Finish Thompson MSVKC Series User Manual
Page 4
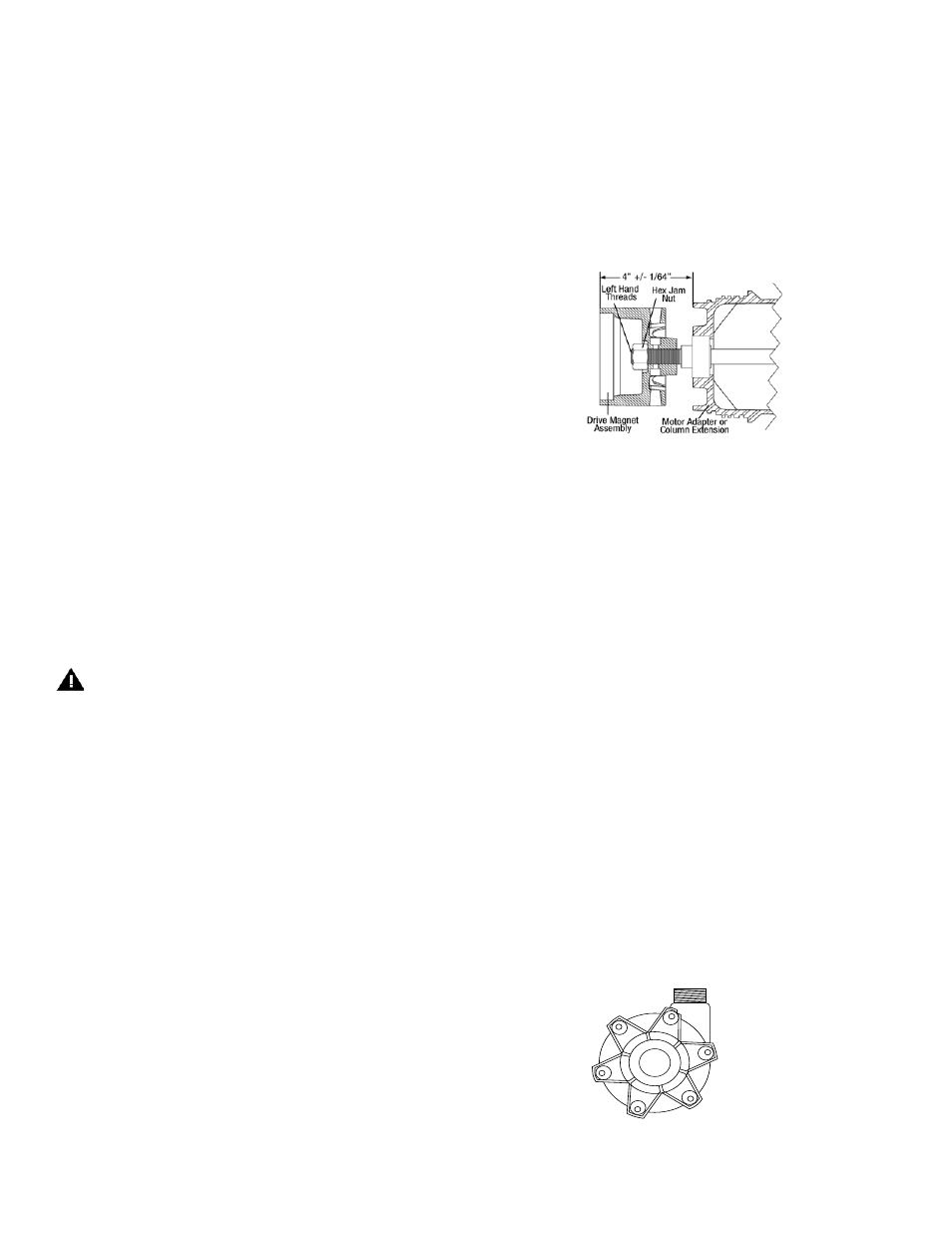
45
7. Examine all of the o-rings for nicks or chemical attack and replace as
needed.
8. If the motor requires replacement, loosen the set screws and remove
the coupling half (part of item 29) from the motor shaft.
Caution: Improper orientation of the metric motor adapter can cause
premature coupling failure or cause the pump shaft to bottom out on
the motor shaft before
5. Install the coupling insert (center plastic part of item 29) onto the
coupling half on the motor. Now insert the pump shaft with coupling
half into the coupling insert until it is completely seated.
6. Locating the pump shaft through the bearing in the motor adapter
section (item 9) carefully slide the motor adapter (item 9) down the
shaft until it is fully seated on the (56C) motor rabbet or (63, 71, 80
frame) on the metric motor adapter. If a mounting plate (item 10) is
being used, gently slide it over the pump shaft and the motor adapter
section (item 9).
7. Rotate the mounting plate and the motor adapter to the desired
orientation (marked before disassembly), and align the holes through
the mounting plate, motor adapter and into the motor (metric motor
adapter if used). Secure the mounting plate and the adapter to the
motor (item 1)/metric adapter (item 2) using the correct hardware
(items 6, 7, & 8 for 56C or item 33 for metric).
8. Tap down gently with a rubber mallet on the top of the pump shaft
to ensure compete coupling engagement. Tighten both bearing set
screws onto the pump shaft using a 3/32” Allen wrench. Replace if
needed and lubricate the two motor adapter/ column extensions o-rings
(item 12) with a chemically compatible thread lubricant.
9. For 12” pumps, go to step 10. For 18” or longer pumps, slide the lock
ring (item 11) past the corresponding flats toward the motor. Make
sure to place the smaller inside diameter side of the lock ring toward
the motor. Use a chemically compatible thread lubricant to lubricate the
external plastic threads on the motor adapter (item 9) and the internal
11. Place the barrier/housing adapter on a clean surface with the white
ceramic post facing up. Place the impeller drive assembly (items 18
and 19) onto the ceramic post. Install and lubricate (with a chemically
compatitible lubricant) the housing o-ring (item 17).
12. Noting the reference marks made during disassembly on the impeller
housing and the barrier column assembly, align the bolt hole tabs and
snap the housing in place (bolt hole alignment is critical).
13. Install and lubricate the diffuser o-ring (item 21). Install the diffuser
assembly (item 22) being careful not to dislodge the o-ring and to keep
the bolt hole alignment straight.
14. If the impeller drive shaft (item 23) was replaced, reassemble it onto
the impeller assembly (item 19) by matching the three tabs on the end
of the drive shaft with the three recessed slots in the impeller assembly
and pressing together.
15. Looking through the hole in the center of the diffuser assembly, note
the orientatin of the square recess in the top of the first stage impeller
drive (item 18). Insert the square end of the drive shaft through the
hole in the diffuser and into the square recess in the impeller driive.
Press gently but firmly to seat the drive shaft.
16. Install and lubricate the housing o-ring (item 17) onto the diffuser (item
22). Lower the first stage impeller housing (item 24) straight down
onto the pump with the ceramic front spindle support sliding into the
bushing (item 18A) on top of the first stage impeller assembly. Orient
the housing with the direction arrow on top (same as discharge direc-
tion), the drain boss on the bottom, andwith the mounting holes aligned.
Install the mounting bolts and hardware (items 25A, B & C) making
sure not to dislodge the housing o-ring (item 17) or the diffuser o-ring
(item 21). Hand tighten the mounting bolts to pull the pump together
using the pattern shown in Figure 4.
plastic threads on the column extension (item 30). Gently slide the
column extension with bearing onto the pump shaft. Install if needed
and lubricatethe two column extension o-rings (item 12). Repeat step
9 for each column extension to be installed.
10. Thread the left hand threaded drive magnet assembly (item 14) onto
the pump shaft until it is 4” +/- 1/64” as measured from the top of
the drive magnet assembly as shown in Figure 3. A 9/16” wrench can
be used on the milled flats below the threads to hold the pump shaft
during this step. Apply a small amunt of Loctite Thread Locker 262
to the left-hand threaded 5/8-18 hex jam nut (item 15) and thread
onto the pump shaft. Tighten to 50 ft. lbs. Recheck the drive setting
dimension after the nut is tightened.
Figure 4
3
1
6
4
2
5
Figure 3
Reassembly
1. If the motor was replaced-
Slide the coupling half (half of #29) on to the motor shaft with the
splines facing away from the motor. On 56C motors, set coupling half
so that motor shaft is recessed 7/32”.
For 63 and 71 frame motors, set coupling half so that motor shaft is
recessed 7/16”, and on 80 frame motors set coupling half so that it
is flush with the motor shaft.
2. On 56C, 63, & 80 frame motors, align one set screw with flat or key slot
on motor shaft and tighten both set screws with a 1/8” Allen wrench
to 70 in.-lbs. (7.9 N-m). For 71 frame motors, align both set screws 90
degrees from motor flat or key slot and tighten as instructed above.
3. If the shaft was replaced, slide the second coupling half onto the pump
shaft (the end with the milled flat) with the splined side facing away
from the threaded end of the shaft. For 56C motor frames, set the
coupling with the pump shaft recessed 7/32”. For 63 and 71 motor
frames, set it with the pump shaft recessed 7/16”. For 80 frame, the
pump shaft should be recessed ¼”. When coupling half is set correctly,
align set screw with the flat on the pump shaft, and tighten both set
screws with 1/8”allen wrench to 70 in.-lbs. (7.9 N-m).
4. Place the motor gently on the fan cover for reassembly. For metric
frame pumps, install the metric motor adapter flange (item 2) onto
the motor with the correct hardware (items 3, 4, & 5). One side of
the adapter fits 63 & 80 frame motors (side B) and the other side fits
the 71 frame motors (side A). The letters A & B are molded onto the
adapter. For 71 frame motors the “A” must face the motor, and for
63 & 80 frame motors the “B” must face the motor. The metric motor
adapter must be oriented so that the adapter seats completely onto
the motor rabbet. Make sure your orientation marks are aligned (step
10 of disassembly instructions).
note: It is not recommended to reuse plastic screws. Always use
thread lubricant when installing plastic screws.