LCD are the range of current signal input to the positioner. 4 to 20 mA current signal
is set as the standard.
3. Push
adjusted. Adjust input signal range with
4. +SPLIT mode is displayed while saving adjusted range. Push
to return to RUN mode.
VIEW Mode
This mode provides users with various information about the Series 195 and 295
positioners. In this mode, users can change the valve stroke types displayed on the
LCD to % or numbers. Refer to the next table for information and description
displayed on VIEW mode.
1. Push
2. Push
3. Check information by using
4. Push
Error and Warning Code
If there are any problems during Series 195 and 295 positioner operation, you can
check the error and warning code at VIEW mode as follows:
Error Code
This code is displayed when the Series 195 and 295 positioner control becomes
impossible. Code C, D applies.
Warning Code
This code is displayed when the positioner control is available but there is a
possibility of malfunction or low accuracy. Code B, F, G, H applies.
YT-2500L
VERSION
HART V
POL AddR
bIAS VI
0Y 0d
FULL_OP
FULL_CL
VM NOR
Erro
VALUE I
ABS
Description
Positioner model
Main software version
HART Protocol version
Channel address that is used in HART Protocol
BIAS value for motor/piezo valve control. Can be adjusted only by
manufacturer.
Total used time duration. If a unit was used less than 1 minute, the
time does not accumulate.
Time elapsed for valve to fully open.
Time elapsed for valve to fully close.
Display type of valve stroke on LCD (either in percentage or value).
Display error code or warning message
Current I-Value. Can be adjusted only by manufacturer.
Display absolute resistance value.
Information Checked on VIEW Mode
Error Code
MT ERR L
MT ERR H
CHK AIR
RNG ERR
C
D
Code Description and Cause
Positioner is improperly installed.
Positioner lever is not parallel to
the ground at 50% point. Lever is
at lower position than actual 50%
point.
Positioner is improperly installed.
Positioner lever is not parallel to
the ground at 50% point. Lever is
at lower position than actual 50%
point.
Valve does not operate when
positioner receives “Full Open”
signal during auto calibration.
Operating angle is too small due
to improper mounting of
positioner.
Error 10% or above persists more
than 1 minute.
No valve movement.
Friction of valve is too large.
Setting pressure of actuator
changes.
I-Value reaches at maximum or
minimum limit point.
Friction of valve changes.
Setting pressure of actuator
changes.
Action
Re-install/mount the positioner.
Make sure the feedback lever
does not touch the stopper at both
0 and 100%.
Re-install/mount the positioner.
Make sure the feedback lever
does not touch the stopper at both
0 and 100%.
Check if supply pressure is stable
and appropriate.
Adjust bracket so the positioner
can be mounted closer to actuator.
Perform BAS calibration.
Check setting pressure of actuator
and set the pressure as
recommended.
Perform AUTO calibration.
Check setting pressure of actuator
and set the pressure as
recommended.
Warning Code
B
F
G
H
Code Description and Cause
PV end-PV zero range is below
500. The angle of feedback
lever is too small.
Time elapsed for either full-open
or full-close is less than 1
second.
The size of the actuator is
too small.
Pv zero is below 100.
The angle of feedback lever
is too large.
Pv end is over 4000.
The angle of feedback lever
is too large.
Action
Re-install/mount the positioner.
Make sure the feedback lever
does not touch the stopper at
both 0 and 100%.
After re-installation, perform
AUTO1 calibration.
Use variable orifice.
Replace actuator with larger
capacity.
Re-install/mount the positioner.
After re-installation, perform
AUTO1 calibration.
Re-install/mount the positioner.
After re-installation, perform
AUTO1 calibration.
Page 9
6 seconds
5 times
then
3 times
then
4 times
confirm the changes,
then
COMPLETED