Magnum Venus Plastech Powerhead Powerslide 7000 Series User Manual
Page 6
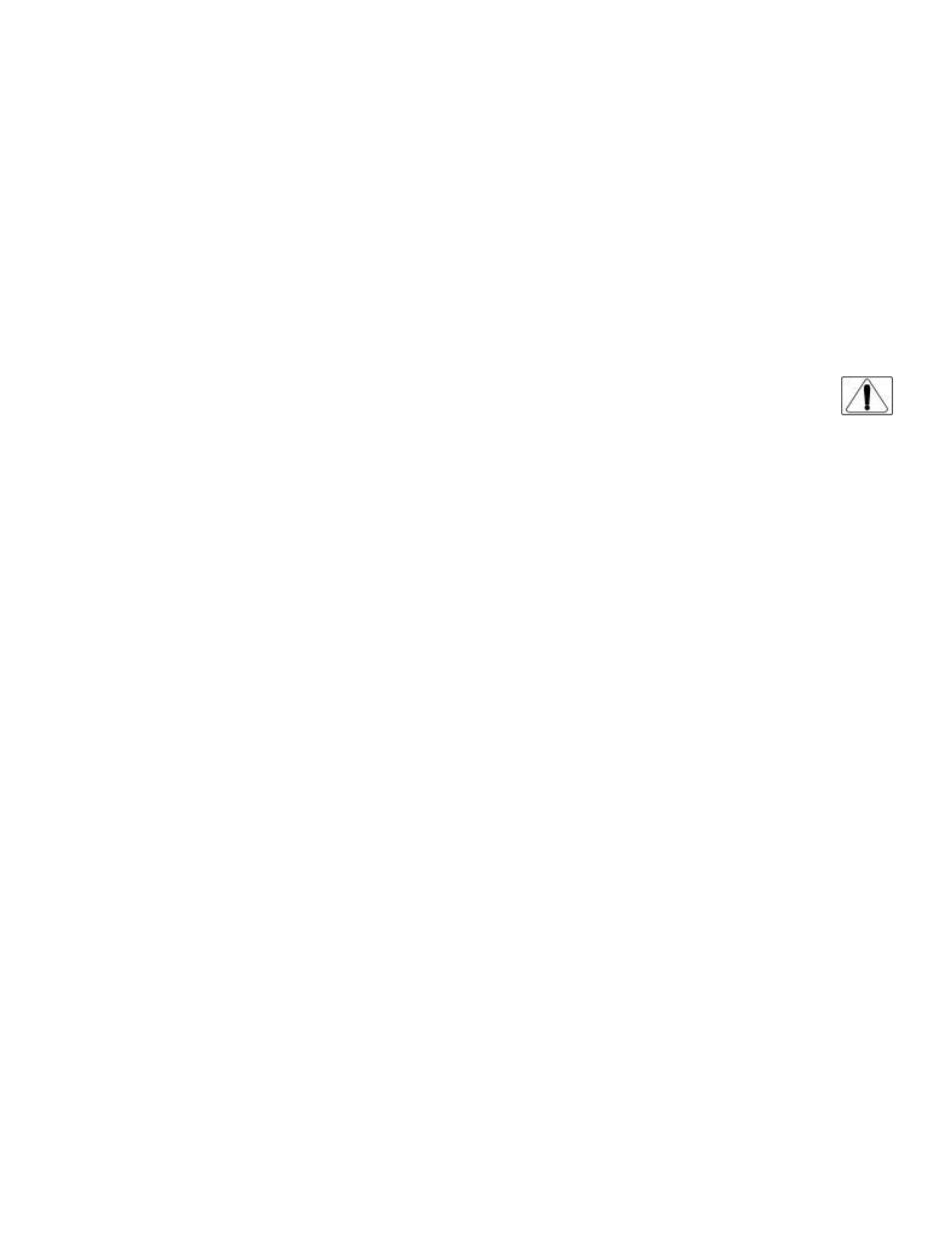
MAGNUM VENUS PLASTECH Powerslide Dual Rod
6
2.2 Catalyst (Methyl Ethyl Ketone Peroxide)
MEKP is among the more hazardous materials found in commercial channels. The safe
handling of the “unstable (reactive)” chemicals presents a definite challenge to the
plastics industry. The highly reactive property which makes MEKP valuable to the
plastics industry in producing the curing reaction of polyester resins also produces the
hazards which require great care and caution in its storage, transportation, handling,
processing and disposal. MEKP is a single chemical. Various polymeric forms may exist
which are more or less hazardous with respect to each other. These differences may
arise not only from different molecular structures (all are, nevertheless, called “MEKP”)
and from possible trace impurities left from the manufacture of the chemicals, but may
also arise by contamination of MEKP with other materials in its storage or use. Even a
small amount of contamination with acetone, for instance, may produce an extremely
shock-sensitive and explosive compound.
Contamination with promoters or materials containing promoters, such as
laminate sandings, or with any readily oxidizing material, such as brass or iron,
will cause exothermic “redox” reactions which can become explosive in nature.
Heat applied to MEKP, or heat build-up from contamination reactions can cause it
to reach what is called its Self-Accelerating Decomposition Temperature (SADT).
Researchers have reported measuring pressure rates-of-rise well in excess of 100,000
psi per second when certain MEKP’s reach their SADT. (For comparison, the highest
pressure rate-of-
rise listed in NFPA Bulletin NO.68, “Explosion Venting”, is 12,000 psi
per second for an explosion of 12% acetylene and air. The maximum value listed for a
hydrogen explosion is 10,000 psi per second. Some forms of MEKP, if allowed to reach
their SADT, will burst even an open topped container. This suggests that it is not
possible to design a relief valve to vent this order of magnitude of pressure rate-of-rise.
The user should be aware that any closed container, be it a pressure vessel, surge
chamber, or pressure accumulator, could explode under certain conditions. There is no
engineering substitute for care by the user in handling organic peroxide catalysts. If, at
any time, the pressure relieve valve on top of the catalyst tank should vent, the area
should be evacuated at once and the fire department called. The venting could be the
first indication of a heat, and therefore, pressure build-up that could eventually lead to an
explosion. Moreover, if a catalyst tank is sufficiently full when the pressure relief valve
vents, some catalyst may spray out, which could cause eye injury. For this reason, and
many others, anyone whose job puts them in an area where this vented spray might go,
should always wear full eye protection even when laminating operations are not taking
place.
Safety in handling MEKP depends to a great extent on employee education, proper
safety instructions and safe use of the chemicals and equipment. Workers should be
thoroughly informed of the hazards that may result form improper handling of MEKP,
especially in regards to contamination, heat, friction and impact. They should be
thoroughly instructed regarding the proper action to be taken in the storage, use and
disposal of MEKP and other hazardous materials used in the laminating operation. In
addition, users should make every effort to:
A. Store MEKP in a cool, dry place in original containers away from direct sunlight and
away from other chemicals.