Installation, Caution – Lincoln Electric IM846 POWER WAVE 405M User Manual
Page 13
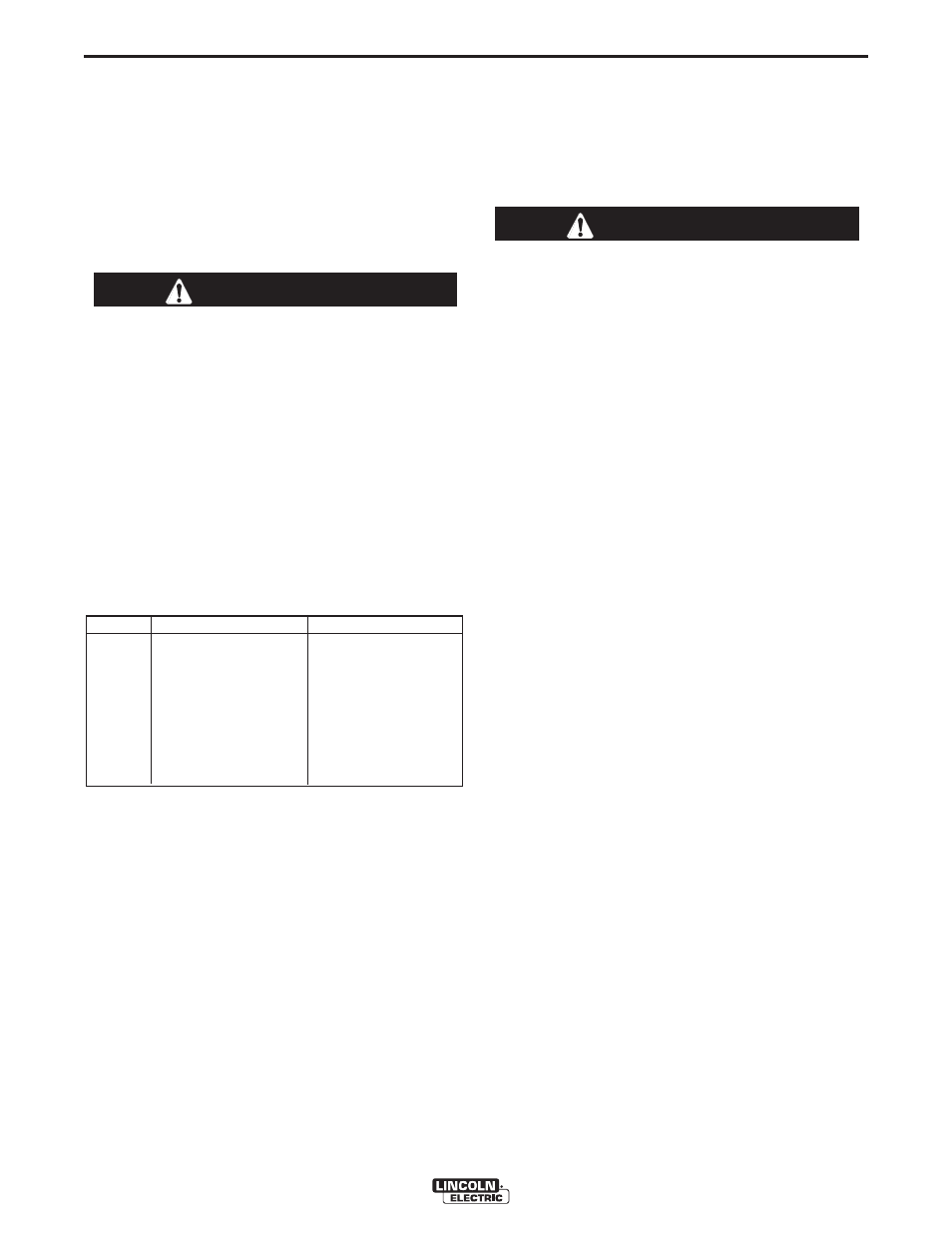
A-4
INSTALLATION
POWER WAVE
®
405M
A-4
VOLTAGE SENSING
The best arc performance occurs when the POWER
WAVE
®
s have accurate data about the arc conditions.
Depending upon the process, inductance within the
electrode and work lead cables can influence the volt-
age apparent at the studs of the welder. Voltage
sense leads improve the accuracy of the arc condi-
tions and can have a dramatic effect on performance.
Sense Lead Kits (K940-10, -25 or -50) are available
for this purpose.
If the voltage sensing is enabled but the sense
leads are missing, improperly connected, or if the
electrode polarity switch is improperly configured,
extremely high welding outputs may occur.
-----------------------------------------------------------------------
The ELECTRODE sense lead (67) is built into the
control cable, and is automatically enabled for all
semi-automatic processes. The WORK sense lead
(21) connects to the POWER WAVE
®
at the four pin
connector. By default the WORK voltage is monitored
at the output stud in the POWER WAVE
®
405M. For
more information on the WORK sense lead (21), see
"Work Voltage Sensing” in the following paragraph.
Enable the voltage sense leads as follows:
TABLE A.1
Process Electrode Voltage
Work Voltage
Sensing 67 lead *
Sensing 21 lead
GMAW 67 lead required
21 lead optional
GMAW-P 67 lead required
21 lead optional
FCAW
67 lead required
21 lead optional
GTAW
Voltage sense at studs
Voltage sense at studs
GMAW Voltage sense at studs
Voltage sense at studs
SAW
67 lead required
21 lead optional
CAC-C Voltage sense at studs
Voltage sense at studs
* The electrode voltage 67 sense lead is integral to
the control cable to the wire feeder.
Work Voltage Sensing
The standard POWER WAVE
®
405Mʼs default to the
work stud (work sense lead disabled)
For processes requiring work voltage sensing, con-
nect the (21) work voltage sense lead (K940) from the
POWER WAVE
®
work sense lead receptacle to the
work piece. Attach the sense lead to the work piece
as close to the weld as practical, but not in the return
current path. Enable the work voltage sensing in the
POWER WAVE
®
. (See Dip Switch Settings and
Locations in Installation Section of this manual.)
CAUTION
ELECTRODE VOLTAGE SENSING
Enabling or disabling electrode voltage sensing is
automatically configured through software. The 67
electrode sense lead is internal to the cable to the
wire feeder and always connected when a wire feeder
is present.
Important: The electrode polarity must be config-
ured at the feed head for all semi-automatic
processes. Failure to do so may result in extreme-
ly high welding outputs.
-----------------------------------------------------------------------
POWER FEED
®
WIRE FEEDER INTER-
CONNECTIONS
The POWER WAVE
®
405M and semi-automatic
Power Feed family communicate via a 5 conductor
control cable (K1543). The control cable consists of
two power leads, one twisted pair for digital communi-
cation, and one lead for voltage sensing. The cables
are designed to be connected end to end for ease of
extension. The output receptacle on the POWER
WAVE
®
405M is on the case front. The input recepta-
cle on the Power Feed is typically located at the back
of the feeder, or on the bottom of the user interface.
Due to the flexibility of the platform the configuration
may vary. The following is a general description of the
system. For specific configuration information, consult
the semi-automatic Power Feed
®
instruction manual.
SYSTEM DESCRIPTION
The POWER WAVE
®
405M and Power Feed
®
M family
of products utilize a digital communication system called
ArcLink. Simply put, ArcLink allows large amounts of
information to be passed at very high speeds between
components (nodes) in the system. The system requires
only two wires for communication, and because of its
bus-like structure, the components may be connected to
the network in any order, thus simplifying the system set-
up.
Each "system" must contain only one power source.
The number of wire feeders is determined by the type
of wire feeder. Refer to the wire feeder instruction
manual for details
CAUTION