Jungheinrich ETX_513-515 User Manual
Page 6
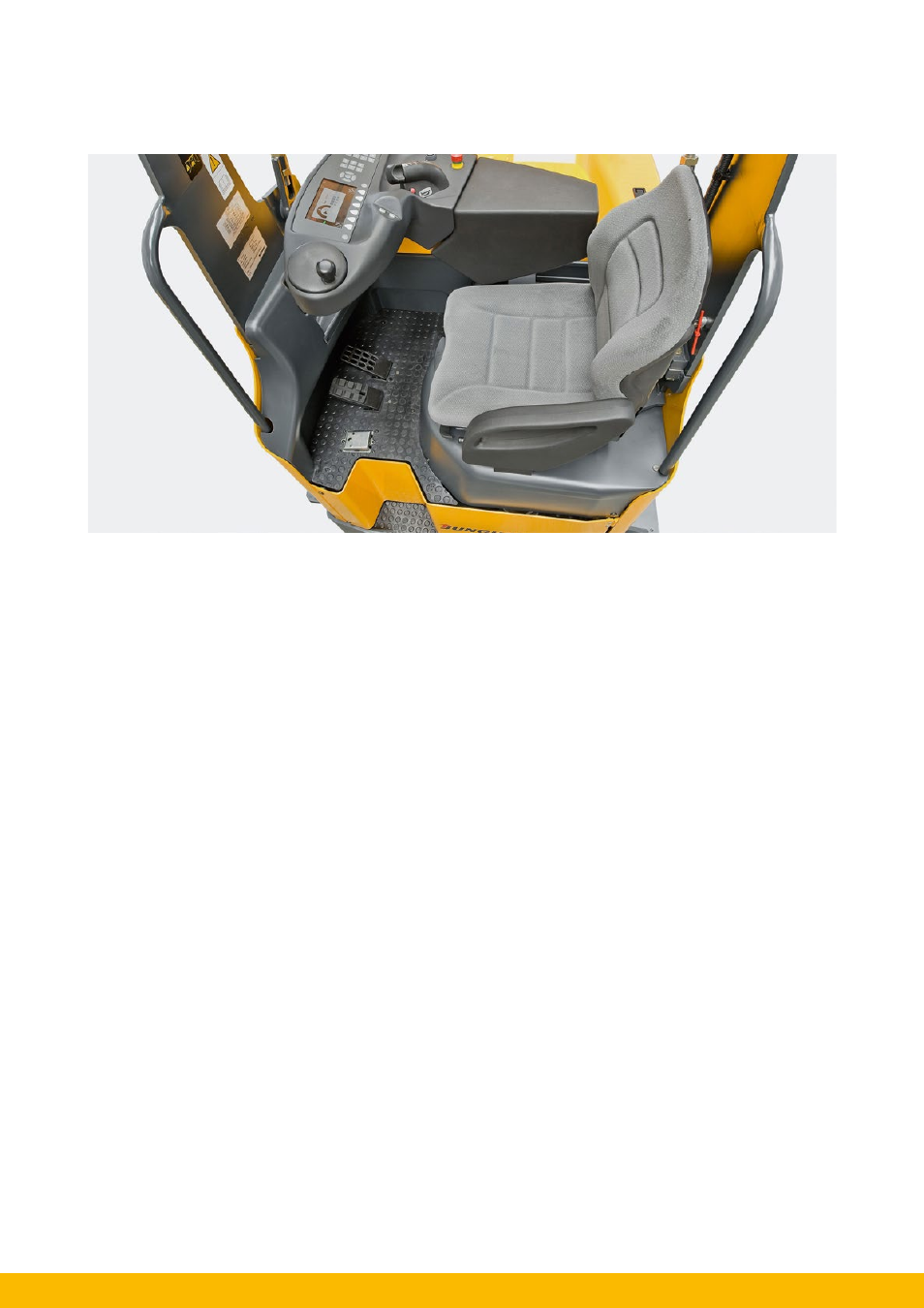
ETX 513/515
ETX standard equipment
• Sprung, adjustable and weight-adjusta-
ble operator seat with armrests.
• Pivoting operating module with over-
head guard.
• Operating console adjustable in height
and distance to the operator.
• Graphics-compatible display with
function keys for status and service
displays.
• Effortless, precise manoeuvring with
electronic power-assisted steering.
• Camera/colour monitor system (5.6”)
for reliable stacking and retrieval.
• Integrated rack height select without
no load sensor.
• Diagonal travel with optimum speed
profile (dependent on travel direction).
• Gentle movement at best efficiency
due to stepless speed control of all
drives.
• Electromagnetic spring-loaded brake
acts on load and drive wheel.
• End position and transfer cushioning of
all hydraulic functions.
• Manually overlaid swivelling/sideshift.
• Integrated diagnostic system with dis-
play and service interface.
• Energy recovery while braking and
lowering.
• CAN-Bus networked controllers.
• Two RFID readers for load and drive
direction.
ETX optional equipment
• ‘Lifting and sideshift’ performance
module.
• Modular telescopic forks in various
designs (standard or flat design).
• Symmetrical fork positioner for lifting
loads of different sizes.
• Asymmetrical fork positioner, adjust-
ment to load size and sideshift for
comfortable picking.
• Mechanical rail guidance in different
designs.
• Wire guidance for precise control in
the aisle with no mechanical loading of
components.
• Enclosed cab (glass version).
• Synchronised swivelling in or outside
the aisle (automatic process).
• Heating in foot-well.
• Radio with CD player and MP3 inter-
face.
• Modular system of lift / travel and
lower cut-outs.
• End of aisle control with speed
reduction.
• Integrated Jungheinrich personal
protection system (PPS optional), fac-
tory-fitted integration into the safety
computer.
• Impact protection (mixed operation of
two trucks in the aisle)
Warehouse navigation for semi-auto-
matic approach within the aisle.
• LED working lights and LED interior
lighting.
• Converters in different designs (e.g.
power supply terminals, printer etc.).
• DIN A4 writing pad.
• Document holder.
• Rack height select plus automatic
stacking with active reach control.
• Optional no load sensor in the fork tips
or on load handler.
• Jungheinrich radio data terminals with
mechanical and electrical interfaces for
material flow management systems.
• Laser scanner including bracket.
• Jungheinrich Information System for
Truck Management (ISM).
Guidance systems in narrow aisles
ensure high performance
Guidance systems guarantee safe truck
operation and provide the best solution
for high performance and high travel
speed. They reduce the space required
due to the extremely low clearance be-
tween truck and racking and significantly
reduce strain on the operator.
The advantages of wire guidance
• Automatic, rapid alignment and guid-
ance of the truck (with 125 mm safety
clearance) without mechanical stress.
• Approaching the guide wire up to an
angle of almost 90°.
• Parameterisation of up to six different
frequencies.
• Modulation (e.g. unblock frequency) of
up to three frequencies.
• Continuously level floor. Advantages:
Easy cleaning and high level of flexibil-
ity regarding the trucks to be used.
The advantages of mechanical guidance
• Narrow aisle widths due to narrow
safety clearance (100 mm).
• High travel speed.
• Optional with low/high or cast/not cast
rails.
• Lower investment costs for smaller
warehouses.
Built-in charger and busbar
Wherever high throughputs are required
in two or three-shift operations, busbar
systems have really proven themselves:
• Power supply of the truck and charging
the battery in narrow aisles.
• Built-in charger.
• Three-shift operation without having to
change the battery.
• No replacement batteries, no charging
station, no time lost replacing batteries.
• Closed busbar for optimum protection
and low contamination.
• Low installation height due to open
busbar.