Fuel system components – Mityvac MV5545 FST PRO FUEL SYSTEM TESTER User Manual
Page 17
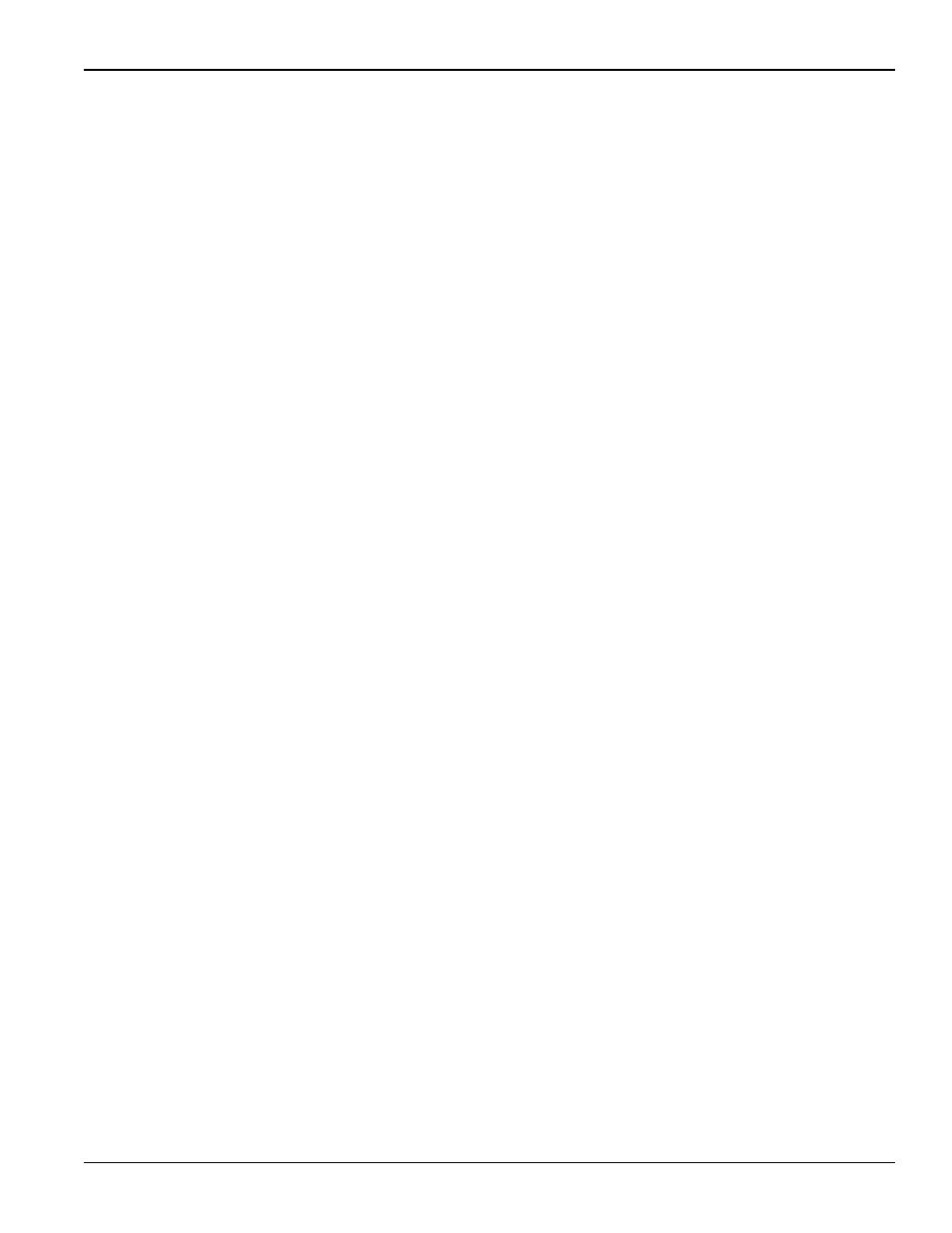
Form 824127
Page Number - 17
Fuel System Components
The modern fuel delivery system is comprised of several critical
components. A malfunction of one or more of these can cause
the system to fail or under perform. The function of the FST is
to diagnose when a fuel system failure has occurred, and to
pinpoint the component(s) which caused the failure. To reach
an accurate diagnosis, a basic knowledge of the fuel system
components and their role in achieving optimum engine
performance is helpful. Following is a list of common compo-
nents that contribute to the function of the fuel delivery system.
A failure of one or more of these components can typically be
diagnosed using the FST Pro:
•
Fuel Tank
•
Fuel Pump
•
Fuel Pump Inlet Strainer/Sock
•
Inline Fuel Filter
•
Pressure Regulator
•
Fuel Lines
Fuel Tank
The fuel tank serves as a reservoir to store the fuel until it is
needed by the engine. Fuel tanks have been manufactured from
a variety of metals and plastics. The fuel pump hangs down into
the tank, drawing the fuel from very close to the bottom. The
most likely influences of the fuel tank towards a fuel system fail-
ure would be the result of rust or scale produced by a metallic
tank, the collection of impurities introduced from the outside, or
a dented tank that interferes with the function of the fuel pump.
It is critical that the fuel tank be emptied, cleaned, and inspected
any time a fuel pump is replaced or impurities are suspected.
Fuel Pump
The fuel pump is the heart of the fuel delivery system. It pumps
fuel from a vehicle’s fuel tank to the engine, where it is mixed
with air and injected into the cylinders for burning. Fuel pumps
in most modern fuel delivery systems are located inside the fuel
tank, and run on electricity supplied by the vehicle’s electrical
system. They pump a continuous volume of fuel at a given
voltage, and are typically extremely reliable when operated
under the conditions for which they are designed. Despite their
reliability and the high cost and hazard of replacement, fuel
pumps have a higher return rate than almost any other
automotive part. They are commonly misdiagnosed and
needlessly replaced, costing consumers, repair shops and
manufacturers millions of dollars each year. It’s estimated that
80% or more of returned pumps are found to function properly
when tested by the manufacturer.
Most mechanically regulated fuel delivery systems operate the
fuel pump at one speed, based on a constant voltage from the
electrical system. However some automotive manufacturers
have begun incorporating two or three speed pumps to improve
efficiency and reduce emissions. Like electronically regulated
returnless systems, the speed of the pump is controlled by the
ECM. However the ECM does not increase pump speed based
on fuel pressure. In such a case, the fuel pump may not
increase speed/output in reaction to the simulated load method
used by the FST. Instead, a scanner or manufacturer’s software
is required to manually increase the speed in order to test the
peak capability of the pump. The manufacturer’s service manual
should document this in their fuel system diagnostic procedure.
Fuel pumps fail or fail to perform due to high mileage,
contaminated fuel, or electrical problems. While there is no fix
for wear due to high mileage, fuel and electrical problems can
be identified, corrected, and prevented. In the case of fuel
contamination, it is almost certain the pump will have to be
replaced due to irreversible damage. However, electrical issues
such as a loose ground, bad connection, or low voltage, can
many times be corrected before the pump experiences any
permanent damage.
Contaminated fuel is a major cause of fuel pump failures. Dirt,
debris and scale can clog the inlet strainer and fuel filter causing
the pump to work harder and reduce its life. They also wreak
havoc inside the pump by acting like an abrasive to grind at
parts. Chemical contaminates can cause precision made
components to swell or gum-up, leading to under-performance
or complete failure. For all of these reasons, fuel tanks should
be completely drained and professionally cleaned, or possibly
even replaced, each time a fuel pump is replaced or
contamination is suspected.
Check all electrical connections. When electrical connections fail,
voltage to the pump will be reduced, causing the pump to run
inefficiently and ultimately reducing its life. Check the vehicle
harness plugs for soot or burned wires. Check the pump
module/hanger plug for melted plastic or loose terminals on the
flange. Perform a voltage drop test across all electrical connec-
tors and all electrical components involved with the fuel pump.
Also check the wires from the pump to the flange when replacing
a pump-only application. A damaged wiring harness, if not
repaired, may cause a premature failure to a replacement pump.
Each component of the fuel delivery system has its own unique
affect on pressure and flow when it malfunctions. When a fuel
pump is failing or under-performing, its total output declines,
causing both flow and pressure to drop. When testing a
vehicle’s fuel delivery system with the FST Pro, the affects of an
under-performing pump can be diagnosed by observing how
pressure and flow respond to simulated load conditions. Other
common test methods such as testing amperage draw or
pressure alone can not reliably detect a malfunction, and/or
do not have the capability to simulate a load condition. This,
combined with a lack of fuel delivery system knowledge and
training, leads to the high rate of misdiagnosis.
Fuel Inlet Strainer/Sock
Fuel flows from the tank through an inlet strainer/sock before
entering the fuel pump. It is designed to capture dirt and debris
that could damage the pump. Because it is not easily accessi-
ble, it is large in size so that it should not have to be replaced
except when the pump is serviced or replaced.
If the inlet strainer becomes clogged or plugged, it will limit the
amount of fuel flowing to the fuel system, to the point that it will
starve the engine of adequate pressure and volume. This can
create drivability problems. In addition, a clogged strainer makes
the fuel pump work harder to pull fuel through it, and can starve
the pump of fuel that it needs for lubrication and cooling. All of
these factors can lead to premature pump failure.