5 program mode – Detcon FP-624D User Manual
Page 22
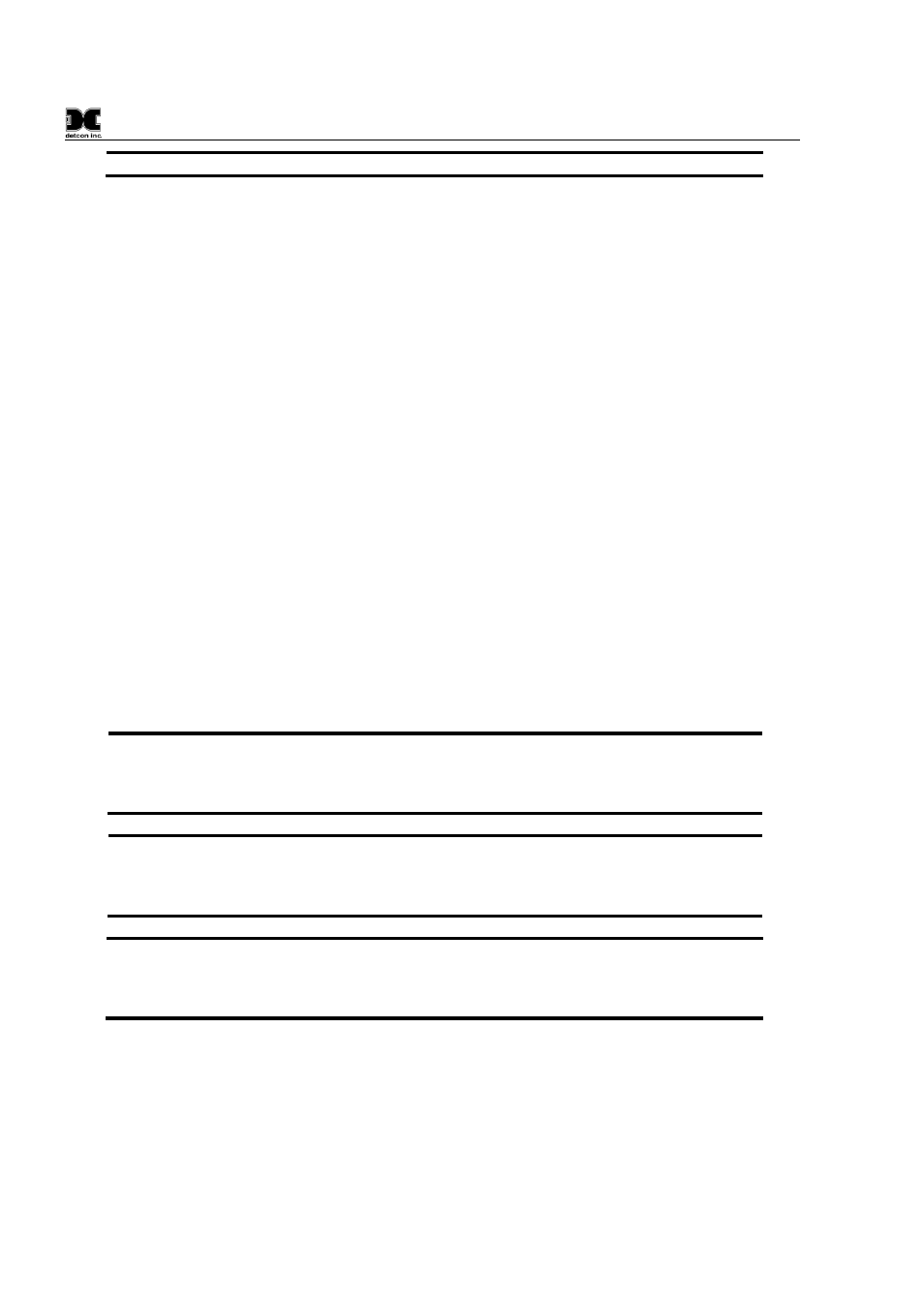
Model FP-624D
FP-624D Instruction Manual
Rev. 1.2
Page 18 of 42
Fault Status register will be set until the calibration is complete.
c) Apply the span calibration test gas at a flow rate of 200-500cc/min (200cc/min is the recommended flow
rate). As the sensor signal begins to increase, the display will switch to reporting a flashing “XX” reading
as the display shows the sensor’s “as found” response to the span gas presented. If it fails to meet the
minimum in-range signal change criteria within 2½ minutes, the display will report “Range Fault” twice
and the sensor will return to normal operation, aborting the AutoSpan sequence. The sensor continues to
report a “Range Fault” and will not clear the fault until a successful AutoSpan is completed.
Assuming acceptable sensor signal change, after 1 minute the reading will auto-adjust to the programmed
AutoSpan level. During the next 30 seconds, the AutoSpan sequence checks the sensor for acceptable reading
stability. If the sensor fails the stability check, the reading is re-adjusted back to the AutoSpan level and the
cycle repeats until the stability check is passed. Up to three additional 30-second stability check periods are
allowed before the unit reports a “Stability Fault” twice and the sensor will return to normal operation,
aborting the AutoSpan sequence. The sensor will continue to report a “Stability Fault” and will not clear the
fault until a successful AutoSpan is completed.
If the sensor passes the stability check, the sensor display reports a series of messages:
“AutoSpan Complete”
“Sensor Life XXX%”
“Remove Span Gas”
d) Remove the span gas and calibration adapter. The sensor will report a live reading as it clears toward “0”.
When the reading clears below 5 % LEL, the sensor will display “Span Complete” and will revert to
normal operation. If the sensor fails to clear to less than 5% LEL within 5 minutes, a “Clearing Fault” will
be reported twice and the sensor will return to normal operation, aborting the AutoSpan sequence. The
sensor will continue to report a “Clearing Fault” and will not clear the fault until a successful AutoSpan is
completed.
NOTE 1: If the sensor fails the minimum signal change criteria, a “Range Fault” will be
declared and a “Fault Detected” message will be displayed alternately with the sensor’s current
reading. The 4-20mA output will be taken to 0mA and the “Range Fault” bit in the Modbus
Fault Status register will be set.
NOTE 2: If the sensor fails the stability criteria, a “Stability Fault” will be declared and a
“Fault Detected” message will be displayed alternately with the sensor’s current reading. The
4-20mA output will be taken to 0mA and the “Stability Fault” bit in the Modbus Fault Status
register will be set.
NOTE 3: If the sensor fails the clearing time criteria, a “Clearing Fault” will be declared and a
“Fault Detected” message will be displayed alternately with the sensor’s current reading. The
4-20mA output will be taken to 0mA and the “Clearing Fault” bit in the Modbus Fault Status
register will be set.
3.5 Program Mode
Program Mode provides a “View Sensor Status” menu to check operational and configuration parameters.
Program Mode provides for adjustment of the AutoSpan Level, Bridge Voltage, Gas Factor, Cal Factor, Serial
ID, Alarm and Fault Settings. Additionally, Program Mode includes the diagnostic functions “Signal Output
Check” and “Restore Factory Defaults”.