Dwyer 295 User Manual
Page 6
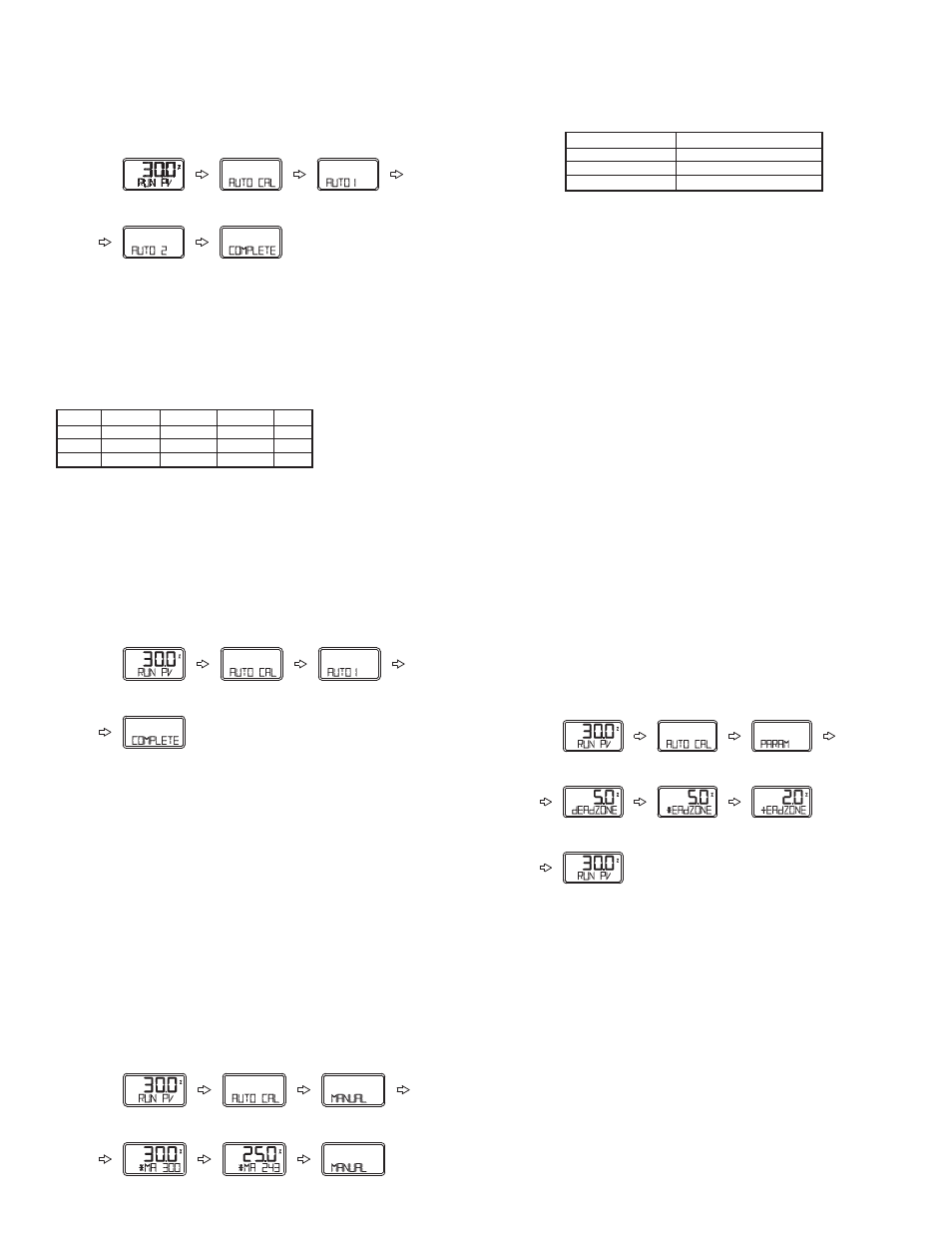
5. When Auto calibration is done, ‘COMPLETE’ message appears on the LCD. After
4 seconds the procedure is returned to RUN mode and valve stroke controlled by
the input signal will be displayed as a percentage.
6. Zero, Span, PID parameters and RA/DA are automatically set when Auto 2
calibration is completed.
Entire Modes and Functions
Auto Calibration (AUTO CAL)
The calibration of the Positioner is simply performed by Auto calibration. There are
3 types of Auto calibration: AUTO1, AUTO2 and AUTO3.
AUTO1 calibration is useful for users in the field. AUTO2 calibration is for valve
companies or the initial parameter setting for the positioner.
It takes about 2-3 minutes for Auto calibration and it can be different based on the
actuator's volume. AUTO2 and AUTO3 calibration set the RA/DA automatically.
Auto Calibration Types
Auto 1 Calibration (AUTO1)
In this mode, all parameters necessary for valve operation are set except KP, KI,
KD and RA/DA. AUTO1 is used to re-execute calibration in the field after being
installed.
1. Push
appear.
2. Push
3. Push
4. When Auto 1 calibration is done, ‘COMPLETE’ message appears on the LCD.
After 4 seconds the procedure returns to RUN mode and the valve stroke by current
input signal is displayed as a percentage.
Auto 2 Calibration (AUTO2)
All parameters necessary to operate the valve are set. This calibration is used
when the positioner is first installed with valve. Refer back to First Auto Calibration.
Auto 3 Calibration (AUTO3)
All parameters necessary to operate the valve are set except zero and end point.
This function is used to re-execute auto calibration without changing the zero and
end point after adjusting them manually.
1. Push
2. Push
this calibration are the same as other calibrations.
Manual Mode
Manual mode is used to raise or lower the valve stem manually. In this mode, valve
stroke is adjusted only by operating buttons, not by the current input signal. This
mode does not affect controlling data registered in the positioner. It only is used to
move the valve stem up and down.
1. Push
2. Push
3. Push
valve stroke by percentage and the lower line indicates absolute value of inner
resistance of the positioner. “MA” means that Manual mode is in operation.
4. Push
RA/DA, if
move fast, push
mode is displayed.
Parameter Mode (PARAM)
Parameter Types
There are four types in Parameter mode: Dead Zone, KP, KI, and KD.
These values are reflected as soon as they are changed, therefore the appropriate
values are found by checking the valve’s motion in real time.
Dead Zone (dEAdZONE)
This is the range of error % that the positioner is not adjusted. Hunting or oscillation
due to friction between the stem and packing is prevented by this parameter.
KP
This is a proportion constant value that is correction by error %. If this value is too
big, there can be hunting, even though it finds position by the input signal. If the
value is too small, accuracy gets worse.
KI
This is an integral constant value adding or subtracting the correction that is
corrected error % on the previous correction signal. If this value is too big, there can
be oscillation. If it is too small, the time to find the exact position increases.
KD
This is a differential constant value adding the previous correction signal with the
changing correction signal by the error % change rate.
Adjustment of Parameter
Dead Zone (dEAdZONE)
1. Push
2. Push
3. Push
4. Push
5. Adjust dEAdZONE value by pushing
applied immediately without additional operation. Users can easily check its
adjustment by changing the current input signal to the positioner. Optimum control
value is found by adjusting values during valve operation.
6. Push
7. Push
AUTO1
AUTO2
AUTO3
Zero Point
o
o
x
End Point
o
o
x
KP, KI, KD
x
o
o
RA/DA
x
o
o
Increase stem value slowly
Increase stem value quickly
Decrease stem value slowly
Decrease stem value quickly
Page 6
6 seconds
COMPLETED
6 seconds
COMPLETED
COMPLETED
6 seconds
6 seconds
6 seconds
then
3 times
COMPLETED