Electronic installation – Max Machinery 234 Flow Meter User Manual
Page 8
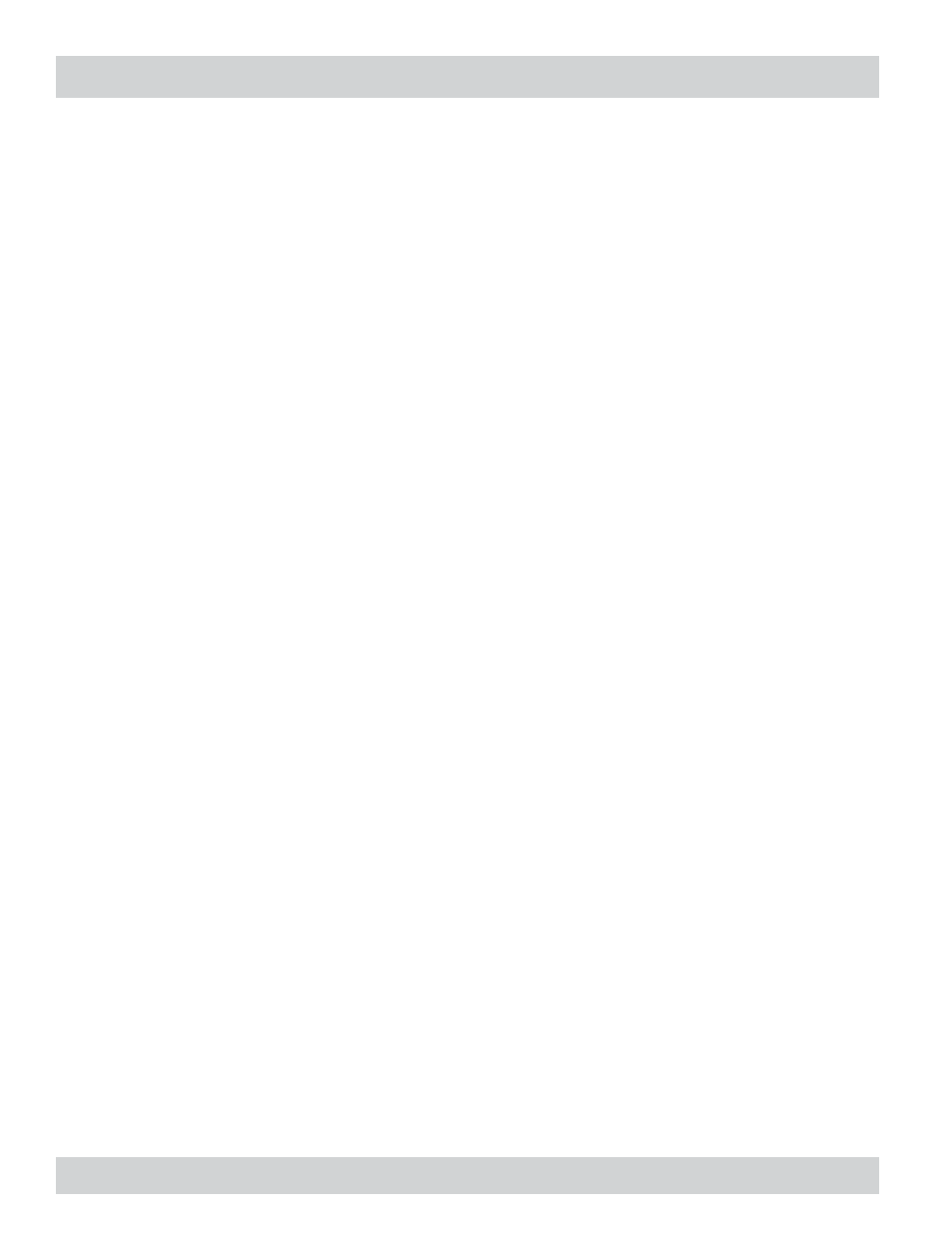
( 8 )
234-000-350 © 2005 Max Machinery, Inc.
Electronic Installation
‘SLOW’ LED:
D8: If a calibration is initiated but the flow rate is too low to give acceptable results, the calibration will be
aborted, and this LED will light up red for 10 seconds . See Calibration Section for more information on
calibration procedures .
‘MEMORY FAIL’ LED:
D7: The microprocessor continually checks the integrity of its program storage memory . If one or more memory
values do not read what they are supposed to, this LED will turn on . Two possible causes of memory failure are
prolonged operation/storage at temperatures exceeding the ratings and transient voltages applied to inputs and/
or outputs that exceed ratings . If the transmitter does not appear to be functioning correctly and this LED is on,
the unit should be sent back to the factory for service .
The coils of the Model 234 stators and the printed circuit board need to be calibrated as a set . The calibration
procedure initiates a routine that determines the offsets needed to balance the output signals from the coils .
When used with a piston flow meter, the calibration procedure includes an additional routine that measures the
linear position of the stator with respect to the meter . This allows the transmitter to compensate for cyclical
variations in rotational velocity of the meter, resulting in a steady output frequency .
The recommended flow range for calibration is that which will turn the meter at 20-500 rpm . Lower flow rates
(resulting in rotor speeds below 20 RPM) will cause the ‘SLOW’ LED to come on and the calibration will not take
place . Successful calibration will occur at higher flow rates (rotor speeds above 500 RPM) but the results may
not be as good as those which would be obtained at a lower flow rate . A flow rate resulting in a flow meter
rotation of 100 rpm will give good calibration results .
When doing a calibration on a piston meter, it is critical that the flow rate remains constant (less than 10%
variation) for the routine that determines the linear position to be successful . When a steady flow passes
through a four-piston meter, the meter speeds up and slows down 4 times per revolution . The phase of this
cyclic speed variation is determined during calibration by finding the position of the 4 speed peaks in a
revolution . These speed peak locations are measured for 8 revolutions (32 peaks), then run through an
averaging procedure . Once this is done, the tachometer can internally compensate for the speed variations to
output a steady frequency under steady flow conditions .
Error can be introduced into this phasing procedure if the system flow rate is pulsating (i .e .: driven by a piston
pump) . If there are peaks in the flow rate that overshadow the speed peaks due to the 4-piston geometry, the
calibration routine will incorrectly determine the phase of the cyclic speed variation and will subsequently apply
the compensation out of phase .
The phase balancing routine that occurs for all types of meters requires 16 revolutions of the meter to reach
completion . The ‘CAL’ LED changes color (red to green or green to red) 4 times per revolution, or 64 blinks for
the entire calibration . The linear position determination (phasing) requires 8 revolutions, so the ‘CAL’ LED will
blink an additional 32 times after the 64 phase balancing blinks when calibration is performed on a piston meter .
If the flow is stopped part way through a calibration, the blinking will stop and the calibration will not reach
completion since it requires a fixed number of meter revolutions . In such a case, a new calibration should be
done at a steady flow rate .