LEESON SM-Plus Series Sub-Micro Inverters User Manual
Page 55
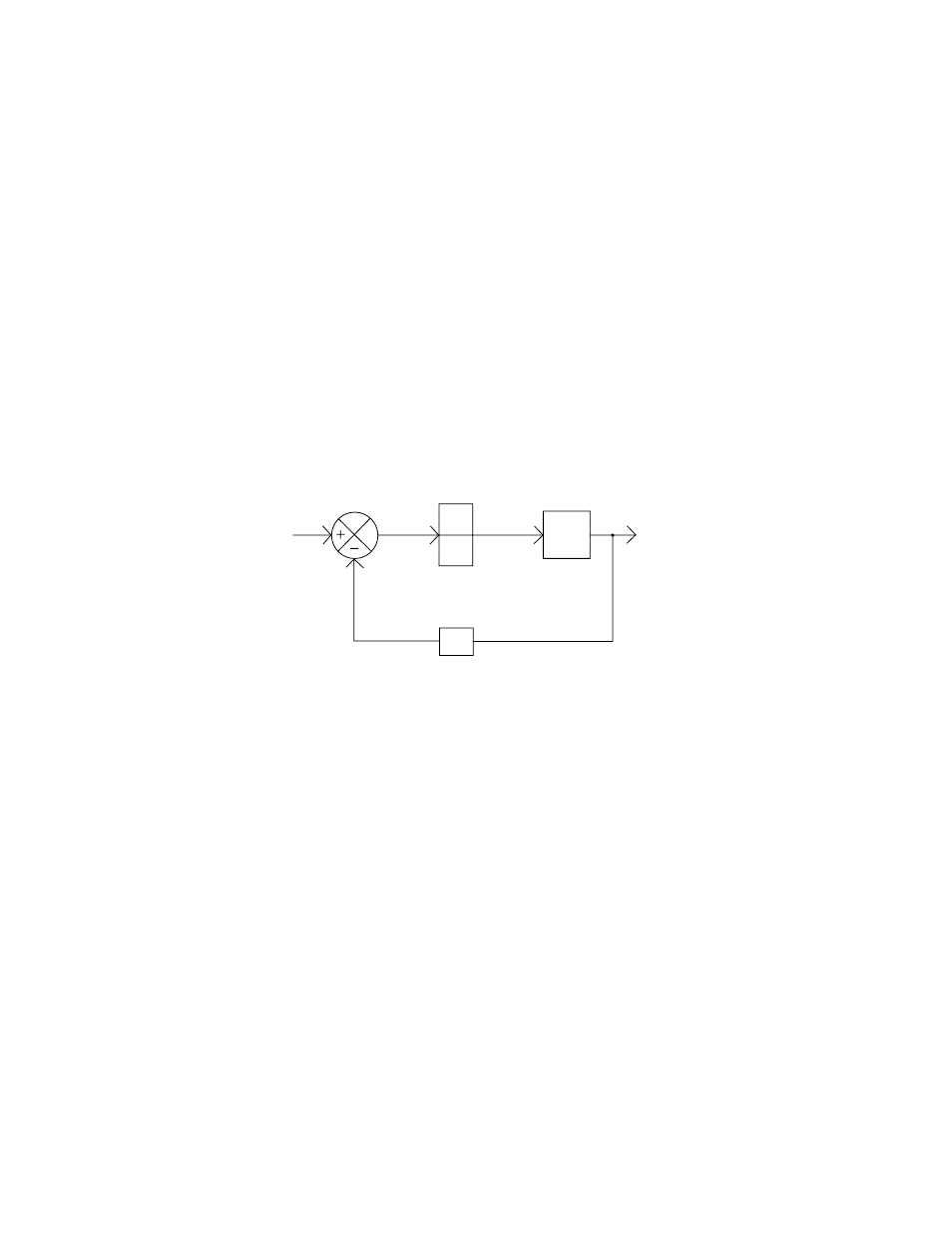
APPENDIX B – PI SETPOINT CONTROL OPTION
The following describes the PI Setpoint Control software option for the SM-Plus
™
drive. This software
option has additional parameters compared to the standard SM-Plus
™
drive. Also, some of the
parameters found in the standard drive have changed in the PI version.
PI Setpoint Control allows the SM-Plus
™
drive to maintain a process setpoint, such as PSI or CFM,
without using an external controller. When PI is activated the SM-Plus
™
will operate in a closed-loop
fashion, automatically adjusting the motor speed to maintain the process setpoint.
PI setpoint control requires feedback from the process in order to compare the actual process value to the
setpoint The difference between this value and the setpoint is called the error. The SM-Plus
™
drive will
increase or decrease the motor speed in an attempt to minimize the error. By constantly adjusting the
motor speed, the PI control will drive the process toward the setpoint. Refer to the PI block diagram
below:
B.1
DIRECT ACTING vs. REVERSE ACTING SYSTEMS
The PI function must be set to match the type of system that it will control. A direct (or normal) acting
system requires an increase in motor speed if the process variable decreases. A reverse acting system
requires a decrease in motor speed if the process variable decreases. Parameter 61 - PI MODE must be
programmed to the setting that matches the system (normal or reverse acting) and also the type of
feedback signal that is used (0-10 VDC or 4-20 mA).
B.2
FEEDBACK DEVICES
A transducer or transmitter is required to monitor the process variable and provide feedback to the PI
unit in order to compare the process value with the desired setpoint. A transducer outputs a signal
corresponding to a fixed range of the process variable. A transmitter provides offset and gain adjustments
to allow the output signal to be adjusted to correspond to different ranges of the process variable. Typical
output signals for transducers and transmitters are 0-10 VDC or 4-20 mA.
NOTE: If a 4-20 mA signal is used for feedback, and the signal is lost, the drive will display “FL” to indi-
cate the lost signal. The signal is considered lost if it drops below 2 mA.
51
SETPOINT
Error
Speed
P
Motor
PROCESS
VARIABLE
(PSI, CFM, etc)
I
Command
Process Variable
Feedback