Warning – Cashco C27 - C53 Actuator User Manual
Page 2
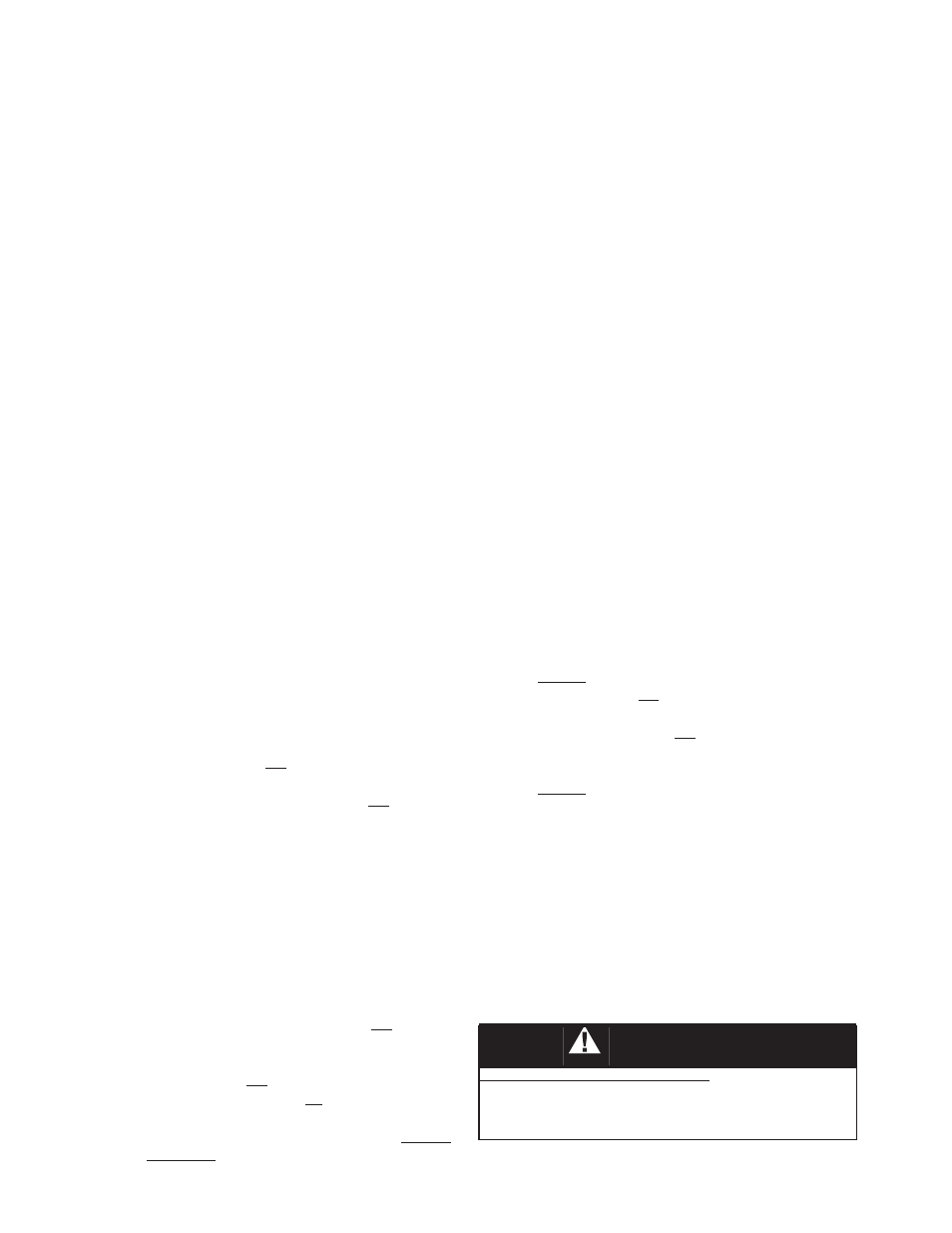
2
2
IOM-C27-C53
IOM-C27-C53
SECTION III
III. INSTALLATION
A. Orientation:
1. Recommended actuator major axis orientation
with any model of Cashco control valve body,
is upwards in a horizontal pipe.
2. Actuator axis may be horizontal when valve
is in a vertical pipe.
3. Outdoors, all installations must be oriented
any angle from horizontal-to-vertical.
4. Models C27 and C53 actuators are not recom-
mended for installation oriented downwards
in either “D” or “R” action.
5. In no case is additional weight to be applied
to the actuator when installed in an orientation
other than vertical; i.e. the valve is unsafe as
a “step” to support personnel.
B. Air Supply:
1. Recommendation is that a desiccant dried,
instrument quality air supply be used.
Such a supply is recommended for out-
doors installations, and is required in ar-
eas of freezing weather conditions.
2. If air supply contains moisture and/or lu-
bricating oil, the air should be fi ltered with
a coalescing type of fi lter prior to use in
stroking the actuator.
3. Failure to remove moisture will cause cor-
rosion to internals of casings (1,2).
4. Connections for the air supply are 1/4” fe-
male NPT. A suitable pipe thread sealant
is recommended to be used when install-
ing the pipe or tube fi tting. Exhibit care to
prevent the sealant from getting inside the
tube/pipe.
SECTION IV
IV. MAINTENANCE
A. General:
1. Hereafter, all maintenance, disassembly,
etc., is assumed to be done in an indoor
shop.
2. An actuator assembly (AA) is unitized with a
body assembly (BA). Reference should be
made to the body IOM for instructions about
the specifi ed body assembly (BA) utilized
with the actuator.
3. Where the body is not being removed from
the actuator, special care MUST be exhib-
ited to prevent valve stem rotation during
any disassembly or reassemble for all valve
models. Following this procedure will ensure
not damaging seating surfaces.
4. Remove instrument tubing, airset, positioner,
and any other accessory that maybe mount-
ed on the control valve unit (AA, BA).
5. All indicated Item Numbers that are with re-
spect to body (BA) IOM will be in parenthesis
and underscored; i.e. (20); the same is true
for positioner parts. All Item Numbers that
are with respect to this manual are not un-
derscored; i.e. (19).
B. Diaphragm Removal/Replacement:
NOTE: Actuator (AA) must be separated from
the body (BA) in order to replace O-rings
(15, 16 &17) and diaphragm (7). Refer to
specifi ed body (BA) IOM for instructions to
remove actuator (AA).
NOTE: If actuator (AA) has Handwheel refer to
Step E and remove.
1. Secure the yoke (3) in a vise. Orient with
the (AA) upwards.
2. All air pressure must be released from the
actuator casings (1,2).
3. Take note of alignment of supply ports on
top and bottom cases (1,2); used to assist
with ori en ta tion when actuator is re- as sem-
bled.
SPRINGS UNDER COMPRESSION! To relax spring com-
pression remove case bolting equally in an alternating
pattern. Ensure that all "short" bolting is removed
fi rst.
WARNING