Electronic installation – Max Machinery 234 Flow Meter User Manual
Page 6
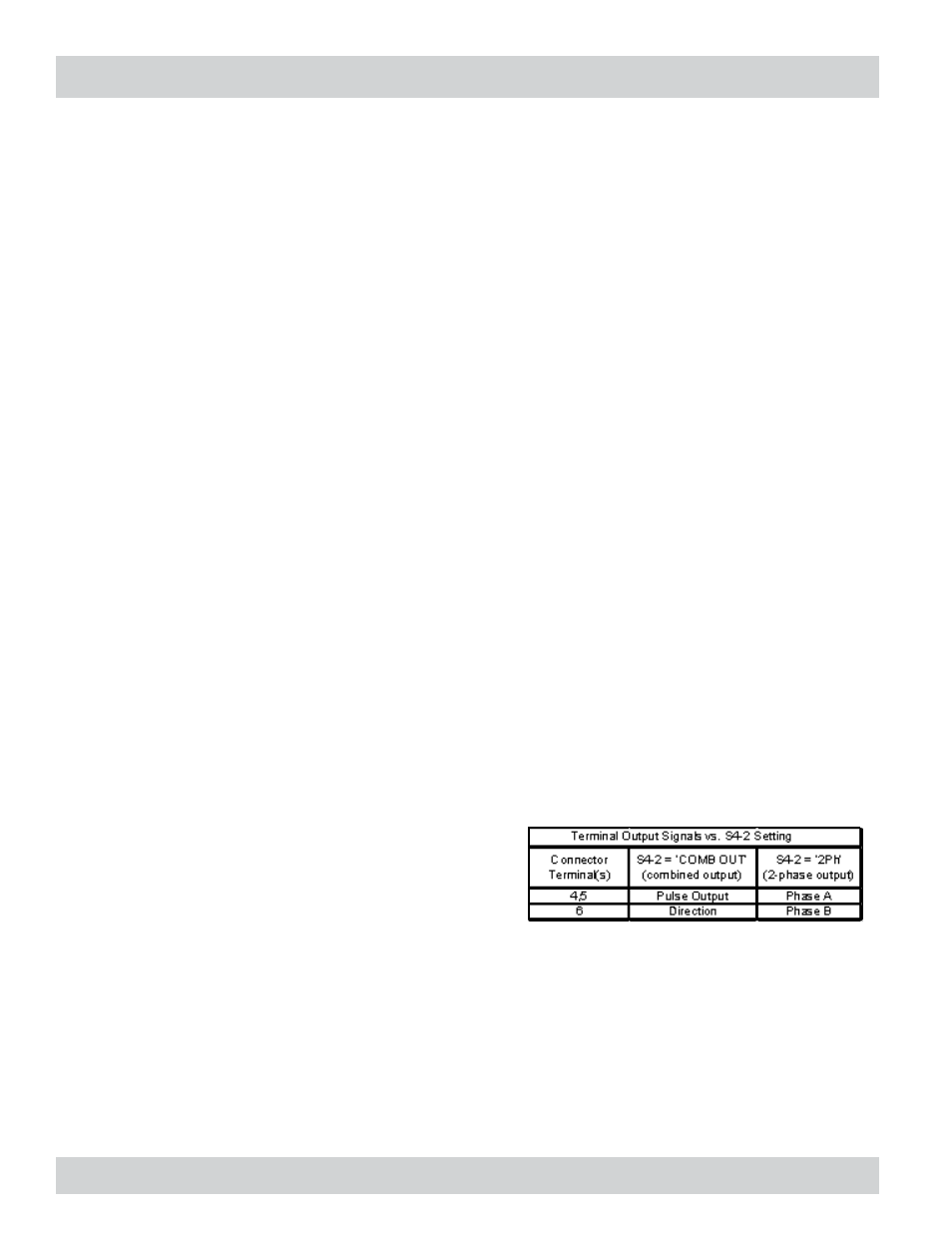
( 6 )
234-000-350 © 2005 Max Machinery, Inc.
Electronic Installation
Environment: The transmitter housing should be kept as cool as possible due to the temperature limits of the
electronic components . If the ambient temperature rises above 1300F (550C), the maximum fluid temperature at
the flow meter will have to be derated .
The weather-tight versions of the flow meter require that the electrical conduit connection be sealed with pipe
dope or a potting fitting . If this precaution is not taken, moisture may form inside the transmitter housing,
resulting in inaccurate readings or circuit failure . The amphenol connector versions of the Model 234 offer
moderate protection from moisture and dust, but are not totally sealed .
Grounding: Two dip switches are provided . The Ground Switch S1-1, when activated, connects the circuit common
to the case terminal . The Filter Switch S1-2 connects common to case through two back to back electrolytic
capacitors . These two switches facilitate system grounding procedures which will reduce electrical noise problems .
It is advisable to have the common of any system physically grounded at one point only . If your system is grounded
at the receiving or indicator end, then it is not advisable to also ground it at the transmitter end . This may cause
a ground loop . In this case, it is advantageous to connect the circuit common to case via the capacitors (filter) .
This will give some extra immunity to electrical noise .
Interconnections: The cable connection to the Model 234 should be made with shielded cable, with the shield
itself connected only at the receiving end . The transmitter output stage is designed to drive up to 1000 feet (300
m .) of cable without problems . Even longer lengths may prove feasible depending on such factors as external
electromoagnetic interference and the sensitivity of the receiving indicator .
K-Factors: Each Model 234 Flow Meter is supplied with a calibration sheet showing the actual number of pulses
output per cubic centimeter (or other engineering unit) of metered fluid at several different flow rates . These
numbers are termed “K-Factors” . The individual or average K-Factor is used to calibrate the receiving indicator for
the proper display in the desired engineering units .
Reverse Flow Buffer: The transmitter square wave signal employs a reverse flow buffer designed to eliminate
false ouputs when the flow meter is subjected to hydraulic or mechanical oscillations with no actual net flow . Flow
through the meter must total 1/2 of a revolution (approx . 5 .4 cc) before a pulse is output in either the forward or
reverse direction . At low flows, a noticeable period of time will be required to fill up this buffer . For instance, at 20
cc/min, 15 seconds will elapse before an output signal is observed .
Two-Phase or Square Wave Select:
S4-2: Depress side that corresponds to desired output . ‘2PH’ gives a 2-phase quadrature output with the two
phases separated by 90° (Ph A on Terminal 5 and Ph B on Terminal 6) . The ‘COMB OUT’ setting gives a single
square wave output that combines the information in the two
phases into a single output of double the frequency (Combined
Output on Terminal 4, Direction on Terminal 6) . If S4-2 is set
wrong, an unexpected output signal will result since the same
output circuitry is used for the two distinct output options .
Output Frequency Select:
S3: Rotary switch allows selection of output resolutions of 16 to 500 pulses per revolution (square wave output),
or 8 to 250 pulses per revolution (per phase) if the 2-phase output option is selected . The resolution can be
changed while the tachometer is operating, and the new value will take effect immediately . Please Note: The
screen printed resolution on the circuit board applies to 210/220/240 Series meters . See table for resolution .
Output Indicators:
D10, D11: These bi-color (red, green) LEDs indicate the status of the outputs . If the 2-phase output mode has
been selected, the state of Phase A and Phase B are each shown on the corresponding LEDs (‘OUT/
∅A’ and
‘DIR/
∅B’) . If the combined output mode has been selected, the LED labeled ‘OUT/∅A’ shows the status of the
pulse output channel, and the LED labeled ‘DIR/
∅B’ indicates the direction .