Cashco C27 - C53 Actuator User Manual
Page 4
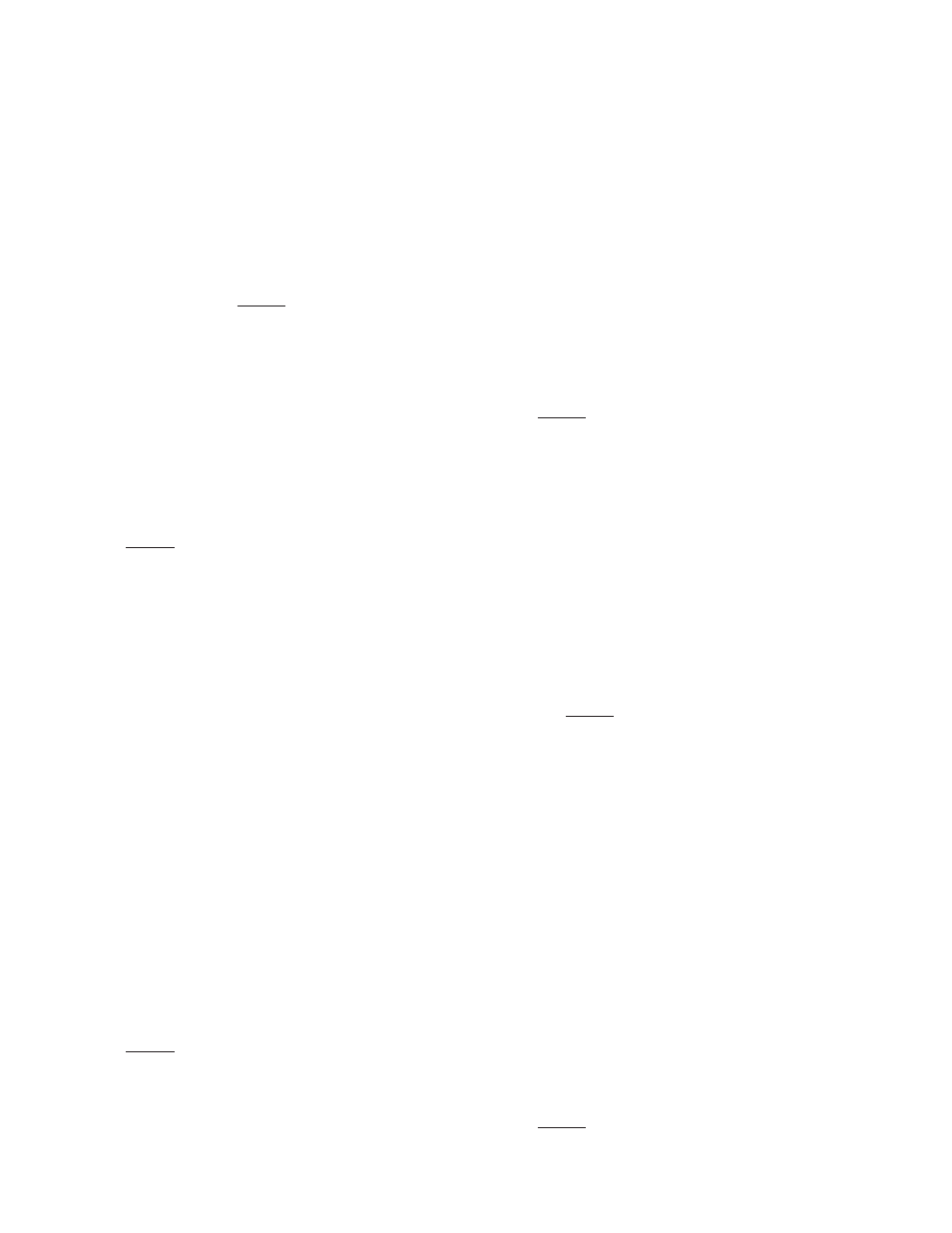
4
4
IOM-C27-C53
IOM-C27-C53
28. Refer to B.3 previous, align top and bottom
cases (1,2). Install long bolting (19) and nuts
(21) equally spaced around the bolt circle -
fi nger tight.
29. Install remaining short bolts (18) and nuts
(20). Torque all bolting to 75 in-lbs.
30.
Thread upstop fl ex nut (52) [coupling assem-
bly (33) for handwheel option] CW onto the
actuator stem (6) and engage until just past
stem fl ats. NOTE: Upstop position cannot
be set until actuator is mounted on the body
and the bench range is set.
C. Changing Action from Direct to Reverse; i.e.
From ATC to ATO.
NOTE: Not necessary to remove actuator as-
sembly from body assembly, unless supplied
with Handwheel Assembly.
1. Follow steps from B.1 thru B.5 then continue
as follows.
NOTE: DO NOT rotate actuator stem (6) or body
stem.
2. Secure both stem jam nuts with wrenches
and rotate the lower nut fi rst down to thread
base of the stem, followed by the upper nut.
3. Secure
the
fl ats on the lower end of the actua-
tor stem (6) with a wrench. With a second
wrench rotate the upstop fl ex nut (52) CCW 5
revolutions. (Required to help release spring
preload when stem bolt (12) is removed.)
4. Remove top case (1). Re-secure the fl ats on
stem and with a 9/16” socket wrench rotate
bolt (12) CCW and remove.
5. Lift out lock washer (22), diaphragm washer
(14) and O-ring (15). Remove diaphragm (7).
6. Remove diaphragm plate (8), spring plate
(9), stem spacer (5) and springs (10).
7. With hand pressure - push stem (6) down to
where bottom of stem (6) aligns with the “C”
close mark on the indicator plate (23.
NOTE: DO NOT rotate actuator stem (6) or body
stem while plug is touching the seat surface.
8. Re-assemble by placing diaphragm washer
(14) “o-ring side up” and new o-ring (15) on
attachment hub (4).
9. Place the diaphragm plate (8) inside the
diaphragm (7) and carefully center both on
the diaphragm washer (14). Align bolt holes
in diaphragm with holes in lower case.
10. Align center holes in the spring plate (9) and
stem spacer (5) with the center hole of the
diaphragm plate (8).
11. Apply Loc-tite #242 to stem bolt (12) threads
and insert down through stacked parts.
Rotate CW to engage threaded end of stem
(6). Secure the fl ats on the lower end of the
actuator stem (6) with a wrench. Tighten
stem bolt (12) to actuator stem (6) with 35
ft-lbs. torque.
NOTE: DO NOT rotate actuator stem (6) or body
stem while plug is touching the seat surface.
12. Place springs (10) equally spaced around
the spring plate (9).
13. Refer to B.3 previous, align top and bottom
cases (1,2). Install long bolting (19) and
nuts (21) equally spaced around the bolt
circle - fi nger tight.
14. Install remaining short bolts (18) and nuts
(20). Torque all bolting to 75 in-lbs.
15.
Rotate upstop fl ex nut (52) CW up the
actuator stem (6) until just past stem fl ats.
NOTE: Upstop position cannot be set until
the bench range is set.
16. Lift indicating washer up to bottom of stem
(6) and thread both jam nuts up secure
underneath the indicating washer.
D. Changing Action from Reverse to Direct; i.e.
From ATO to ATC.
NOTE: Not necessary to remove actuator as-
sembly from body assembly, unless supplied
with Handwheel Assembly.
1.
Follow steps from B.1 thru B.5, then continue
as follows.
2. Remove top case (1) and springs (10).
3. Secure the fl ats on stem (6) and with a
9/16” socket wrench rotate bolt (12) CCW
to remove.
NOTE: DO NOT rotate actuator stem(6) or body
stem while plug is touching the seat surface.