Operation, Dr-1 plastic fluid regulator - operation – Ransburg DR-1 Plastic Fluid Regulator 75902 User Manual
Page 10
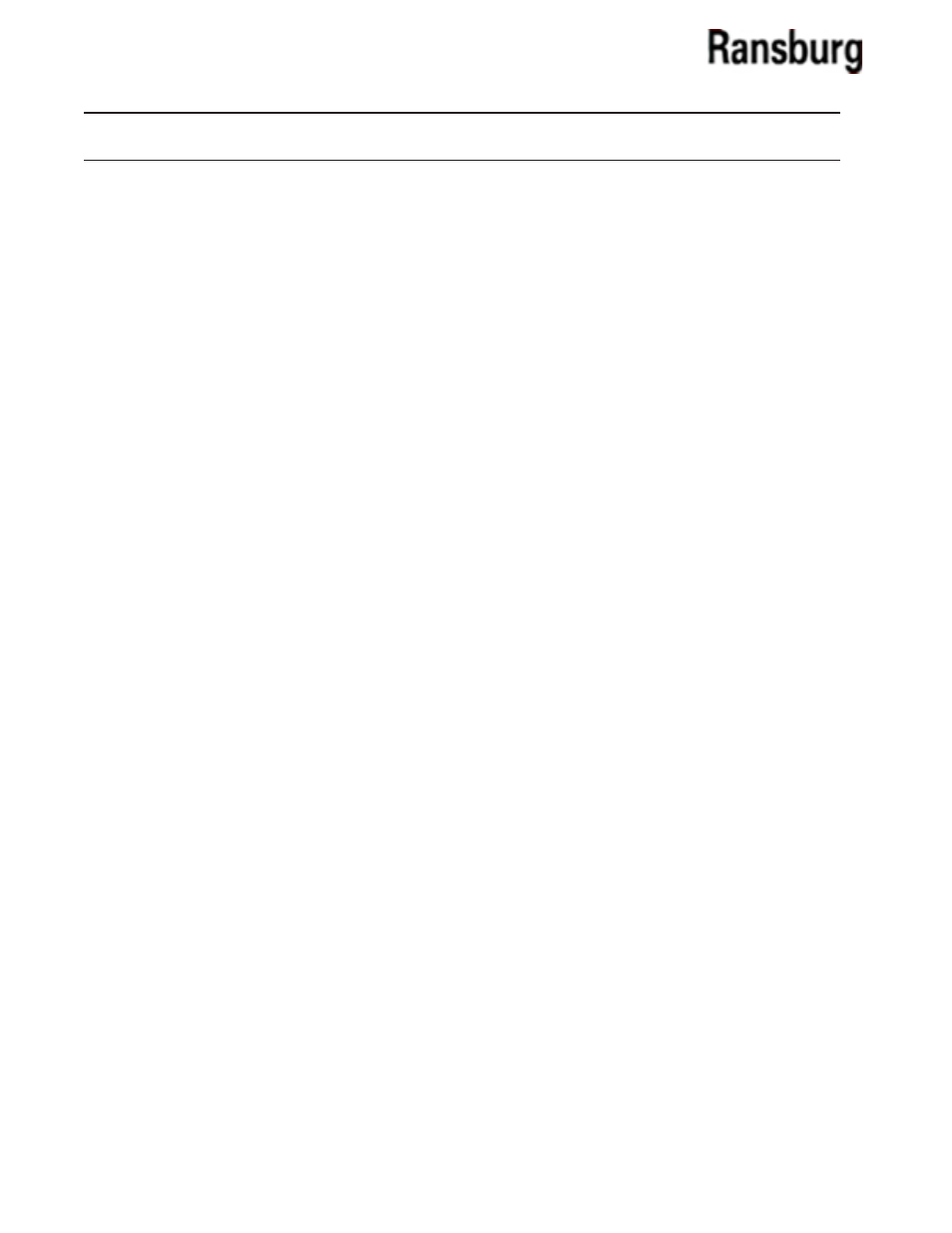
DR-1 Plastic Fluid Regulator - Operation
7
OPERATION
The DR-1
TM
Plastic Regulator is designed to provide
remote control fluid regulation for automatic coating
applications.
The regulator features two independently control-
lable flow pressure ranges from the fluid output port.
The high flow range port accomm-odates higher fluid
deliveries and minimal color change times. The lower
flow ranges provide precise fluid delivery control.
There are seven lower range models available (1:1,
1:2, 1:3, 1:4, 1:6, 1:8, and 1:10) which can be selected
based on the required fluid flow rate.
Separate pilot signals modulate each of the regu-
lator’s two diaphragms to control the amount of
paint being delivered from the regulator to the spray
applicator. These pilot signals can be controlled
manually or automatically with the AdaptaFlow
TM
5000, closed loop flow control system.
Because of the regulator’s dual range capabilities, it
provides the user flexibility of selecting either the
high flow range or the low flow range. Different
coating material viscosities and quick color change
requirements may necessitate the use of both ranges.
If color change time is not a factor or if material vis-
cosity remains relatively constant, either port may
be used depending on flow rate requirements. All
regulators, regardless of ratio designation, have the
high flow port.
The low flow (i.e. 1:2, 1:4, etc.) port provides a lower,
more precise flow response curve. Fluid output, as
a result, is less likely to be affected by pilot signal
errors. An increase in the ratio (i.e. from 1:2 to 1:4)
provides a lower slope in the flow/air signal pressure
curve, but, more precise response curve. This same
increase in ratio, however, will reduce flow capacity
and should be considered when selecting the proper
regulator ratio.
The following factors must then be considered when
selecting the regulator ratio required for proper fluid
control:
• Fluid tubing inside diameter (ID) and length
• Fluid feed tube inside diameter (ID) and length
• Fluid viscosity
• Fluid input pressures
Preliminary testing will determine which regulator
ratio should be used. If conditions change after
installation which require a different low flow ratio,
this regulator can be altered easily by replacing the
existing ratio spacer ring and upper retainer with the
desired ratio (ratio designation is etched on the side
of the spacer ring).
LN-9228-00.3