Archive – Ransburg AdaptaFlow Node Adapter A10159 User Manual
Page 20
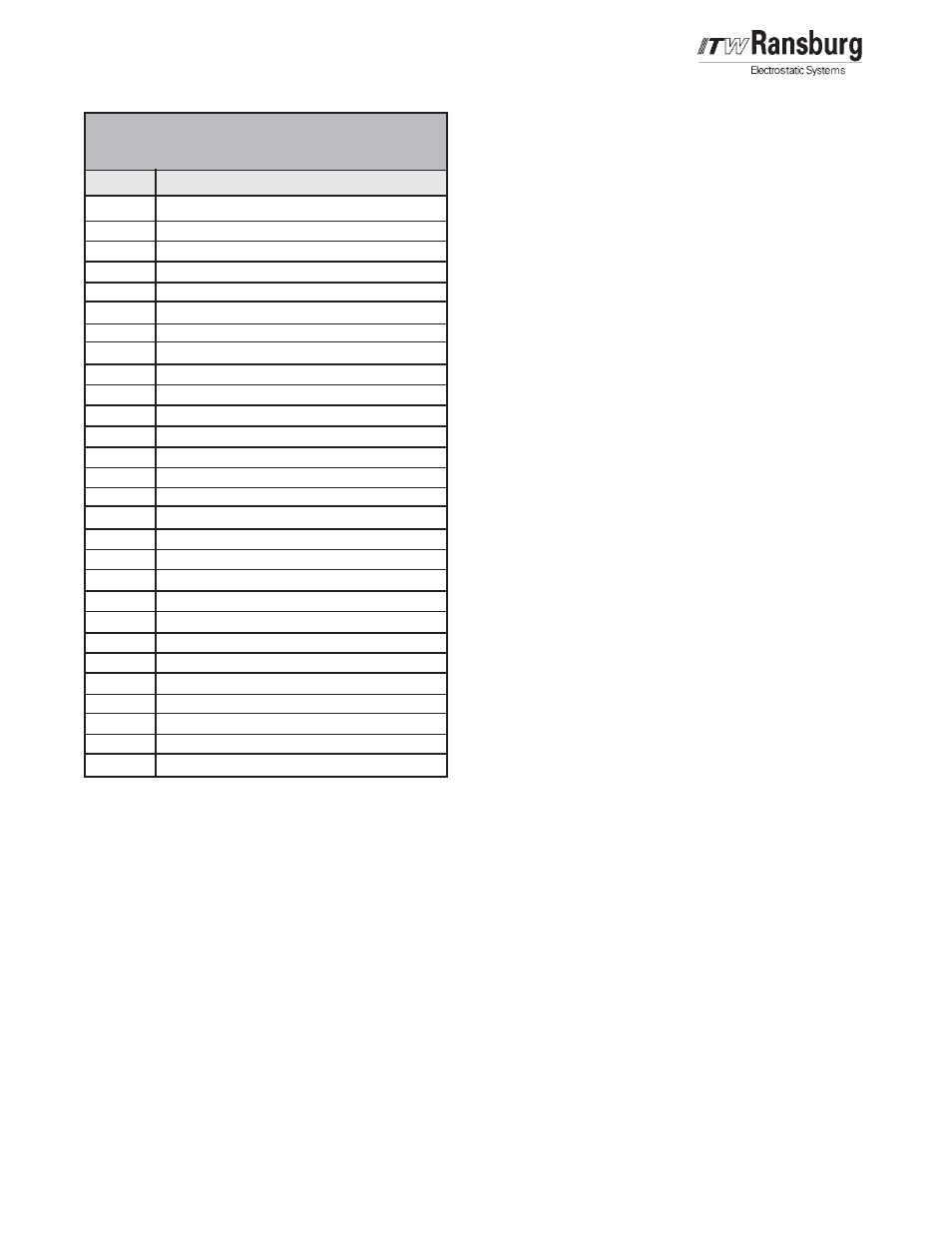
LN-9217-00.2
AdaptaFlow Node Adapter - Operation
1 7
1 7
1 7
1 7
1 7
Color Data Block T
Color Data Block T
Color Data Block T
Color Data Block T
Color Data Block Transfer
ransfer
ransfer
ransfer
ransfer
Write Operational Descriptions
Write Operational Descriptions
Write Operational Descriptions
Write Operational Descriptions
Write Operational Descriptions
- Refer to Figure 12
- Refer to Figure 12
- Refer to Figure 12
- Refer to Figure 12
- Refer to Figure 12
The Color Block Transfer Write is used to program
color variables for each flow controller channel.
Configuration Word
Configuration Word
Configuration Word
Configuration Word
Configuration Word
The BTW configuration word is set to 4 to inform
the flow controller that the following data is Color
Data write global data.
Global BTW Word
Global BTW Word
Global BTW Word
Global BTW Word
Global BTW Word
Configuration
Configuration
Configuration
Configuration
Configuration
Word #
Word #
Word #
Word #
Word # Description
Description
Description
Description
Description
0
1
2
3
4
5
6
7
8
9
10
11
12
13
14
15
16
17
18
19
20
21
22
23
24
25
26
27
Configuration Word (3)
Channel No. (1-4)
KFR Factor
Rate Display Eng. Unit (cc)
Rate Display Eng. Unit (M)
KFR DP Data
KFT Factor
Total Display Eng. Unit (cc)
Total Display Eng. Unit
KFT DP Data
Sample Amount
Cutoff Frequency
Operating Mode
PID Integral
PID Derivative
PID Delta Step
PID Death Delay
Volts 2 Offset (Analog Out #2)
Volts 2 Gain (Analog Out #2)
Volts 2 Shifter (Analog Out #2)
Volts 2 Pointer (Analog Out #2)
Volts in Offset
Volts in Gain
Total Limit 1
Total Limit 2
Flow Rate Limit 1
Flow Rate Limit 2
Controller ID
Figure 11: Global BTW Word Configuration
Figure 11: Global BTW Word Configuration
Figure 11: Global BTW Word Configuration
Figure 11: Global BTW Word Configuration
Figure 11: Global BTW Word Configuration
Channel Number
Channel Number
Channel Number
Channel Number
Channel Number
The Channel number is set to 1-4 to indicate which
channel is to store the data that is to follow.
Color Number
Color Number
Color Number
Color Number
Color Number
Is set to tell the flow controller where to store the
data that is to follow.
PID Proportional
PID Proportional
PID Proportional
PID Proportional
PID Proportional
This factor determines the strength, or overall
magnitude of change depending on the overall
response of a particular set of system components.
In many cases this value can only be determined
by experimenting and it is well advised to start with
a relatively low number. Too large of a number can
cause oscillations. Normal values are 100 to
1000. For paint applications, a starting value of
150 is recommended.
PID Initial Kick
PID Initial Kick
PID Initial Kick
PID Initial Kick
PID Initial Kick
The Initial Kick is beneficial in cases where the
regulator has a large hysteresis. The kick value
will be applied to the analog output if there is a Set
Value present, no fluid flow and the analog output
is less than the kick value. This is programmed in
a range from 0000 to 4095 steps which
corresponds to 0-10 VDC. The correct setting is
that value that will guarantee a minimal flow rate
above the fluid regulator cracking pressure.
PID Tolerance
PID Tolerance
PID Tolerance
PID Tolerance
PID Tolerance
This is the margin above and below the Set Point
that determines when the PID pursuit of reaching
the Set Point will be stopped. This window is also
referred to as a “dead band”. Depending on the
mechanics of the system, it is advisable to start
with a large window at first. Then, when system
tuning results in stable operation, this number can
be reduced.
Note that a small value here, will effect the stability
of the “Stable LED” and the Setpoint Achieved
status bit. This value is entered in hundredths of
Hertz. A value of 100 represents 1.00 Hz feedback
from the flow meter. A reasonable setting is 50.
ARCHIVE